IAI America RCM-GW-PR User Manual
Page 96
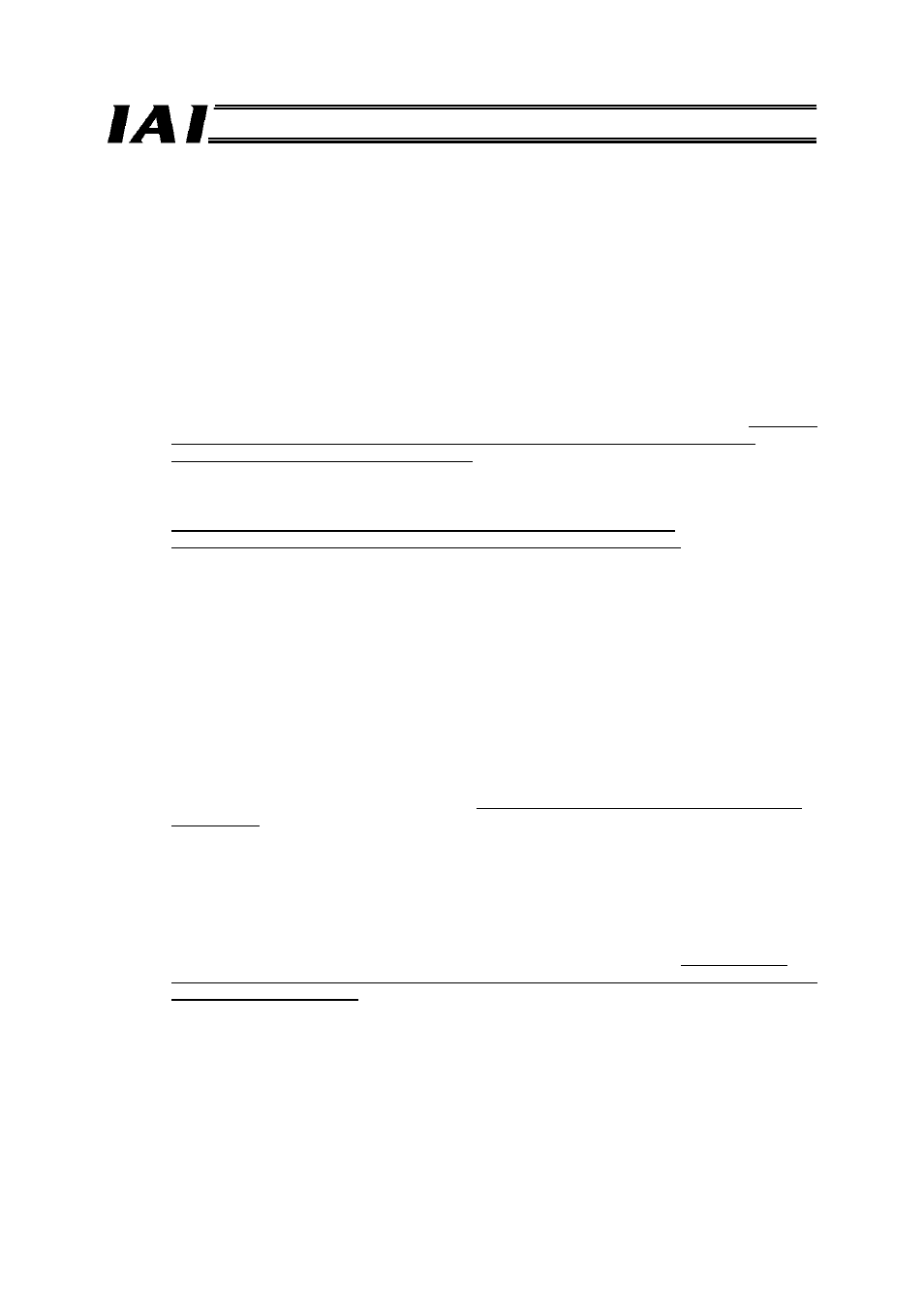
90
PfofiBus Gateway
(4) Operation in the direct numerical specification mode
The actuator is operated not by using the position table of the controller, but by writing the target
position data, acceleration/deceleration data, speed data, push-current limiting value data and
positioning band data to the link registers in the PLC.
All these data must be set in the case of push-motion operation.
In the case of normal positioning operation, the push-current limiting value data, PUSH signal and
DIR signal are not required.
Take note that in either operation, the actuator will not move unless all necessary data is set.
Operation
[Push-motion operation]
[1] Set the push start position data in the target position data specification register.
[2] Set the speed data until the push start position in the speed specification register, and set the
corresponding acceleration/deceleration data in the acceleration/deceleration register. Take note
that even if acceleration/deceleration is not set, the setting of parameter No. 9, “Default
acceleration/deceleration” will not be applied.
[3] Set the push-motion travel in the positioning band specification register. (*)
[4] Set the push-current limiting value data in the push-current limiting value register in order to set
the push force.
[5] Turn the PUSH (push-motion operation mode specification) signal “1” (ON).
[6] Use the DIR (push direction specification) signal to select the push direction.
When the DIR signal is set to “1” (ON), push-motion operation is performed in the direction
opposite home. When the signal is set to “0” (OFF), push-motion operation is performed in the
direction of home.
[7] Next, turn the start command (CSTR) signal “1” (ON) after confirming that the positioning
complete (PEND) signal is “1” (ON).
The data set in [1] to [4] will be read by the controller at the “0” (OFF)
Æ “1” (ON) edge of CSTR
(leading edge of the signal).
[8] PEND turns “0” (OFF) tdpf after CSTR has turned “1” (ON).
[9] Turn CSTR “0” (OFF) after confirming that the PEND signal has turned “0” (OFF) or MOVE
signal has turned “1” (ON).
[10] MOVE turns “1” (ON) simultaneously as PEND turns “0” (OFF) or within 1 Mt thereafter.
[11] PEND turns “1” (ON) when the motor current reaches the push-current limiting value set in [4]
while CSTR is “0” (OFF). (The push operation has completed.)
If the motor current does not reach the push-current limiting value set in [4] even after the
positioning band set in [3] has been reached, the PSFL (missed load in push operation) signal
turns “1” (ON). In this case, PEND will not turn “1” (ON). (The actuator has missed the load.)
[12] The current position data is constantly refreshed.
[13] Turn PUSH “0” (OFF) after PEND or PSFL has turned “1” (ON).
* Take note that even if positioning band specification data is not set, the value of parameter
No. 10, “Default positioning band” will not be applied.
[Normal positioning operation]
In the case of normal operation, the operation continues while the PUSH signal is still “0” (OFF)
in [5] above. Setting of push-current limiting value data in [4] is not required. PEND turns “1”
(ON) when the remaining travel falls within the range of positioning band specification data set in
[3], while CSTR is “0” (OFF).