Master – Moniteur 50 Series SMART Positioners User Manual
Page 14
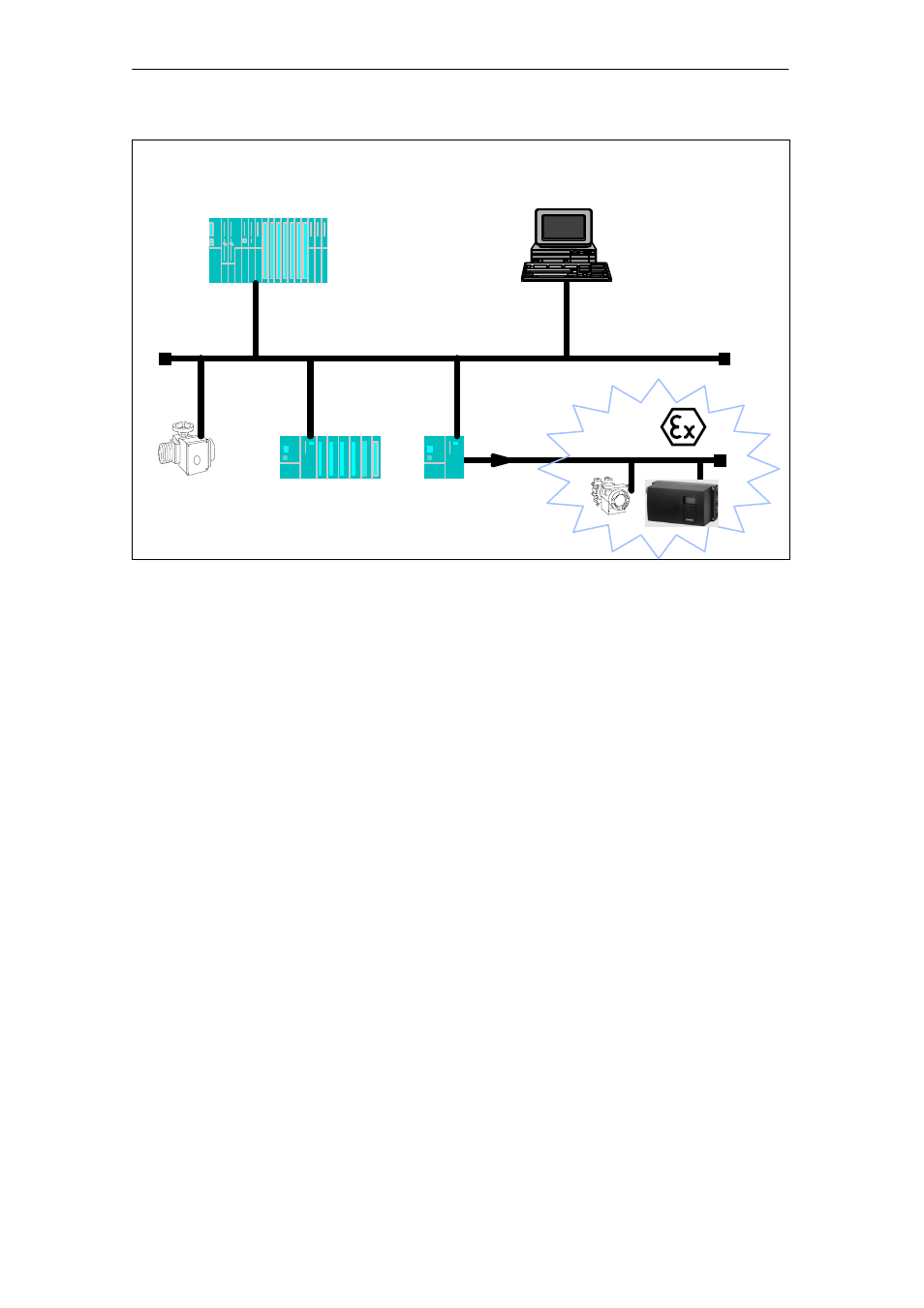
Introduction
1-4
Positioner SIPART PS2/SIPART PS2 PA
C79000-G7476-C150–01
Master
(class 2)
Master
(class 1)
PROFIBUS PA
Slaves
(field devices, distributed I/Os, lower–level controls,
gateway to PROFIBUS PA)
PROFIBUS DP
J
Fig. 1-1
Typical PROFIBUS automation system
Fig. 1-1 shows a section of a typical PROFIBUS automation system.
The control system consists of two masters with distributed tasks:
The master class 1 performs open–loop and closed–loop control tasks,
master class 2 is used for HMI functions. Exchange of measuring and
positioning data is performed cyclically between master 1 and the field
devices. Parallel with this data, the status information of the field de-
vices is transmitted and evaluated in master 1. Parameterization of the
field devices or reading of further device information is not performed in
cyclic operation.
The control system obtains the information required to establish com-
munication from the device–specific device master data files GSD (see
Appendix).
In addition to cyclic operation one or more masters of class 2 can ac-
cess the field devices non–cyclically. By this method of communication,
further information can be fetched from the devices or settings made in
the devices.
1.2.2 Properties of the PROFIBUS PA
The PROFIBUS PA permits bidirectional communication from a bus
master with the field devices via a shielded, twisted pair. At the same
time the two–wire field devices are powered via the same lines
(current J in Fig. 1-1).