Model lsb, Removal of mech. seal, Installation of mech. seal – Xylem LSB User Manual
Page 97
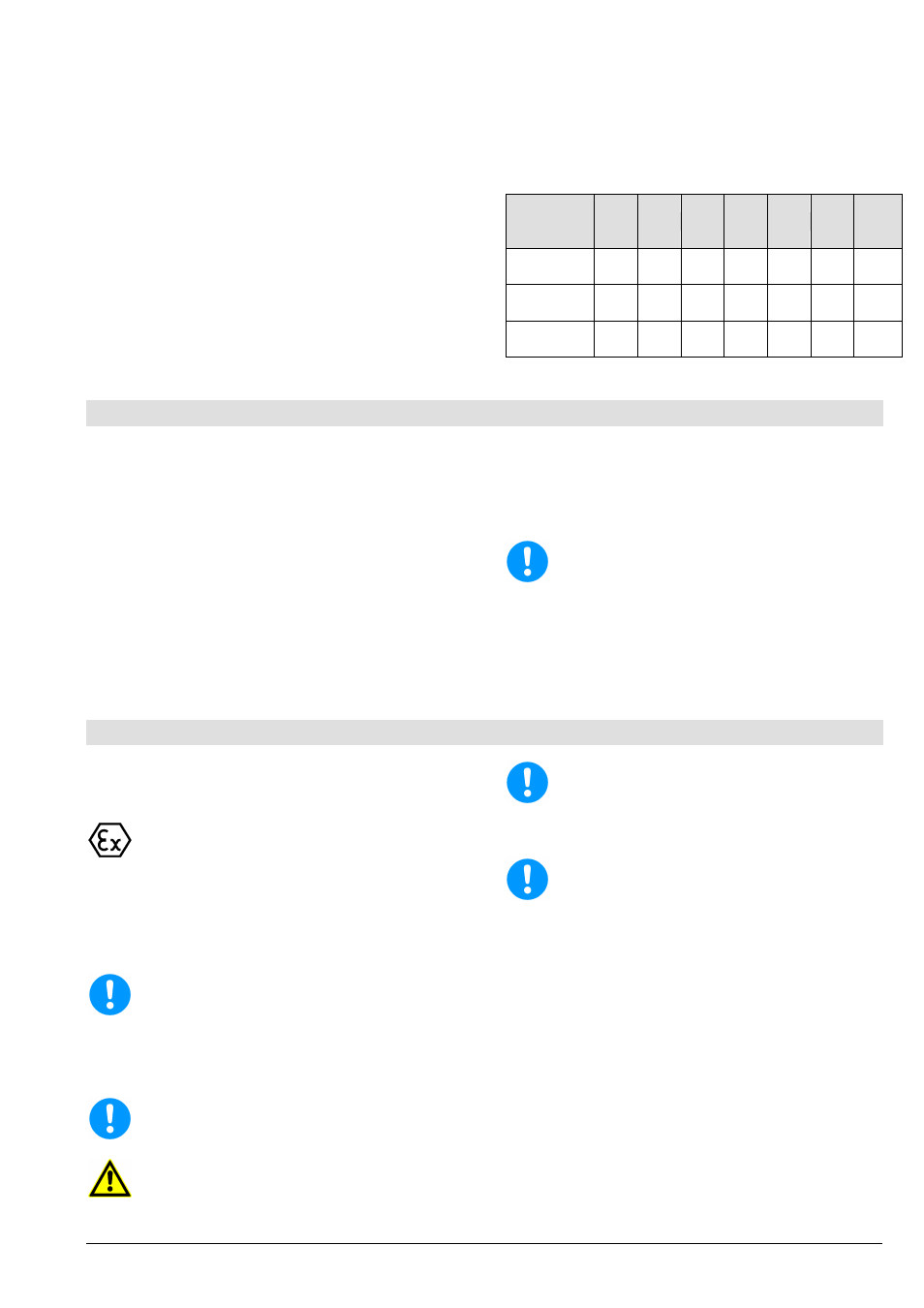
Installation, Operation and Maintenance Instruction
Model LSB
LSB 100-english
page 93
Revision 02
Artikel Nr. 771076129
Ausgabe 01/2010
Index of parts:
161
Casing cover
210
Shaft
230
Impeller
412.23
O-ring
412.32
O-ring
435
Mech. seal
471Q
Quench cover
502.31*)
Wear ring
527 a)
Fixing ring
542.31
Throttle bush
560 b)
Pin
904.31 a)
Grub screw
904.32*)
Grub screw
927
Impeller nut
*)
optional
a)
not for all designs
b)
only for mech. seals with PTFE-O-rings
Subject to techn. alterations!
Nominal
size of
mech. seal
∅
d
1
∅
d
7
l
1K
A
B
∅
d
L
QI, Q0
33
33
48 42,5 7,5
50
19 1/4-18
NPT
43
43
61
45
7,5 52,5 28 3/8-18
NPT
53
53
73 47,5 10 57,5 38 3/8-18
NPT
3. Removal of mech. seal
For that purpose use the appropriate sectional
drawing and the enclosed data sheet of the mech.
seal.
Remove and disassemble the pump acc. to the
Installation,
Operation
and
Maintenance
Instructions including chapter 8.6.
Remove fixing ring (527) (if existing) and rotating
part of the mech. seal (433) from shaft (210).
Refer to the enclosed data sheet of the mech.
seal, if set screws are to be loosened at the mech.
seal at first.
Remove casing cover (161) together with quench
cover (471Q). Use hexagonal screws (901.42) as
jack screws.
Pull stationary part of the mech. seal (433) and
throttle bush (542.31) out of quench cover (471Q).
Clean drilling for stationary seal ring (∅d
7
) in the
quench cover (471Q) and surface of the shaft
(210).
.
The reuse of mech. seals, which have already
been used for a longer time, can lead to leaking
at the seal faces after reinstallation. Therefore
the replacement of the mech. seal through a
new one is recommended. The dismounted
mechanical seal can be reconditioned by the
manufacturer and serve as a replacement
mech. seal.
4. Installation of mech. seal
For that purpose use the appropriate sectional
drawing and the enclosed data sheet of the mech.
seal.
It is only allowed to install mech. seals, which
have a certificate of Conformity acc. the
Directive 94/9/EG.
On changing the mech. seal type resp. the
mech. seal manufacturer the data regarding
max. operating temperature of the pumped
medium and temperature class must be
checked again.
Pay attention to the utmost cleanness!
Especially the seal faces must be clean, dry and
undamaged. Don´t apply lubrication on the seal
faces of the mech. seal.
If a lubricant is provided with the replacement
mech. seal, you should use this.
Use mineral grease or oil only, if you are
completely sure that the elastomers of the
mech. seal are oil resistant. Use no silicone.
Use only lubricants when you are sure that
there can´t occur any dangerous reactions
between the pumpage and the lubricant.
Make all required parts available, so that
assembly can be completed quickly. The
lubricants are only effective for a short time.
After that the axial movability and, thus, the
automatic adjustment of the elastomeres is lost.
Don´t push elastomers over sharp edges. If
necessary use mounting devices.
Put throttle bush (542.31) into quench cover
(471Q) carefully.
Press the stationary part of the mech. seal in the
quench cover (471Q). For this you can eventually
use a stamp with a soft surface. Unequal load can
lead to cracking of the seal face.
Don´t damage seal face!
Pay attention that the stationary ring is in solid
contact with the quench cover. The seal face must
be installed perpendicular to the shaft.
If a pin (560) is existing, be careful that it fits into
the slot of the mech. sealing, without touching the
mech. seal.
Insert casing cover (161) carefully, until it fits
axially in the bearing frame lantern (344).
Push the rotating unit of the mech. seal on the
shaft (210).