Moniteur 50 Series SMART Positioners User Manual
Page 25
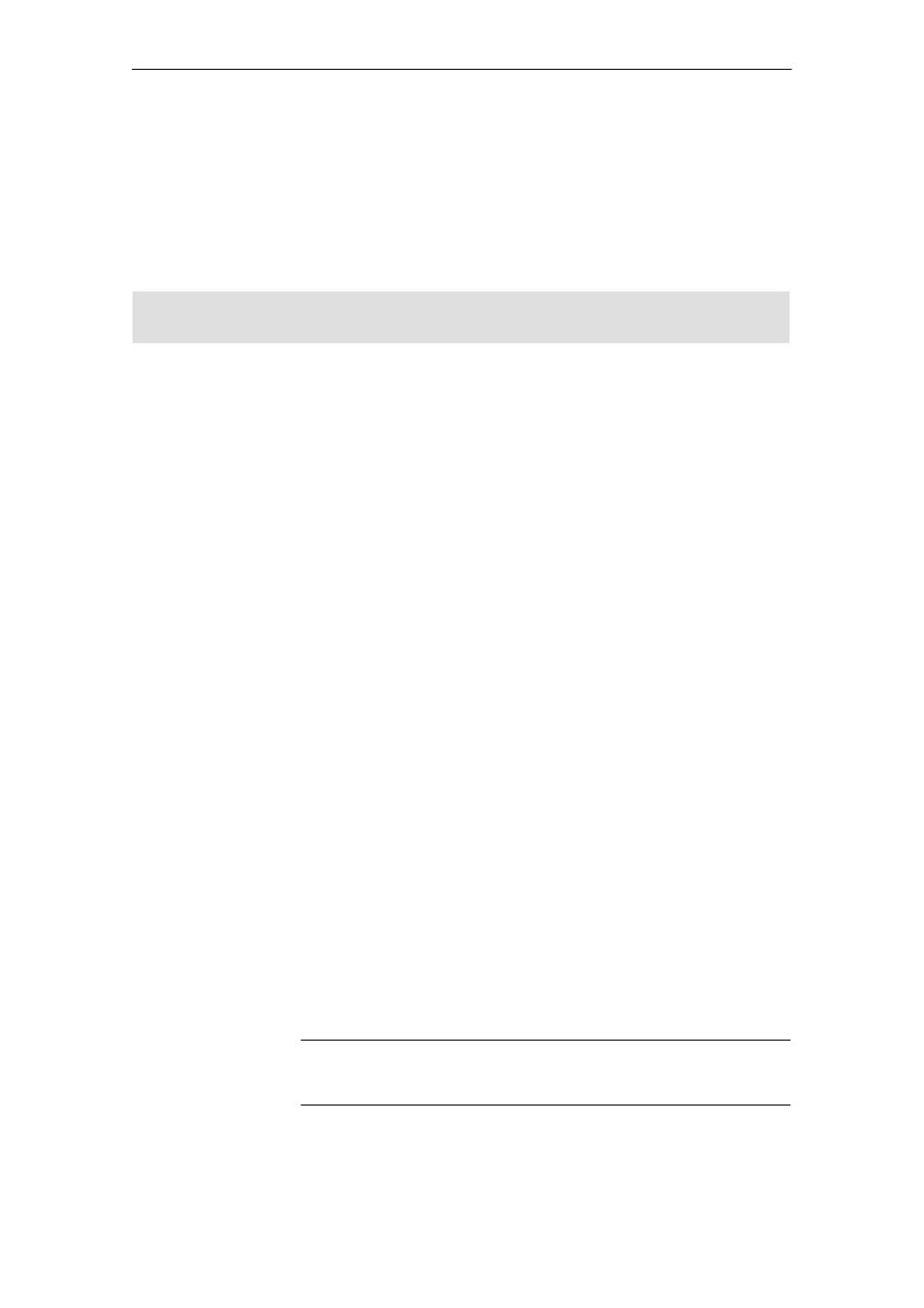
Design and Method of Operation
2-7
Positioner SIPART PS2/SIPART PS2 PA
C79000-G7476-C150–01
2.3
Method of operation
The electropneumatic positioner SIPART PS together with the pneuma-
tic actuator forms a control loop in which the actual value x is the posi-
tion of the actuator rod on linear actuators and the position of the ac-
tuator shaft on rotary actuators and the reference variable w is the
actuating current of a controller or manual control station of between
0/4 and 20 mA.
With devices with PROFIBUS PA, the command variable w is set digi-
tally via a bus system.
The stroke or rotational movement of the actuator is transferred to a
servopotentiometer via the necessary mounting accessories, the feed-
back shaft and reversible gear train without play and then sent to the
analog input of the microcontroller.
This corrects the angular error of the stroke pick–off, if necessary, com-
pares the potentiometer voltage as an actual value x with the setpoint x
fed in via terminals 3 and 7 and calculates the manipulated variable
increments
"
D
y. Depending on the size and the direction of the sy-
stem deviation (x–w) the piezoelectric pre–controlled air inlet and air
outlet valve is opened. The volume of the actuator integrates the cor-
recting increments up to actuating pressure y which moves the actua-
tor rod or the actuator shaft approximately proportionally. These cor-
recting increments continue to change the actuating pressure until the
system deviation is zero.
The pneumatic actuators are available as single–acting and double–ac-
ting versions. In the single–acting version only one volume is ventilated
or vented. The resulting pressure is exerted against a spring. In the
double–acting version two volumes act against each other. One volume
is ventilated as the other volume is vented. See block diagrams in Fig.
2-7 and 2-9.
The control algorithm is an adaptive predictive five–point controller.
The valves are actuated with a maintained contact for large system
deviations (high–speed zone). The valves are actuated with pulse–
width–modulated pulses for medium system deviations (short–step
zone).
No positioning pulses are output in the zone of low system deviation
(self-adjusting dead band). The dead-band adaptation and the continual
adaptation of the minimum pulse length in automatic operation allow
the best possible control accuracy to be achieved with the minimum
switching frequencies. The start parameters are determined during the
initialization phase.
Figs. 2-7 to 2-10 show the block diagrams for single and double-acting
actuators, in this example on a linear actuator.
☞
Note
When not under power, the air discharge valve is always open.