Yaskawa MP3200 Troubleshooting Manual User Manual
Page 62
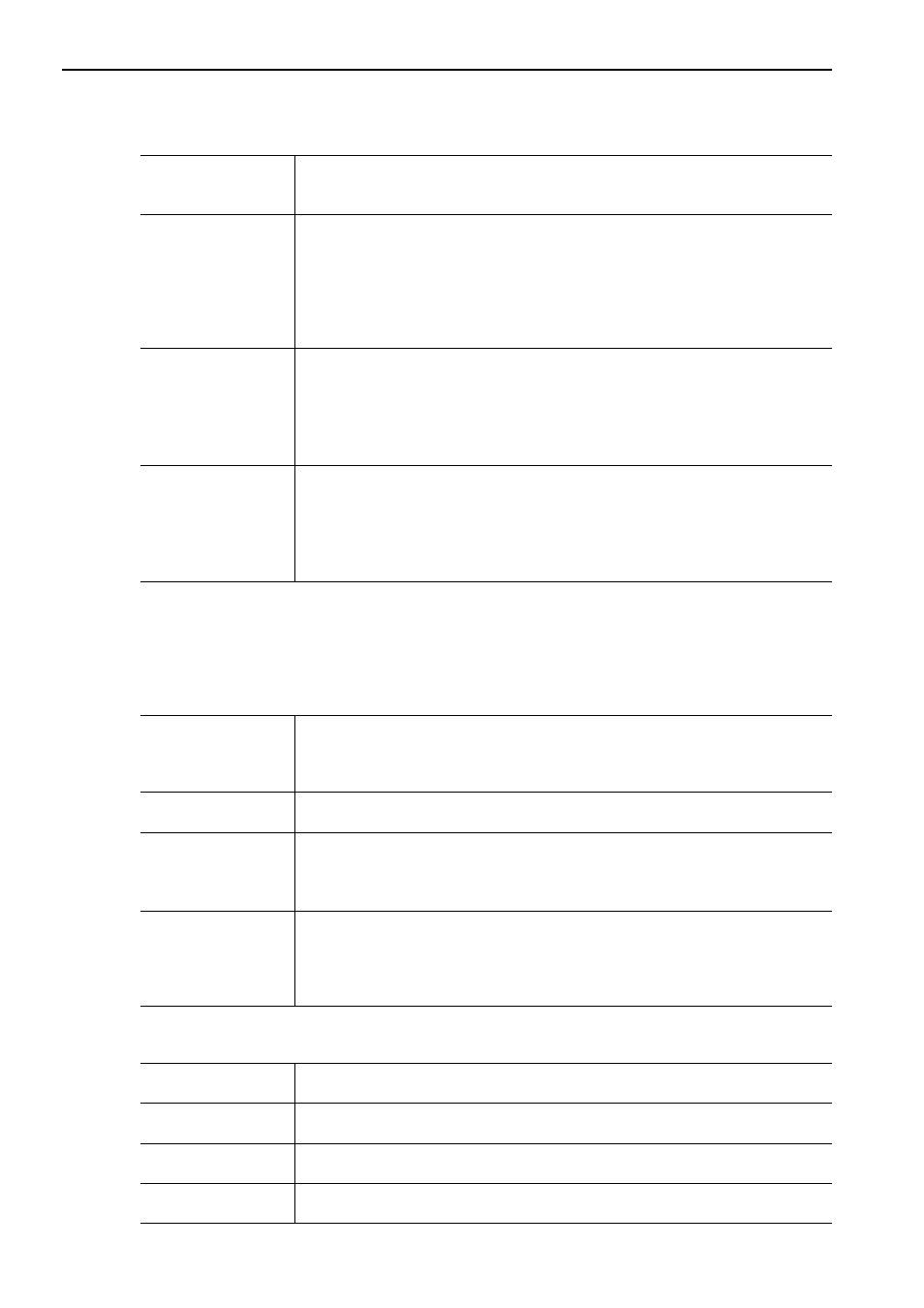
4.2 Troubleshooting Motion Errors
Troubleshooting Motion Errors
4-12
Bit 1: Positive Overtravel and Bit 2: Negative Overtravel
Note: For a vertical axis, we recommend that you make the following settings in the SERVOPACK to prevent falling or
oscillation at the overtravel boundary.
• Using an emergency stop to decelerate to a stop
• Implementing a zero clamp after decelerating to a stop
Bit 3: Positive Software Limit and Bit 4: Negative Software Limit
Bit 5: Servo OFF
Detection Timing
These alarms are detected by the position control section during execution of a motion
command (always).
Overtravel detection is enabled while the OT signal in travel direction is OFF.
Processing When
Alarm Occurs
• Stop processing is performed in the SERVOPACK.
The stop method and the operation after stopping depend on the SERVOPACK param-
eter settings.
Bit 3 (Command Error End) in IW09 (Motion Command Status) turns ON.
• Controller Processing
The command is canceled and the axis decelerates to a stop. Followup processing to
align the command position with the current machine position is performed.
Details and Cause
Any of the following is possible.
• A command was issued that caused a travel limit of the machine to be exceeded for one
of the following:
A command from a user program
Manual operation that exceeds the travel limit
• An error in the overtravel signal
Correction
• Check the following items:
Check the overtravel signal.
Check programmed and manual operation.
• After checking the above items, clear the motion command code and reset the alarm.
Then return the axis to eliminate the overtravel condition. (Commands in the overtravel
direction will be disabled. If you attempt to execute one, the alarm will occur again.)
Detection Timing
Detection is enabled when a motion command is used. These alarms are detected by the
position control section.
Detection is enabled after completion of a Zero Point Return or a Set Zero Point com-
mand.
Processing When
Alarm Occurs
The axis decelerates to a stop at the software limit.
Bit 3 (Command Error End) in IW09 (Motion Command Status) turns ON.
Details and Cause
A command was issued that caused a software limit to be exceeded for one of the follow-
ing:
• A command from a user program that exceeds the travel limit
• Manual operation that exceeds the travel limit
Correction
• Check programmed and manual operation.
• After checking the above item, clear the motion command code and reset the alarm.
Then return the axis to within the software limit. (Commands in the direction of the
software limit will be disabled. If you attempt to execute one, the alarm will occur
again.)
Detection Timing
This alarm is detected when a movement command is attempted when the power to the
Servomotor is OFF.
Processing When
Alarm Occurs
The movement command is not executed.
Bit 3 (Command Error End) in IW09 (Motion Command Status) turns ON.
Details and Cause
A movement command (Positioning, External Positioning, Jog, or STEP Operation) was
issued when the power to the Servomotor was OFF.
Correction
Clear the motion command code, reset the alarm, and then turn ON the power to the Ser-
vomotor.