4 c-more slaves to bms/bms ii/acs or ems master, 3 rs485 loop terminating resistors and bias, 1 bms terminating resistor – AERCO Modbus Communications Manual User Manual
Page 66: Modbus, Communication, Gf-114
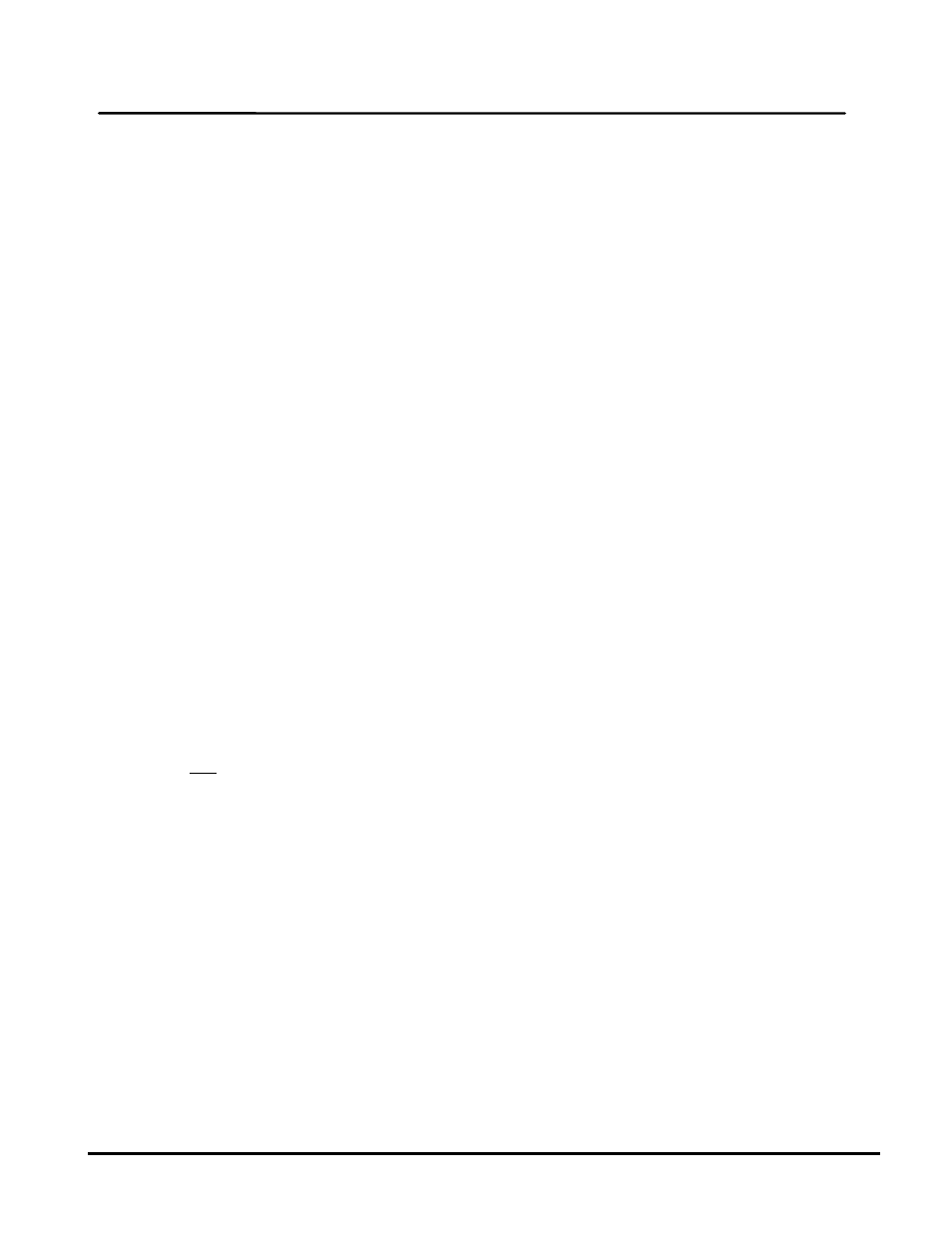
GF-114
MODBUS
Communication
Chapter 4
OMM-0035_0C
USER MANUAL
Hardware Setup & Installation
Page
66 of 200 AERCO International, Inc. • 100 Oritani Dr. • Blauvelt, NY 10913 • Ph.: 800-526-0288 05/18/12
4.2.4 C-More Slaves To BMS/BMS II/ACS or EMS Master
Wiring connections between a BMS/BMS II/ACS Master and up to 32 Network C-More Boiler
Controller Slaves are made directly between the BMS/BMS II/ACS internal RS485 terminals
(Figure 4-4 or 4-5) and the RS485 COMM terminals in each Boiler’s I/O Box (Figure 4-7).
If a third-party EMS Master is used in place of the BMS/BMS II/ACS, the Modbus Network
connections will depend on the available communication port(s) on the EMS. Many EMS Models
contain only a RS232 (DB9) port, while others contain either a 2-Wire or 4-Wire RS485 port.
Some EMS models contain both a RS232 and a RS485 port. If the EMS is equipped with only a
RS232 port, a RS232-to-RS485 converter will be required (such as a B&B Electronics, Model
485SD9TB).
4.3 RS485 LOOP TERMINATING RESISTORS AND BIAS
A terminating resistor (120 ohms) on each end of the RS485 loop is designed to match the
electrical impedance characteristic of the twisted-pair loop and prevent echoes or cross-talk from
corrupting data on the line.
Bias may be necessary on the RS485 loop to minimize noise on the circuit. Loop bias is
accomplished by activating pull-up/pull-down resistors on the last C-More Boiler Controller in the
chain. Do not activate the bias DIP switches on the BMS II/ACS when the C-More bias is used
AERCO requires that both terminating resistors and bias be implemented on the RS485 circuit
as described in paragraphs 4.3.1 and 4.3.2 which follow.
4.3.1 BMS Terminating Resistor
Each BMS/BMS II/ACS is equipped with a built-in terminating resistor (120 ohms) on the RS485
port. Therefore, only one additional terminating resistor will be required at the other end of the
RS485 loop. Ensure that the last C-More Boiler Controller Slave on the loop has its terminating
resistor activated as described in paragraph 4.3.2.
4.3.2 C-More Boiler Controller Terminating Resistor and Bias
C-More Boiler Controllers can function only as Slave devices on a Modbus Network. Since the
Slaves are connected in a “Daisy-Chain” configuration, the terminating resistor must be enabled
only in the last C-More Boiler Controller in the chain. In addition, bias must also be implemented
only in the last C-More Boiler Controller. This is accomplished by setting a DIP switches on the
Primary Micro-Controller (PMC) Board contained in the applicable C-More Boiler Controller. The
last unit in the chain must be energized (even if disabled) to enable bias. To activate the DIP
switches, proceed as follows:
1. Remove power from the last C-More Boiler Controller in the RS485 loop.
2. Loosen and remove the four (4) screws securing the front panel assembly to the chassis
as shown in Figure 4-8.
3. Carefully separate the panel from the chassis. Use care to avoid applying undue stress
to the ribbon cable connected between the back of the panel and the chassis-mounted
printed circuit boards.