Modbus, Communication, Gf-114 – AERCO Modbus Communications Manual User Manual
Page 56
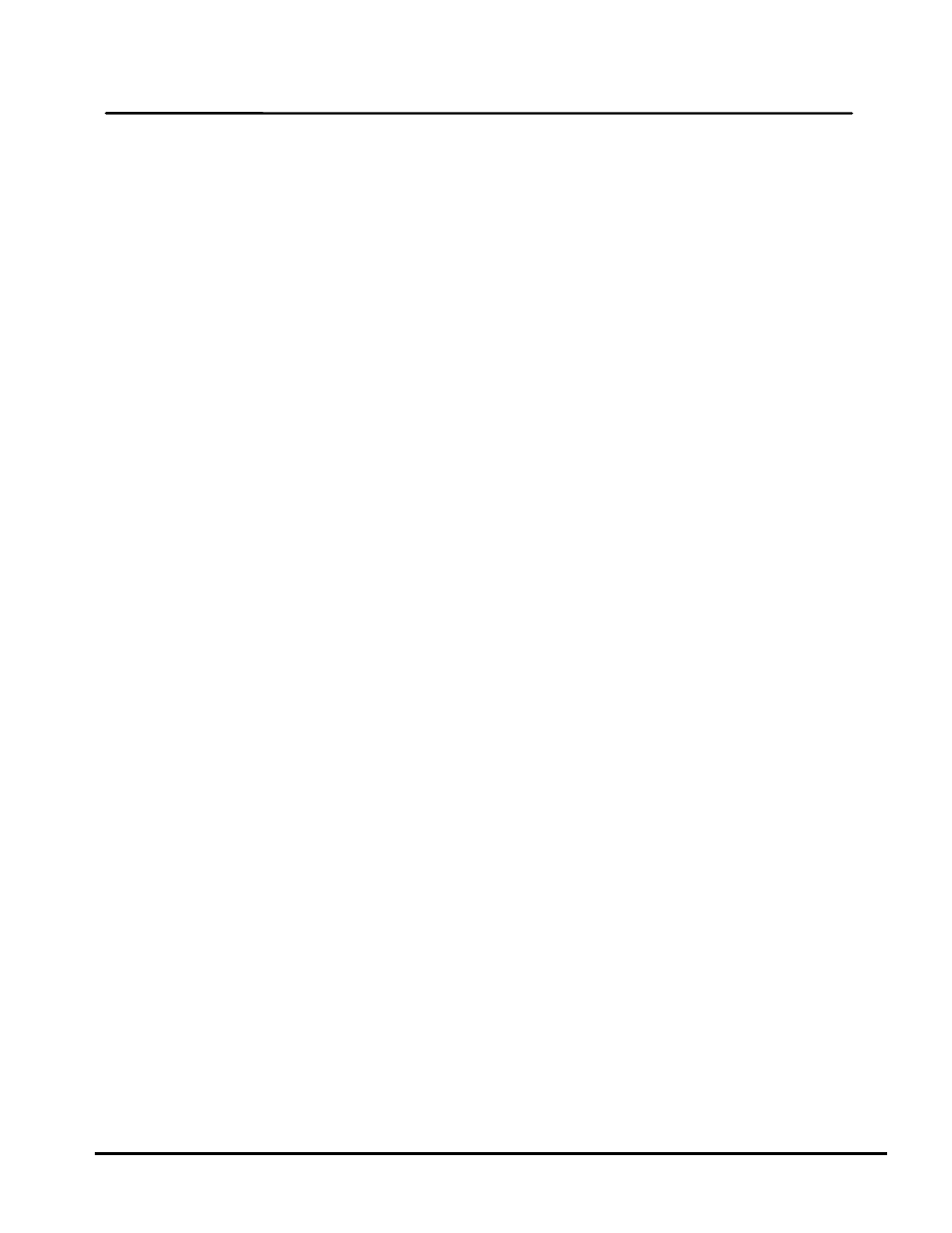
GF-114
MODBUS
Communication
Chapter 3
OMM-0035_0C
USER MANUAL
Standard Application Operations
Page
56 of 200 AERCO International, Inc. • 100 Oritani Dr. • Blauvelt, NY 10913 • Ph.: 800-526-0288 05/18/12
Holding Register addresses 0x0056 and 0x0057 respectively. Also, ensure that the RS232
Baud Rate setting (address 0x0058) matches the EMS Baud Rate being used.
In the Remote Setpoint Mode, the holding register parameter “Net Header Set Temp” (Holding
Register address 0x0004) must be transmitted periodically from the EMS Master to the BMS/
BMS II/ACS Slave. A “Heartbeat” Timer with a timeout period defined by the variable “Network
Timeout” (Holding Register address 0x007D), is reset each time the signal is successfully
received. If the timeout period is exceeded, the BMS/BMS II/ACS will default to its “Fail-Safe”
mode and display a Network Comm Fault.
3.3.3 BMS/BMS II/ACS Master Control of C-More Slaves Via Network
The BMS/BMS II/ACS can also communicate with the up to 32 Network C-MORE Boiler Control
Slaves via the BMS RS485 port. Parallel and Sequential control can be selected as before.
See BMS Manual GF-108M, BMS II Manual GF-124, or ACS Manual GF-131 for additional
information.
The “Number Of Network Boilers” must be entered at location 0x0059 in the Standard Holding
Registers.
The C-More Slave communication addresses (“Net Boiler 1 Address” To “Net Boiler
32 Address”) can either be manually entered in a pre-defined order in the BMS, or they can be
detected from the network and operated in the order they are detected. To manually enter
Network Boiler communication addresses, leave the “Min Slave Address” and “Max Slave
Address” set to their default values of 0. To allow the BMS to automatically detect the Network
Boilers, enter the respective “Min Slave Address” and “Max Slave Address” in their proper
location in the Standard Holding Registers (0x005A, 0X005B). The Max Slave Address must be
no more than 31 above the Min Slave Address.
The fire rate information will be transmitted periodically from the BMS/BMS II/ACS to the C-
MORE boiler controls. A “heartbeat” timer will be reset in the slave each time the control
information is successfully received from the BMS. If a timeout occurs, the slave will default to
its “Fail-Safe Mode” and display “Modbus Comm Fault”.
3.3.4 BMS Combination Mode Boiler Control of C-More Slaves (BMS and ACS
Only)
For BMS applications, the Legacy (PWM) Boilers 5 through 8 can be selected as Combination
Boilers. These Boilers are connected to the BLR 5 - BLR 8 PWM terminal connections (J2).
An AERCO Combination Control Panel (CCP) is necessary to configure this type of setup. It
should be noted that the assigned PWM Combination Boilers can be monitored and configured
on the Modbus Network by assigning a Comm Address between 1 and 127. Refer to BMS
Manual GF-108M for additional information on installation and setup.
NOTE
The C-More Demand Delay function can only be used on C-More
Controllers with software version 2.01 or higher.
For ACS applications, the domestic boilers (up to 8 of 32 network boilers) can be selected as
Combination Boilers. These boilers are connected to the RS485 terminal, JP6. Depending on
the application, ACS Relay Panel may be required. See Application Guide TAG-0049 and ACS
Manual GF-131.