Model lsb, 8 reconditioning, 9 mounting – Xylem LSB User Manual
Page 89
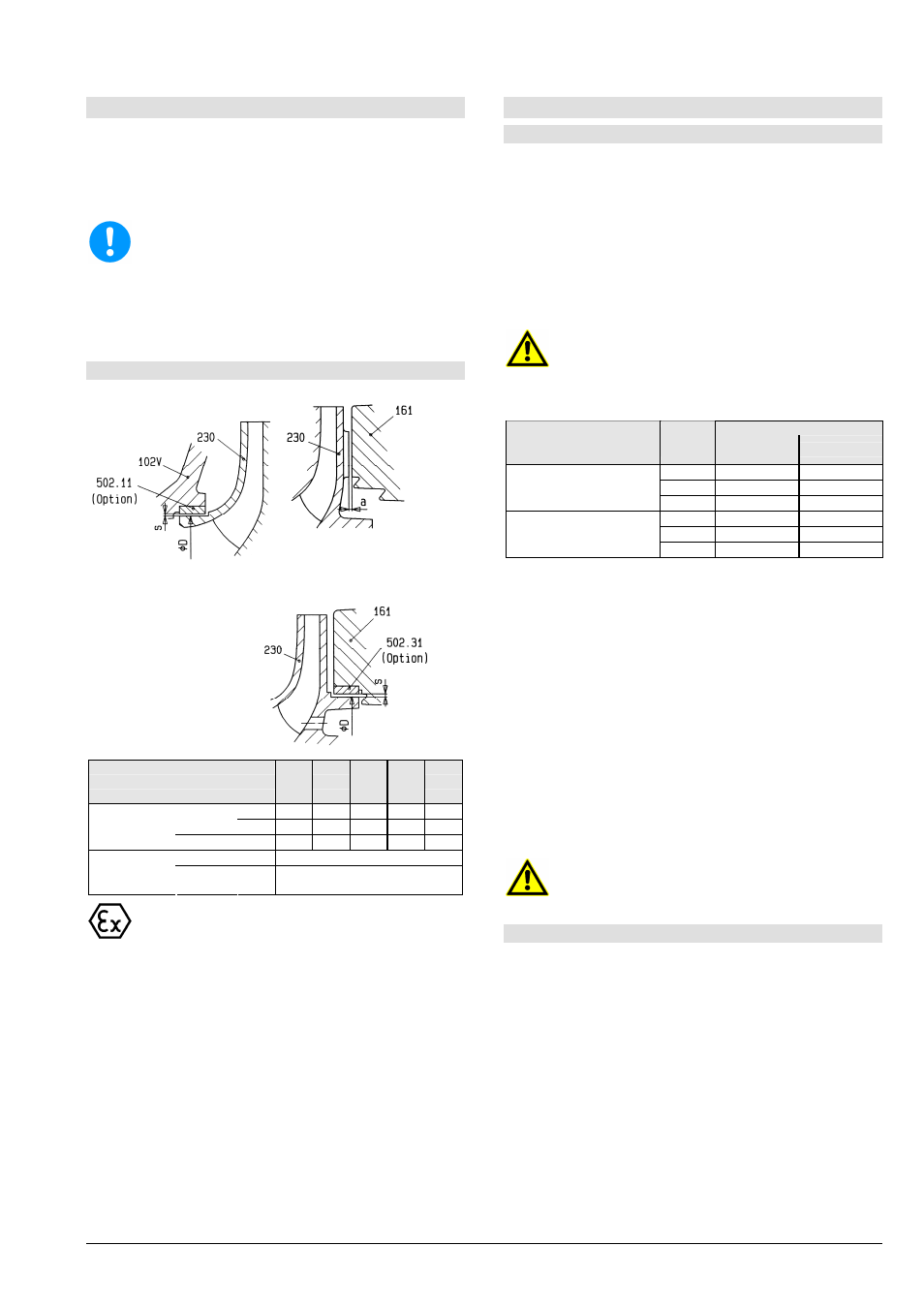
Installation, Operation and Maintenance Instruction
Model LSB
LSB 100-english
page 85
Revision 02
Artikel Nr. 771076129
Ausgabe 01/2010
8.8 Reconditioning
After disassembly all parts must be cleaned and
checked for wear carefully. Worn or damaged parts
must be replaced by new parts (spare parts).
It is recommended in most cases to replace mech.
seal, ball bearings and seals (flat seal, O-rings).
All PTFE-sealing elements and graphite
sealings are intended for being used only once.
In most cases it make sense, if damaged absolutely
necessary, to renew the mech. seal and the bearings
Deposits on the impeller (230), in the volute casing
(102V) or on the casing cover must be removed.
8.8.1 Clearance at impeller
Suction side of impeller
Back vanes of impeller
Drive side of impeller
Only with pump size
100-65-315
125-80-315
125-100-315
150-125-315
Nominal diameter D (mm)
60
68
85
100
120
135
155
175 220
min. 0,15 0,17 0,20 0,22 0,25
new
max. 0,19 0,22 0,24 0,27 0,30
Radial
clearance
s (mm)
worn
0,78 0,85 0,90 1,05 1,15
new
0,8 - 1,2
Axial
clearance
a (mm)
worn
max. 1,7
When the wear limits has been reached or
exceeded, the worn parts must be replaced.
For volute casings (102V) with a wear ring (502.11)
and cover casings (161) with a wear ring (502.31)
there are the following possibilities to restore the
correct clearance:
a) Renew impeller (230) and wear ring. Then the
original measures are restored.
b) A customized wear ring (bored to fit) can be
supplied to avoid replacement of the impeller.
Please contact factory for details.
When volute casing (102V) or casing cover (161)
without wear ring must be repaired, a wear ring can be
installed to renew pump performance. Remachining of
the volute casing and / or casing cover is required.
Please contact the factory for details and assistance.
8.9 Mounting
8.9.1 General
Re-assemble the pumps using the reverse order of
steps as completed for pump disassembly. However
the following observations should be considered:
Pay attention to the utmost cleanliness when
reassembling the pump.
For tight tolerances e.g. between stub shaft (210)
and motor shaft or impeller (230) and shaft (210),
as well as thread, use suitable anti-galling
compound (e.g. Molykote / Never-Seeze), so that
the next mounting and dismounting will be easier.
Anti-galling compound must be compatible with
the pumpage.
Screws should be tightened, with the following
torque:
Screw torque in Nm
Location
Screw
Size
Lubricated
threads
Dry threads
M12
35
50
M16
105
150
Casing Screws
M20
210
305
M10
35
50
M12
60
90
All other scres
M16
150
220
Do not use excessive force.
For mounting of stub shaft refer to chapter 8.9.2.
For mounting of mech. seal refer to separate
"Mounting Instruction of Shaft Sealing" and
chapter 8.5.
For impellers with back vanes the axial clearance
between the back vanes and the casing cover
(161) should be checked after mounting the
impeller (230) and tightening the impeller nut (922)
(see chapter 8.8.1).
After the mounting of the back pull out assembly,
and its assembly into the volute casing, turn the
shaft and control the free moving of the pump in
this way. The shaft sealings will cause slightly
resistance when turning, but there must not be
any contact between metal parts.
Before starting the pump do not forget to install
and connect all security devices.
8.9.2 Mounting of Stub Shaft
Insert key in the motor stump.
Put anti-galling compound onto the motor stump
(see point 8.9.1).
Push stub shaft up the motor shaft to measure A
(see pict. 11 and chart).
Drill countersink into motorshaft, appr. 2-3 mm
depth, through the radial bore in the motor shaft
(see pict. 11), by useing a twistdrill with 90° tip.
Remove cuttings out of the stud hole (e.g. with
compressed-air), screw in and make safe thread
pins (904.41 and 904.42) (e.g. with Omnifit 100 M
or Loctite).
Check smooth running of stub shaft opposite to
motor flange with a dial gauge. The pointer
deflection of the dial gauge must not exceed 0,1
mm.