4 combination control (bms/acs only), 5 physical slave address zero, 3 bms/bms ii/acs standard application operations – AERCO Modbus Communications Manual User Manual
Page 55: Modbus, Communication, Gf-114
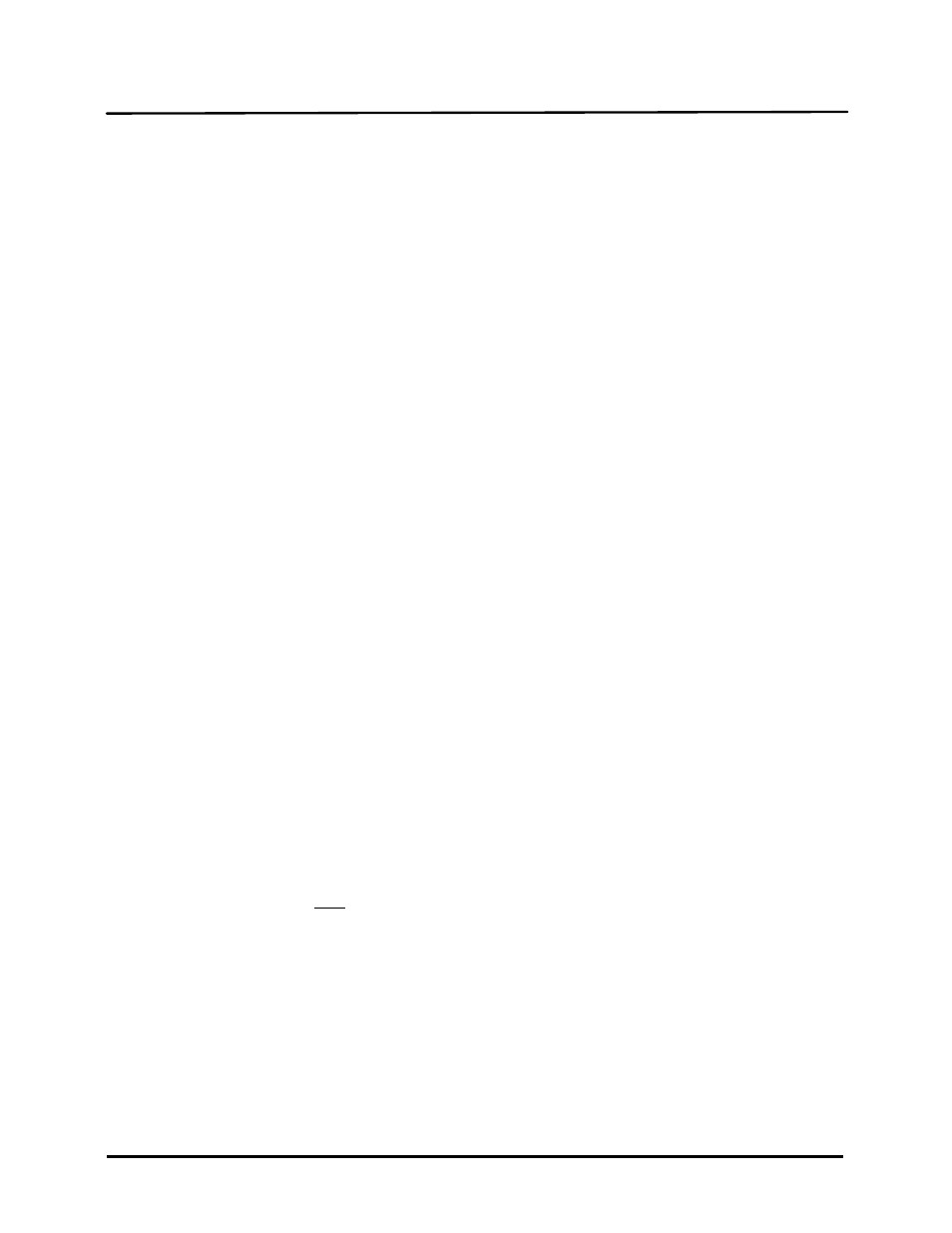
Chapter 3
MODBUS
Communication
GF-114
Standard Application Operations
USER MANUAL
OMM-0035_0C
05/18/12 AERCO International, Inc. • 100 Oritani Dr. • Blauvelt, NY 10913 • Ph: 800-526-0288
Page
55 of 200
3.2.4 Combination Control (BMS/ACS Only)
The Combination Control Mode is only used for the BMS and ACS,
NOT the BMS II. For BMS
applications, Combination Control is implemented via PWM input. For ACS applications
Combination Control is implanted via Modbus Network.
3.2.5 Physical Slave Address Zero
Normally, each Modbus Network Slave Controller will be assigned its own unique Comm.
Address (Input Register Address 0x0013). Valid entries are from 1 to 127. However, if the
default address of 0 is assigned, the C-More Slave, will not respond or process any Modbus
Network messages. This effectively disables the Slave’s Modbus communication link.
3.3 BMS/BMS II/ACS STANDARD APPLICATION OPERATIONS
For an AERCO BMS (only) Controller, the first eight Boilers are reserved for Legacy Boilers.
These Legacy Boilers are wired to the J2 connector terminals and are controlled utilizing Pulse
Width Modulation (PWM) signals, just as with earlier BMS Models, prior to implementation of
Modbus. Therefore, Boiler No. 9 will be the first Modbus Network Boiler, Boiler No. 10 will be
the second and so on. Up to 32 Network Boilers can be connected on a Modbus Network, in
addition to the 8 Legacy Boilers. The BMS will operate the Network Boilers and the Legacy
Boilers as one complete System.
The BMS II and ACS do not utilize PWM signals and will not operate a Legacy Boiler Controller
that does not have Modbus capability. The BMS II and ACS will operate up to 32 Network
Boilers.
3.3.1 Password Protection for BMS/BMS II/ACS Input and Holding Register
Access
Access to BMS/BMS II/ACS register addresses are protected by a password in virtually the
same manner as the C-More Controllers. For the BMS/BMS II/ACS, a communications security
code holding register “Password Lo” and “Password Hi” (addresses 0x007E, 0x007F) must be
written with the proper password for writing data in the BMS/BMS II/ACS through the RS232
communications port. If an attempt is made to write data to a single holding register using an
incorrect password, write access is denied. If this occurs, an Illegal Data Address Exception
Code (02) is generated and the data is not changed. Reading data is allowed, even if the
password is incorrect. If a Modbus message is received to read multiple Input or Holding
Registers and one or more of the addresses is not accessible, an Illegal Data Address
Exception Code will be sent to the EMS Master and no data is affected.
Only the network control variable “Net Header Set Temp” (address 0x0004) can be written
without a password and only if the BMS/BMS II/ACS is programmed for Remote Setpoint
Control by an EMS Master.
3.3.2 Remote Setpoint Control of BMS/BMS II/ACS Slave By EMS Master
All Modbus communication between a BMS/BMS II/ACS Slave and an EMS Master is
accomplished via the RS232 port. If the EMS Master also contains a RS232 port, it can be
directly connected to the BMS/BMS II/ACS. However, if the EMS Master contains only a RS485
port, a RS232-to-RS485 Converter is required.
To enable the Remote Setpoint Mode, the parameters “Remote Signal” and “RS232 Mode”
must be set to “Network” and “Modbus” respectively. These parameter are stored in Standard