Address configuration of gateway unit, 1 position number specification mode – IAI America RCM-GW-PR User Manual
Page 41
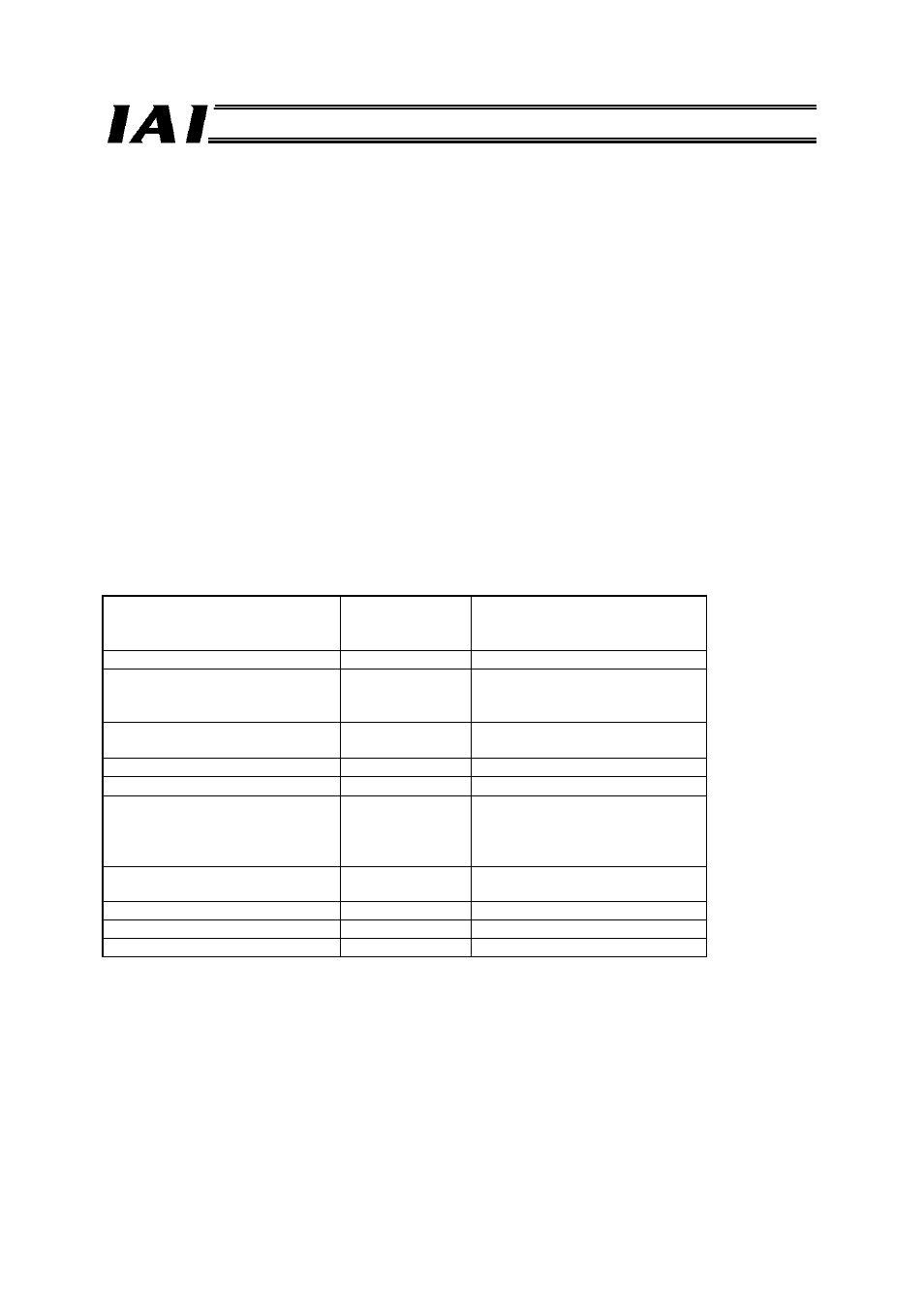
35
PfofiBus Gateway
5. Address Configuration of Gateway Unit
All data exchanged between the master station and the controller are tentatively stored in the internal
memory of the Gateway Unit, and then transmitted cyclically. Accordingly, the PLC program recognizes
these data as remote ProfiBus I/Os.
Up to 16 ROBO Cylinder controllers can be connected to the Gateway Unit, with the connected controllers
assigned an axis number of 0 to 15, respectively. The Gateway Unit simultaneously sends and receives
data to/from the master station for all ROBO Cylinder controllers connected via SIO link.
As explained in the features of the Gateway unit in section 1.4, controllers can be operated in there major
modes.
In each mode, an address configuration varies as the slave.
5.1 Position Number Specification Mode
In this operation mode, a desired position number in the position table is specified to operate the actuator,
and up to 16 axes can be controlled. The position table must be set for each axis using the PC software or
teaching pendant.
A desired position number is written in the PLC to operate the actuator.
Up to 64 positions from Nos. 0 to 63 can be specified, but the number of positions may be limited
depending on the PIO pattern (PIO pattern selection parameter) specified for each axis.
(Refer to the table in 1.4.2.)
The key functions that can be controlled in this mode are summarized in the table below.
Key function
{: Direct control
∆: Indirect control
X: Disabled
Remarks
Home return operation
{
Positioning operation
∆
This operation is performed by
specifying a number in the
position table.
Speed and
acceleration/deceleration setting
∆
Set in the position table.
Pitch (incremental) feed
∆
Set in the position table.
Push-motion operation
∆
Set in the position table.
Speed change during movement
∆
This operation is performed by
combining two or more position
numbers. (Refer to the operation
manual for the controller.)
Operation with acceleration and
deceleration set differently
∆
Set in the position table.
Pause
{
Zone signal output
{
Each zone is set by parameters.
PIO pattern selection
X
*1
*1 Since the number of position is limited according to the PIO pattern selection (parameter No. 25)
specified for each connected controller, specify the position numbers in a manner avoiding
inconsistency. For your information, up to 64 positions can be specified.