Franklin Fueling Systems T5 Series Fuel Management System Programming Guide User Manual
Page 42
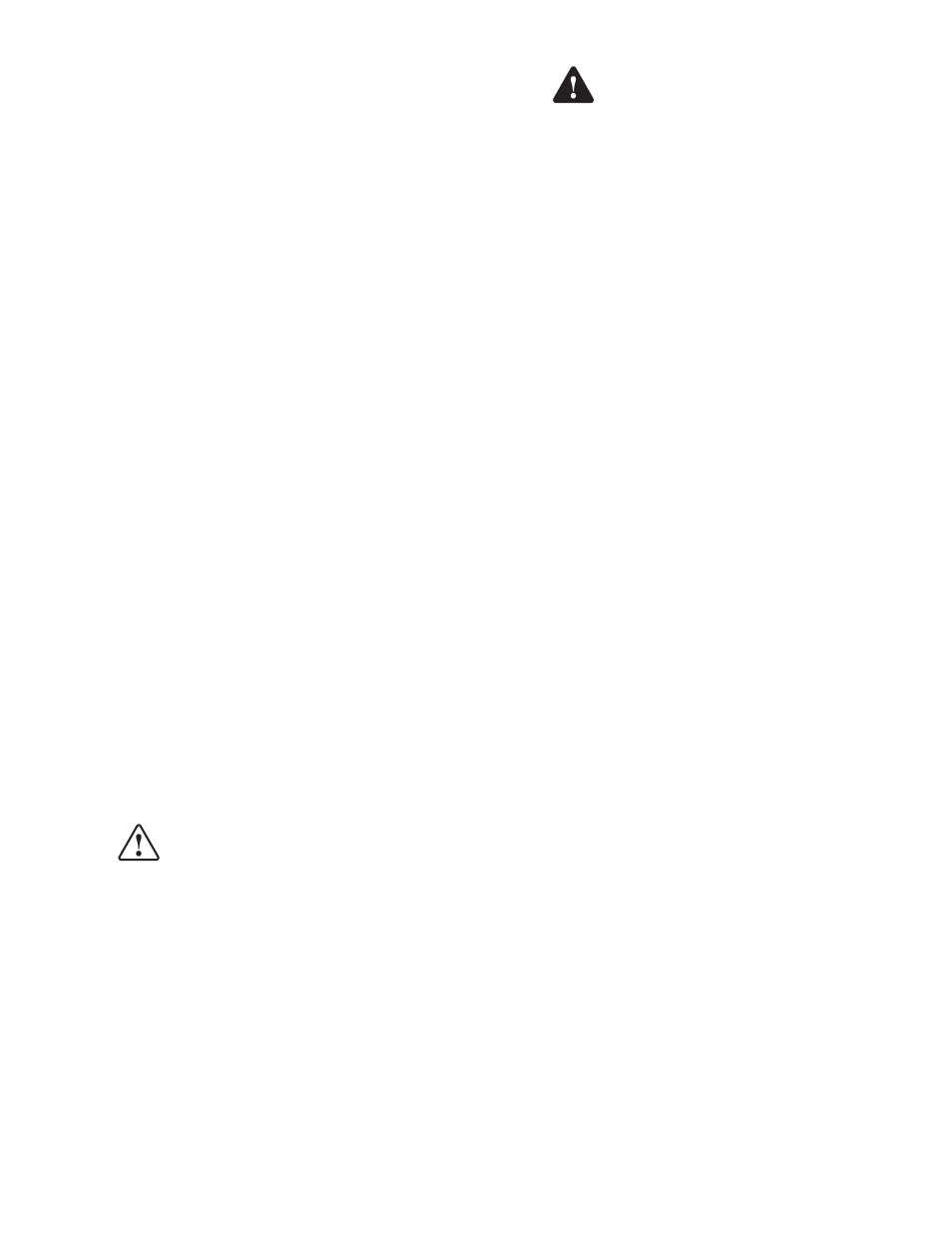
38
Tank Leak Test Results
Leak test results are either
increase, passed, failed, or
indeterminate.
Reasons Why Tank Leak Tests Fail
• The tank leaks.
• Temperature instability – temperature variations of the
product within the tank after a delivery is the most com-
mon source of interference and failed leak tests / false
alarms (a failure to detect real leaks can also result).
Look at the hourly temperature data on the leak test re-
port and retest if the variation is more than a few tenths
of a degree.
• Large changes in product temperature from the start to
the end of the test.
• Water Level changes during the test.
• Evaporation and loss of product through the vent
stack will look exactly like a leak. Evaporation can be
a problem during high seasonal temperatures and/or
high winds, and when liquid level exposes the greatest
surface area for evaporation (half full tanks are worse).
Seasonal variations in product composition, size of the
tank (larger is worse), and tank vent configuration are
also evaporation factors.
• Tank Deformation -- the tank changes shape after a
large product delivery.
• Tidal Action – in coastal communities, groundwater lev-
els maybe be affected, and, as a result, may deform the
tank. During certain times of the day, the tide changes
inconsistently.
• Tank Cross-Talk – level changes in one tank causes a
level change in an adjacent tank or compartment.
• Product is being dispensed during a test.
Steps to Take When a Tank Leak Test Fails
Leak tests do occasionally fail and a single failed leak test
should not be a cause for great concern. Remember, if the
confidence level of the test is 99%, there is a 1% chance
that the system will give a false answer.
Caution
Don’t excavate / repair a tank because
of a single failed leak test. Reference
your site policy and procedures plan.
If you fail a leak test, review the leak test report to
determine if there is an obvious source of interference with
the test (see the Causes of Leak Test Failures section for
an example of a Tank Leak Test Report). If such a source
of interference is identified, retest the tank as soon as
possible. Retest the tank to validate or invalidate the first
test result if no source of interference can be identified. If
necessary, run several tests.
If repeated tests indicate a leak and no obvious source
of interference is found, then immediately have the
tank precision / pressure tested. If the precision test
confirms the presence of a leak, then the tank owner
must take corrective action in accordance with federal,
state and local regulations.
Warning
The owner of the tank is legally
obligated to comply with reporting and
procedural requirements of federal,
state and local regulations. These
must be followed explicitly. Serious
legal, health and safety hazards could
result from not taking immediate and
proper action. If codes and regulations
conflict with this manual, follow the
regulations set by governing agencies.
SCALD Tank Leak Tests
SCALD (Statistical Continuous Automatic Leak Detection)
is optional on Franklin Fueling Systems tank gauges. It
runs 24 hours a day and is used to perform 0.2 gph tests
on tanks that are always in use.
SCALD works by collecting Quiet Intervals (QIs) in
between dispensing. A QI is obtained when a thermally
stable tank is idle for 20 minutes with no dispensing, no
deliveries and no other movement of the probe floats.
Once four QIs are collected, the Automatic Tank Gauge
(ATG) will analyze the data and either Pass, Fail, Increase
or discard that test because the data is not statistically
sound. Four QIs can be collected over a period of several
days or weeks.
• If the result is a Pass, then a test result of Pass will be
generated.
• If the result is Fail or Increase, then another test will be
run to ensure that this is not a false alarm. Three Failed
or Increase tests in a row will produce a test result of
Failed or Increase.
• If the data is not statistically sound, then the test is dis-
carded. No new test result will be generated and SCALD
will continue to run. The fact that a result was discarded
is recorded and can be seen in the Status number that
accompanies the next generated test result.
• On rare occasions certain conditions can arise that can
prevent SCALD from getting enough QIs to complete a test.
Reasons Why SCALD Tank Tests may Fail
• Temperature
• If a site receives deliveries where the temperature of the
fuel being delivered is several degrees different then the
fuel in the tank, then SCALD will not be able to collect
QIs due to thermal instability. The temperature of the
fuel can not change more than .01°F during a 20 min QI.
• If a pump control relay is stuck closed and the pump is
running all of the time, the temperature in the tank can
be much higher than the other tanks. Due to this high
temperature and the fact that the pump is running and
causing turbulence in the tank, no QIs will be collected.
• No Quiet Time
• SCALD needs four 20 minute QIs in order to complete
a test. These QIs are normally found in the early morn-
ing hours. If a site is so busy that there are no 20 minute
periods of no dispensing, then SCALD will not be able to
complete a test.