1 communication medium, 1 ems master to bms/bms ii/acs slave, 3 ems master to c-more boiler controller slaves – AERCO Modbus Communications Manual User Manual
Page 9: 2 address support, 3 modbus transmission modes, 4 timing specifications, Modbus, Communication, Gf-114
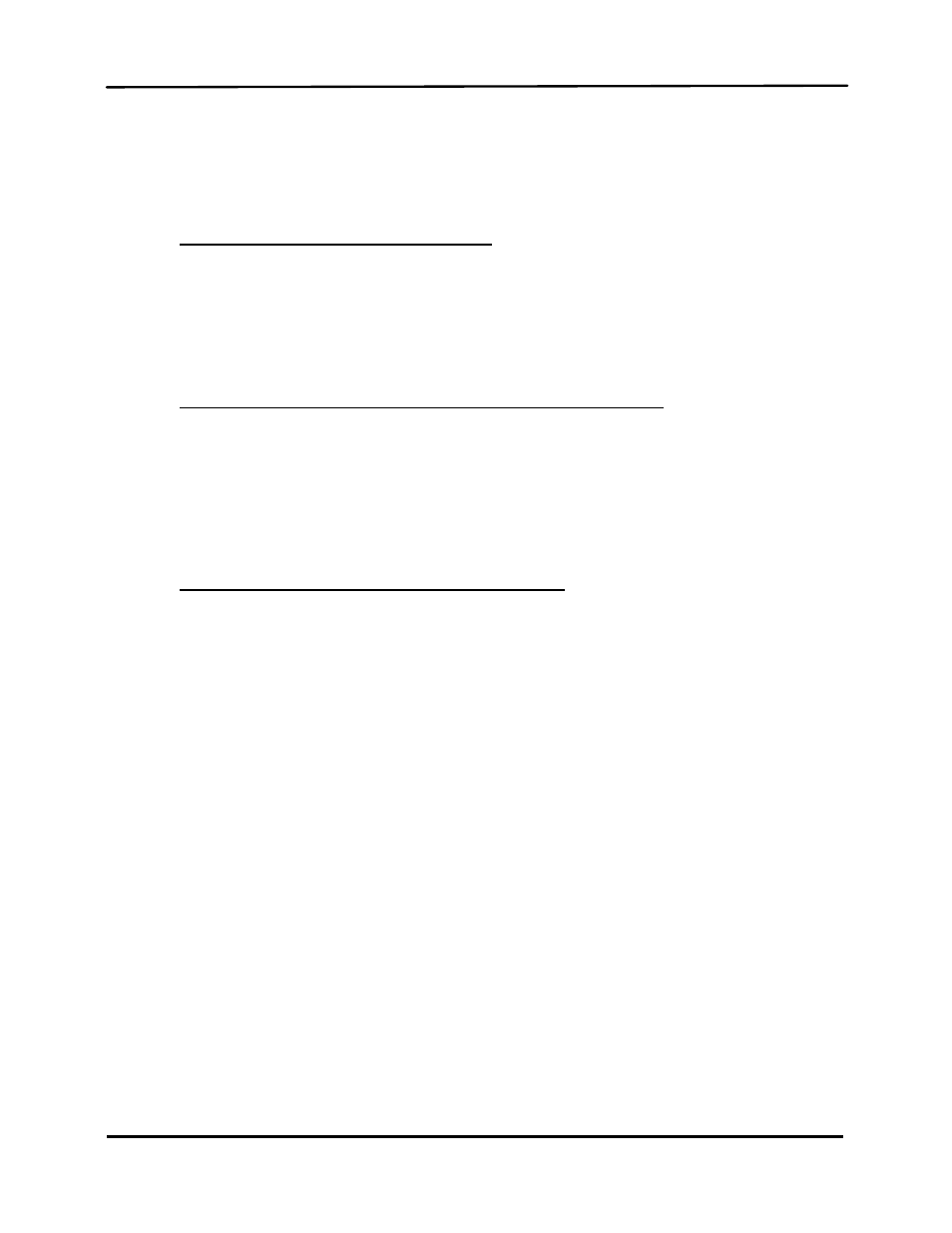
Chapter 1
MODBUS
Communication
GF-114
Introduction & Description
USER MANUAL
OMM-0035_0C
05/18/12 AERCO International, Inc. • 100 Oritani Dr. • Blauvelt, NY 10913 • Ph: 800-526-0288
Page
9 of 200
1.3.1 Communication Medium
The communication medium for each of the possible Modbus network configurations may vary
depending on the Master/Slave scenario being implemented. Detailed installation procedures
and wiring diagrams for the configurations described in the following paragraphs are provided in
Section 4 of this manual.
1.3.1.1 EMS Master To BMS/BMS II/ACS Slave
The Modbus network connections between the EMS and BMS/BMS II/ACS will depend on the
type of port provide on the EMS Master. If the EMS contains a RS232 port, a direct connection
can be made directly to the BMS/BMS II/ACS RS232 port. For optimum results the wire length
between the EMS and BMS/BMS II/ACS RS232 connection should not exceed 50 feet. If the
EMS Master contains a RS485 port, a RS485-to-RS232 converter will be required to implement
the Modbus network.
1.3.1.2 BMS/BMS II/ACS Master To C-More Boiler Controller Slaves
Up to a total of 32 C-More Boiler Controllers can be connected to a BMS/BMS II/ACS Master on
the Modbus Network. Multi-point drop network connections are made using shielded, twisted-
pair wire. In addition to the Modbus Network Boilers, up to 8 additional Legacy Boilers can be
connected to the BMS Pulse Width Modulation (PWM) wiring connection. The BMS II and ACS
do not support PWM. It should be noted that the BMS, BMS II, and ACS include a Modbus
Pass-Thru feature which, when enabled, permits an EMS to monitor and configure (but not
directly control) the boilers.
1.3.1.3 EMS Master To C-More Boiler Controller Slaves
The number of C-More Boiler Controllers which can be connected to a Modbus Network which
utilizes a third party EMS Master will depend on the EMS’s limitations. Theoretically, the
maximum number of Slave devices is limited to 127. If the EMS contains a RS232 port, a
RS232-to-RS485 converter will be required to provide the necessary RS485 interfaces and
signal levels for the C-More Boiler Controllers. Multi-drop network connections are made using
shielded, twisted-pair wire.
1.3.2 Address Support
Address support is assigned as follows:
•
BMS/BMS II/ACS Address Support From EMS Master: 128 – 247 (80 – F7 hex)
•
C-More Address Support From BMS/BMS II/ACS or EMS Master: 1 – 127 (01 – 7F hex)
•
Broadcast Messages: Address 0 is reserved for all Broadcast messages
1.3.3 Modbus Transmission Modes
Many Modbus Controllers can be set up to transmit using either the ASCII (American Standard
Code for Information Interchange) transmission mode, or the RTU (Remote Terminal Unit)
transmission mode. However, since RTU messages can be formatted using far fewer binary
bits than the corresponding ASCII message, it is far more efficient. Therefore, all Modbus
messages for the AERCO BMS/BMS II/ACS and C-More Boiler Controllers use RTU
transmission ONLY. If a third-party EMS Master is being used in the Modbus network, ensure
that it is set for RTU transmission.
1.3.4 Timing Specifications
As Table 1-1 shows, Baud Rate and Heartbeat Timeout will vary depending on the
Configurations of the AERCO BMS/BMS II/ACS and C-More Boiler Controllers being used in the
Modbus Network. Ensure that the Baud Rate used by the controlling Master (BMS/BMS II/ACS