Toshiba Tosvert VF-A5 User Manual
Page 18
Attention! The text in this document has been recognized automatically. To view the original document, you can use the "Original mode".
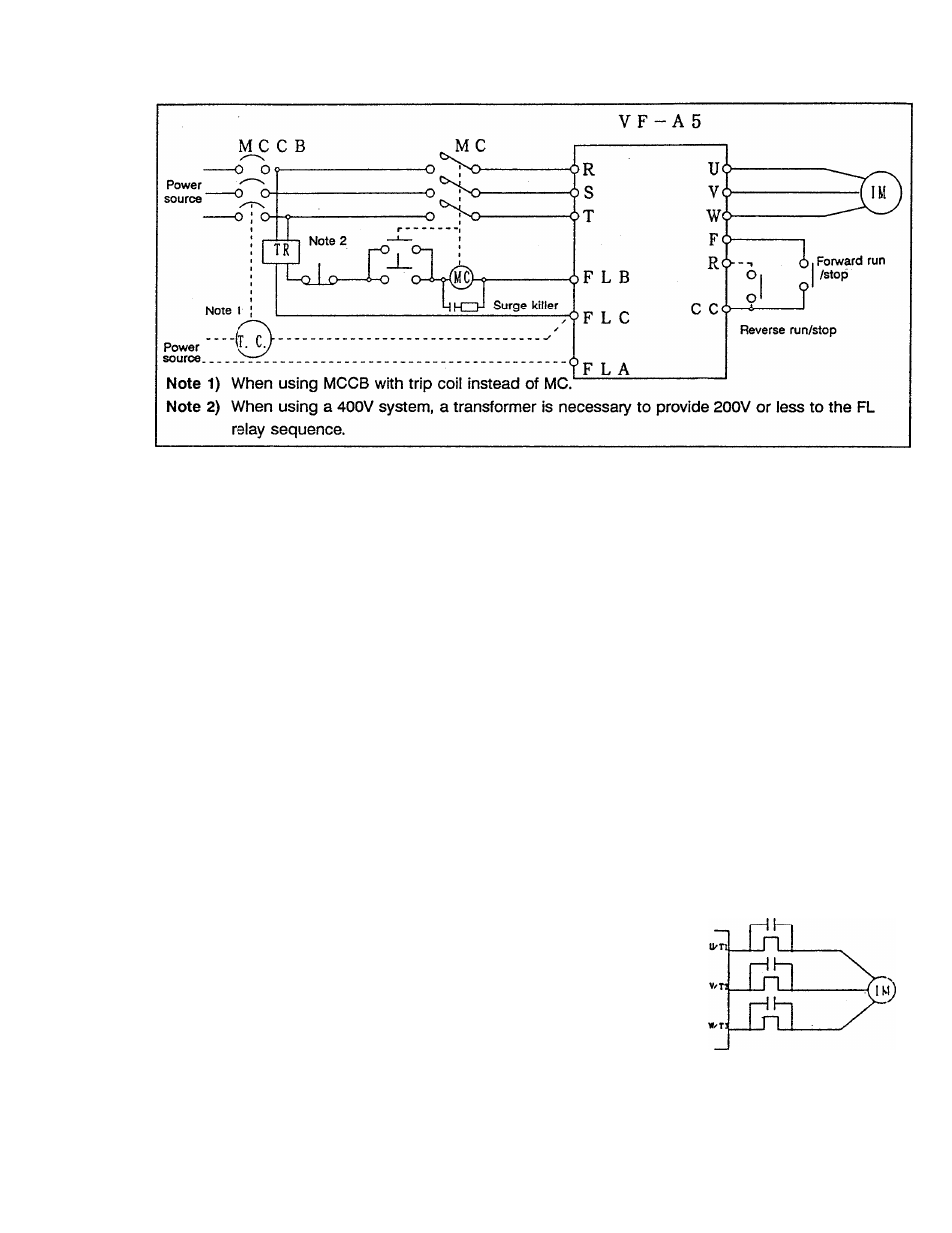
Fig. 5.2 Wiring example using a magnetic contactor
installation restrictions of secondary-side magnetic contactors
(1) As a rule, if a magnetic contactor is installed between the inverter and motor, do not turn it ON/OFF
while running. (If the secondary-side contactor is turned ON and OFF while running, a large current
may flow in the inverter, causing inverter damage and failure.)
(2) A magnetic contactor may be installed to change the motor or to change to the commercial power
source when the inverter is stopped. Always use an interlock with the magnetic contactor in this
situation so that the commercial power supply is not applied to the inverter’s output terminals.
Installation of overload relay (thermal relay)
(Refer to page 14; Examples of selecting equipment for wiring.)
(1) The VF-A5 has a built-in overload protection function that uses an electronic thermal relay. However,
in the following cases, the thermal relay operation level must be adjusted or an overload relay matching
the motor’s characteristics must be installed between the inverter and motor.
0When using a motor having a rated current value different from a Toshiba general-purpose motor.
(Adjust the electronic thermal level)
©When running a single motor with an output less than the specified standard applicable motor, or
when running several motor simultaneously (An overload relay must be installed on each motor.)
Note) If the motor cables for a 400V class inverter are long, the thermal
relay may malfunction. In this case, lower the carrier frequency (refer
to adjustment parameters on page 66), or install a 0.1/r to O.SpF-
1000V film capacitor between the input/output terminals of each
phase’s thermal relay.
< Example > When using external thermal relays, the inverter can be externally fault-tripped and
immediately stopped by using the following method (Fig. 5.3).
12