2 modbus direct drive control and monitoring, 3 modbus remote setpoint control, Modbus – AERCO Modbus Communications Manual User Manual
Page 82: Communication, Gf-114
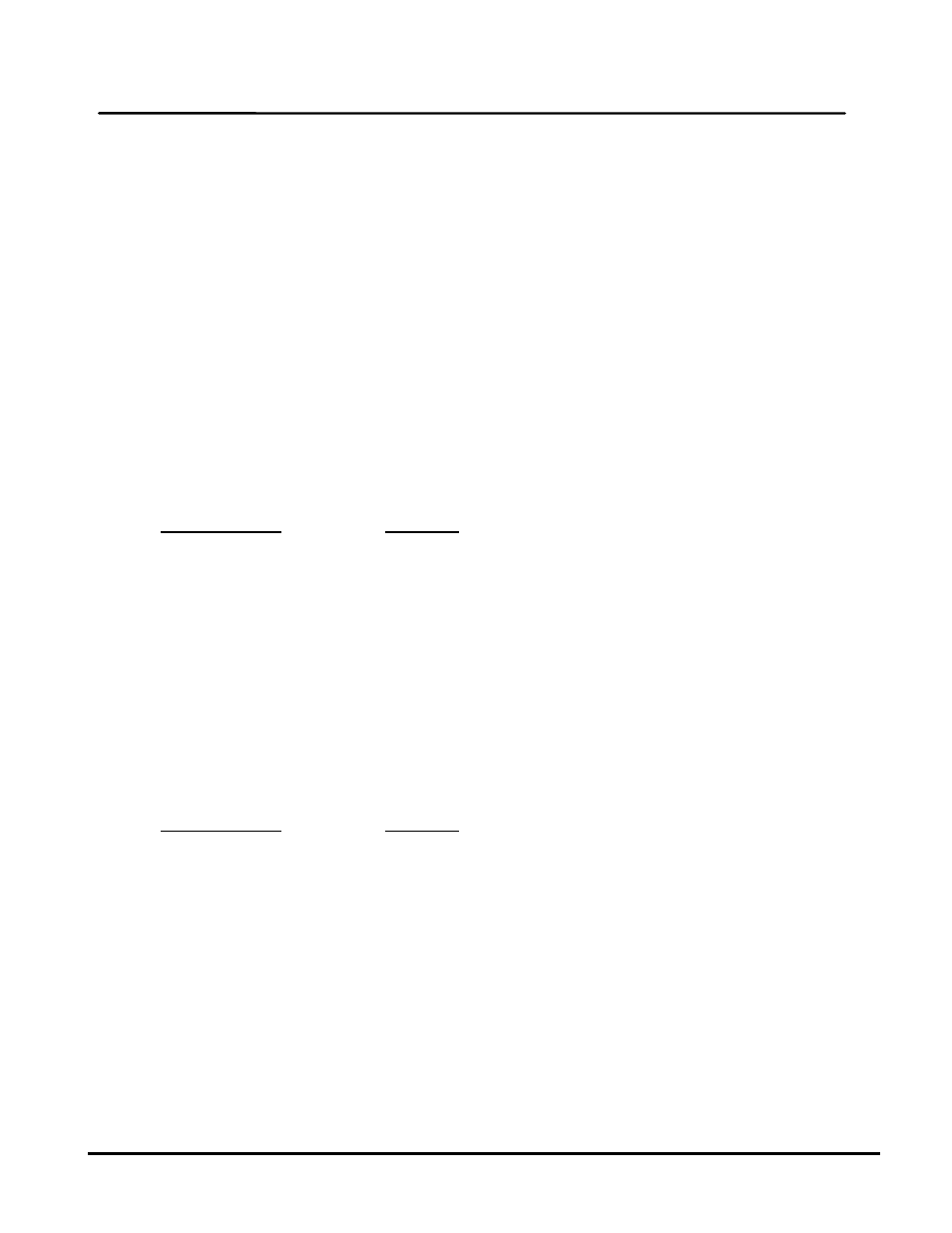
GF-114
MODBUS
Communication
Chapter 6
OMM-0035_0C
USER MANUAL C-More/BMS II/ACS Software Setup
Page
82 of 200 AERCO International, Inc. • 100 Oritani Dr. • Blauvelt, NY 10913 • Ph.: 800-526-0288 05/18/12
NOTE
A C-More Boiler Controller can be monitored or configured on the
Modbus Network regardless of its mode of control.
1. Scroll through the Setup Menu until Comm Address is displayed.
2. With Comm Address displayed, press the
CHANGE key.
3. Using the ▲ or ▼ arrow key, enter the appropriate Comm Address from 1 to 127.
4. Press the
ENTER key to store the Comm Address in memory.
Once the Comm Address has been entered, the C-More Boiler Controller can be accessed by
the Modbus Network Master (BMS II/ACS or EMS).
6.2.2 Modbus Direct Drive Control and Monitoring
Modbus Direct Drive Control of the C-More Boiler Controller is set up as follows:
1. Enter and store a valid Comm Address using the procedures in paragraph 6.2.1.
2. Scroll through the Configuration Menu and change the following menu options to the
settings shown:
3.
MENU OPTION
SETTING
Boiler Mode Direct Drive
Remote Signal
Network
4. The C-More Controller is now set for Direct Drive operation via the Modbus Network.
5. AERCO recommends that the Setpoint Limiting feature in the Configuration Menu be
enabled. Also, ensure that the Failsafe Mode setting is set to the desired setting
(Shutdown or Constant Setpoint) in the event that the Modbus Network signal is lost.
6.2.3 Modbus Remote Setpoint Control
Modbus Remote Setpoint Control of the C-More Boiler Controller is set up as follows:
1. Enter and store a valid Comm Address using the procedures in paragraph 6.2.1.
2. Scroll through the Configuration Menu and change the following menu options to the
settings shown:
3.
MENU OPTION
SETTING
Boiler Mode Remote Setpoint
Remote Signal
Network
4. The C-More Controller is now set for Remote Setpoint operation via the Modbus Network.
5. AERCO recommends that the Setpoint Limiting feature in the Configuration Menu be
enabled. Also, ensure that the Failsafe Mode setting is set to the desired setting
(Shutdown or Constant Setpoint) in the event that the Modbus Network signal is lost.
NOTE
The AERCO BMS II/ACS can function as either a Slave or a
Master on a Modbus Network. Paragraph 6.3 provides the
programming setup procedures when the BMS II/ACS is a Slave to
an EMS (or BAS). Paragraph 6.4 provides the programming setup
procedures when the BMS II/ACS is the controlling Master for C-
More Boiler Controllers.