Moniteur 50 Series SMART Positioners User Manual
Page 77
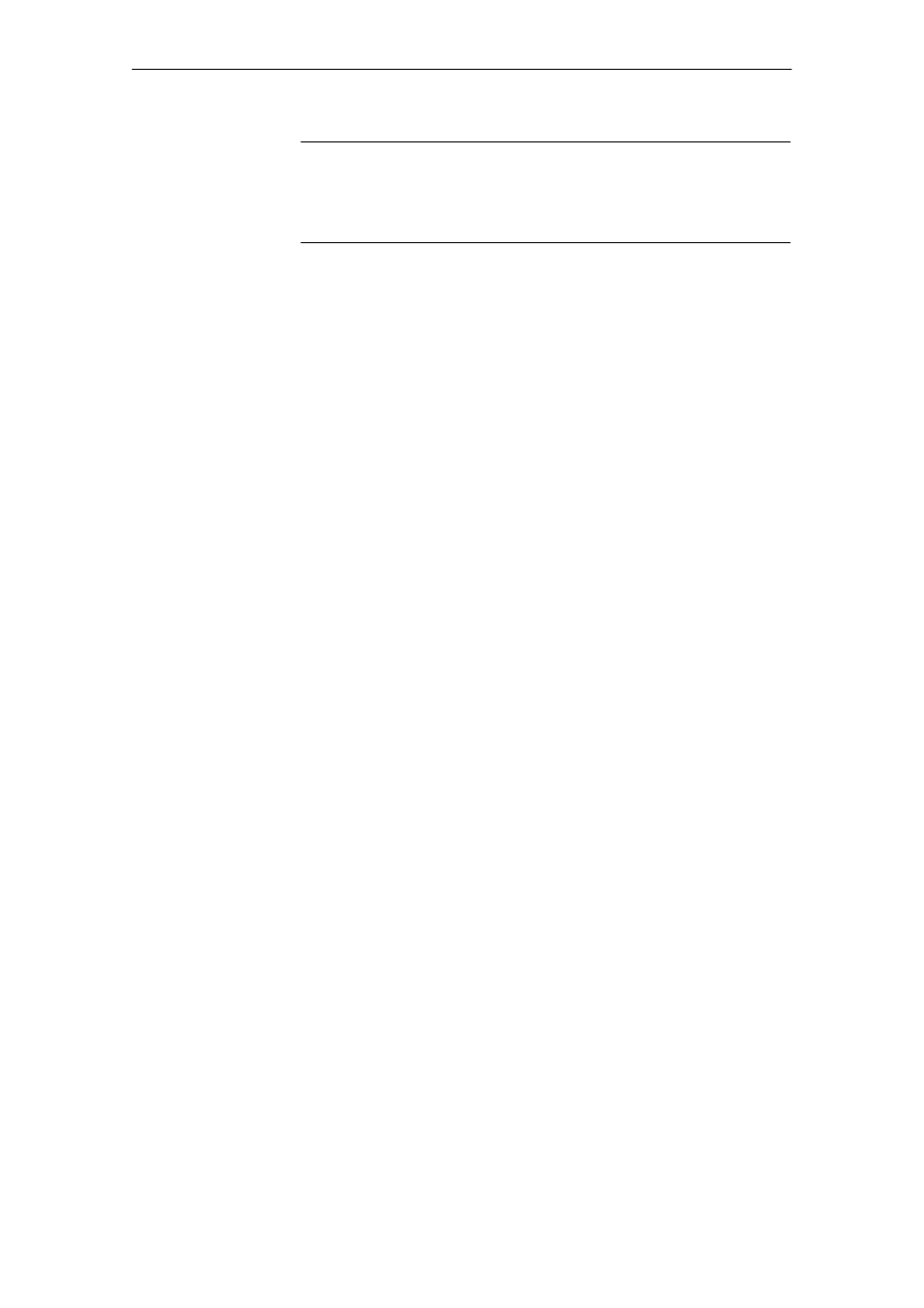
Operation
4-15
Positioner SIPART PS2/SIPART PS2 PA
C79000-G7476-C150–01
☞
Note
The setting for YWAY must correspond to the mechanical leverage
ratio. The driver must be set to the value of the actuator travel or, if
this value is not scaled, to the next largest scaled value.
Initialization
Automatic initialization is started when you select “Strt” and press the
increment key (> 5 s). Initialization is displayed by “RUN 1” to “RUN 5”
(see Fig. 3-22 to Fig. 3-24) as it progresses.
Setpoint direction (see Fig. 4-5)
The setpoint direction setting is used to reverse the direction of the set-
point. It is primarily used for split–range operation and single–acting
drives with the safety setting “up”.
Setpoint ramp OPEN
and
Setpoint ramp CLOSE
The setpoint ramp takes effect in automatic mode and limits the rate of
change of the active setpoint. When the instrument is switched from
manual mode to automatic mode the active setpoint is matched to the
setpoint on the instrument via the setpoint ramp.
This bumpless changeover between manual and automatic avoids
overpressures in long pipes.
In setting TSI = Auto the slower of the two actuating times determined
during initialization is used for the setpoint ramp. TSD then has no ef-
fect.
Setpoint function
With this function, non–linear valve characteristic curves can be lineari-
zed and on linear valve characteristic curves, any flow characteristics
can be emulated.
Seven valve characteristic curves are stored in the instrument
❑
linear
(8.SFCT = Lin, factory setting)
❑
equal percentage
1 : 25
(8.SFCT = 1:25)
❑
equal percentage
1 : 33
(8.SFCT = 1:33)
❑
equal percentage
1 : 50
(8.SFCT = 1:50)
❑
inverse equal percentage
25 : 1
(8.SFCT = n1:25)
❑
inverse equal percentage
33 : 1
(8.SFCT = n1:33)
❑
inverse equal percentage
50 : 1
(8.SFCT = n1:50)
❑
freely adjustable
(8.SFCT = FrEE)
4.INIT
5.SDIR
6.TSI
7.TSD
8.SFCT