Saving and restoring user settings, Module limit, Inputs – Watlow EZ-ZONE RM Limit Module Rev C User Manual
Page 82: Calibration offset, Calibration
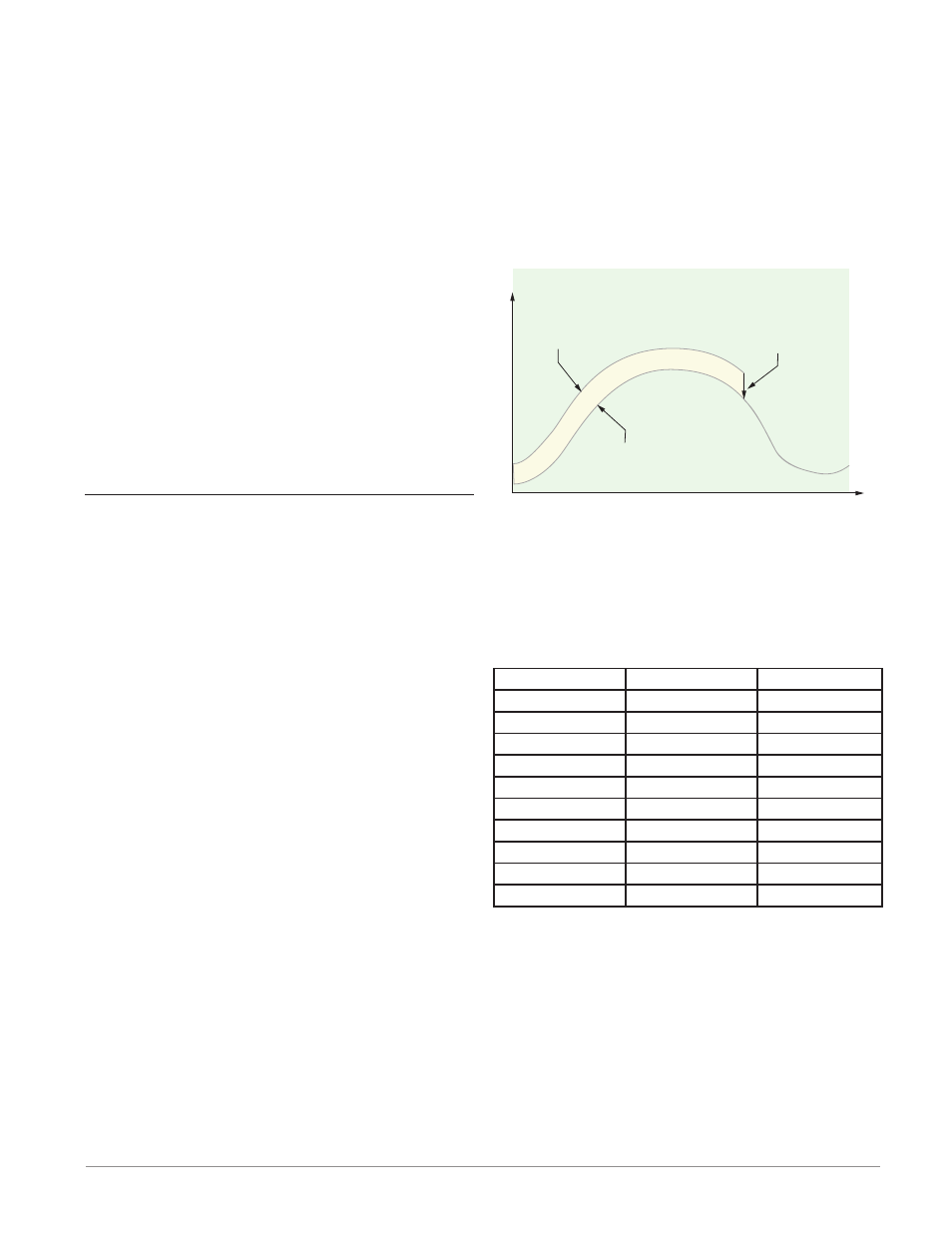
Watlow EZ-ZONE
®
RML Module
•
79
•
Chapter 6 Features
Saving and Restoring User Settings
Recording setup and operations parameter settings
for future reference is very important. If you uninten-
tionally change these, you will need to program the
correct settings back into the controller to return the
equipment to operational condition.
After you program the controller and verify prop-
er operation, use User Save Set [USr;S] (Setup Page,
Global Menu) to save the settings into either of two
files in a special section of memory. If the settings in
the controller are altered and you want to return the
controller to the saved values, use User Restore Set
[USr;r]
(Setup Page, Global Menu) to recall one of
the saved settings.
A digital input or the Function Key can also be
configured to restore parameters.
Note:
Only perform the above procedure when you are
sure that all the correct settings are programmed
into the controller. Saving the settings overwrites
any previously saved collection of settings.
Be sure to document all the controller settings.
Module Limit
This feature allows the user to setup a single output
to reflect an energized (safe) or deenergized (tripped)
state for the module. The reference to an energized
or deenergized state refers to the internal coil that
drives the Form A relay. When energized (safe) the
contact is closed, when deenergized the contact is
open. If any configured limit is tripped (process value
exceeds set point or limit input has malfunctioned),
the output LED assigned to serve as this function
will come on. By default (factory settings), output 8 is
assigned this function where any output of choice can
be configured as such.
Note:
If limit loops exist on the module that are not in-
tended to be used immediately, the loop must be
setup to avoid a trip condition. To do this simply
jumper the input for the unused loops and then en-
sure that the set point will never be exceeded (Op-
erations Page, Limit Menu) by the process variable.
Inputs
Calibration Offset
Calibration offset allows a device to compensate for
an inaccurate sensor, lead resistance or other factors
that affect the input value. A positive offset increases
the input value, and a negative offset decreases the
input value.
The input offset value can be viewed or changed
with Calibration Offset [`i;CA] (Operations Page,
Analog Input Menu).
Time
Temperature
Temperature Reading
from Sensor
Actual Process Temperature
Negative Calibration Offset will
compensate for the difference
between the Sensor Reading and
the Actual Temperature
Calibration
To calibrate an analog input, you will need to provide
two electrical signals or resistance loads near the ex-
tremes of the range that the application is likely to
utilize. See recommended values below:
Sensor Type
Low Source
High Source
thermocouple
0.000 mV
50.000 mV
millivolts
0.000 mV
50.000 mV
volts
0.000V
10.000V
milliamps
0.000 mA
20.000 mA
100 Ω RTD
50.00 Ω
350.00 Ω
1,000 Ω RTD
500.00 Ω
3,500.00 Ω
Thermistor 5K
50.00 Ω
5000.00 Ω
Thermistor 10K
50.00 Ω
10000.00 Ω
Thermistor 20K
50.00 Ω
20000.00 Ω
Thermistor 40K
50.00 Ω
40000.00 Ω
Follow these steps for a thermocouple or pro-
cess input:
1. Apply the low source signal to the input you are
calibrating. Measure the signal to ensure it is ac-
curate.
2. Read the value of Electrical Measurement [`Mu]
(Factory Page, Calibration Menu) for that input.
3. Calculate the offset value by subtracting this val-
ue from the low source signal.
4. Set Electrical Input Offset [ELi;o] (Factory Page,
Calibration Menu) for this input to the offset val-
ue.