Glossary of terms – Rockwell Automation 7000 PowerFlex Medium Voltage (B Frame) Commissioning - ForGe (PanelView 550) User Manual
Page 126
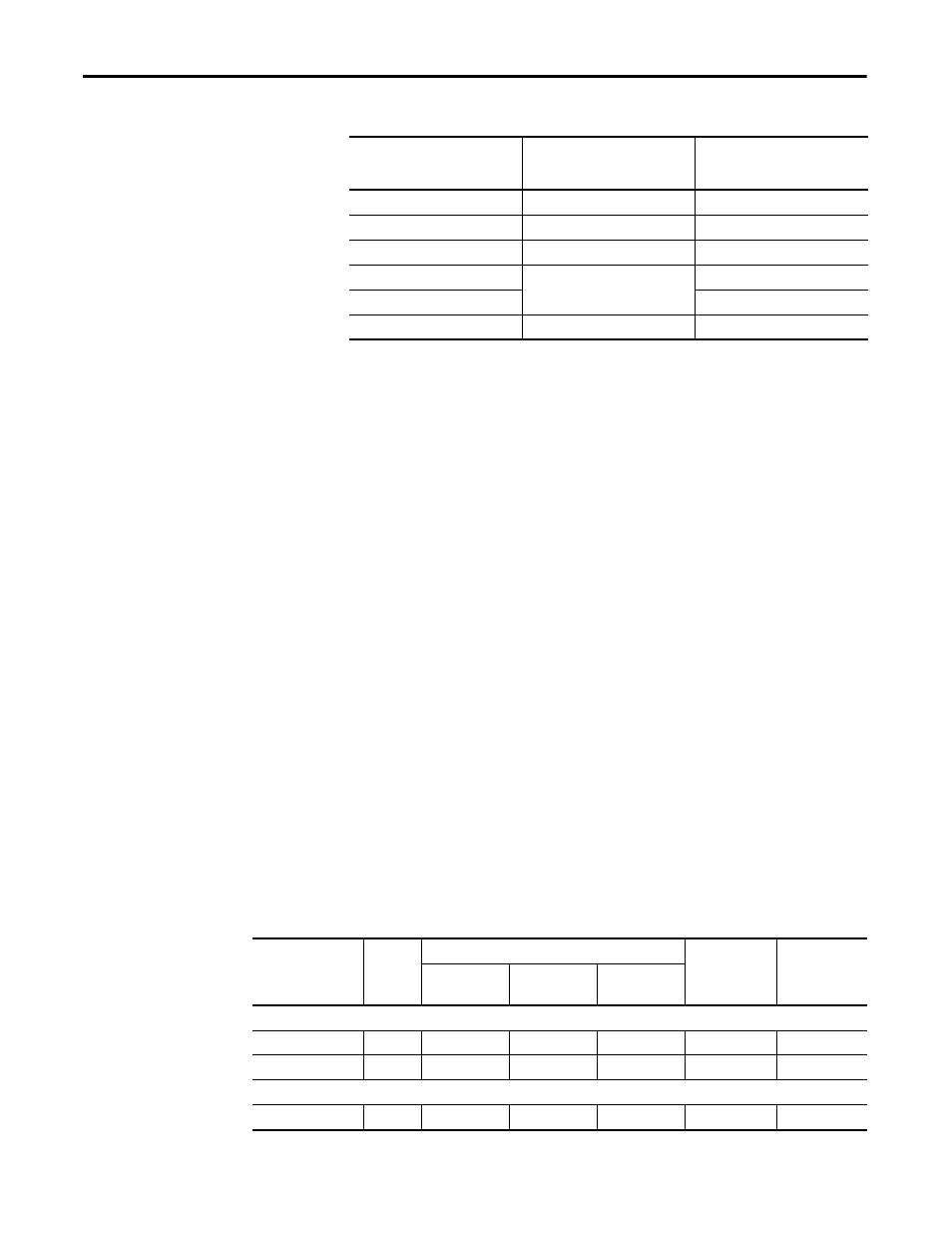
122
Rockwell Automation Publication 7000-IN006B-EN-P - May 2013
Appendix A
General Reference
Table 10 - PowerFlex 7000 Drive Torque Capabilities
** Drive will require over sizing to achieve greater than 100% continuous torque.
Glossary of Terms
Breakaway Torque: Torque required to start a machine from standstill.
Accelerating Torque: Torque required to accelerate a load to a given speed, in a
certain period of time. The following formula may be used to calculate the
average torque to accelerate a known inertia (WK
2):
T = (WK
2 x change in RPM) / 308t
where:
• T = acceleration torque in N.m (lb.-ft.)
• W = force N or kg f (lb)
• K = gyration radius m (ft)
• WK2 = total system inertia (kg f x m2 [lb-ft2
]
) that the motor must
accelerate, including motor, gear box, and load
• t = time (seconds) to accelerate total system load
Steady State Torque: Continuous operating torque required to control the load,
without instability.
Torque Limit: An electronic method of limiting the maximum torque available
from the motor. The software in a drive typically sets the torque limit to 150% of
motor rated torque.
Table 11 - Typical Application Load Torque Profiles
Parameter
7000 Torque Capability Without
Tachometer (% of Motor Rated
Torque)
7000 Torque Capability With
Tachometer
(% of Motor Rated Torque)
Breakaway Torque
90%
150%
Accelerating Torque
90% (0-8 Hertz)
140% (0-8 Hertz)
125% (9-75 Hertz)
140% (9-75 Hertz)
Steady State Torque
125% (9-75 Hertz) **
100% (1-2 Hertz)
140% (3-60 Hertz) **
Maximum Torque Limit
150%
150%
Application
Load
Torque
Profile
Load Torque as Percent of Full-Load Drive Torque
Required Drive
Service Duty
Rating
Tachometer
Required for
Extra Starting
Torque?
Break-away
Accelerating
Peak Running
AGITATORS
Liquid CT
100
100
100
Heavy
Yes
Slurry
CT
150
100
100
Heavy
Yes
BLOWERS (centrifugal)
Damper closed
VT
30
50
40
Normal
No