Kinetix 5500 capacitor module status indicators, General troubleshooting – Rockwell Automation 2198-Hxxx Kinetix 5500 Servo Drives User Manual User Manual
Page 147
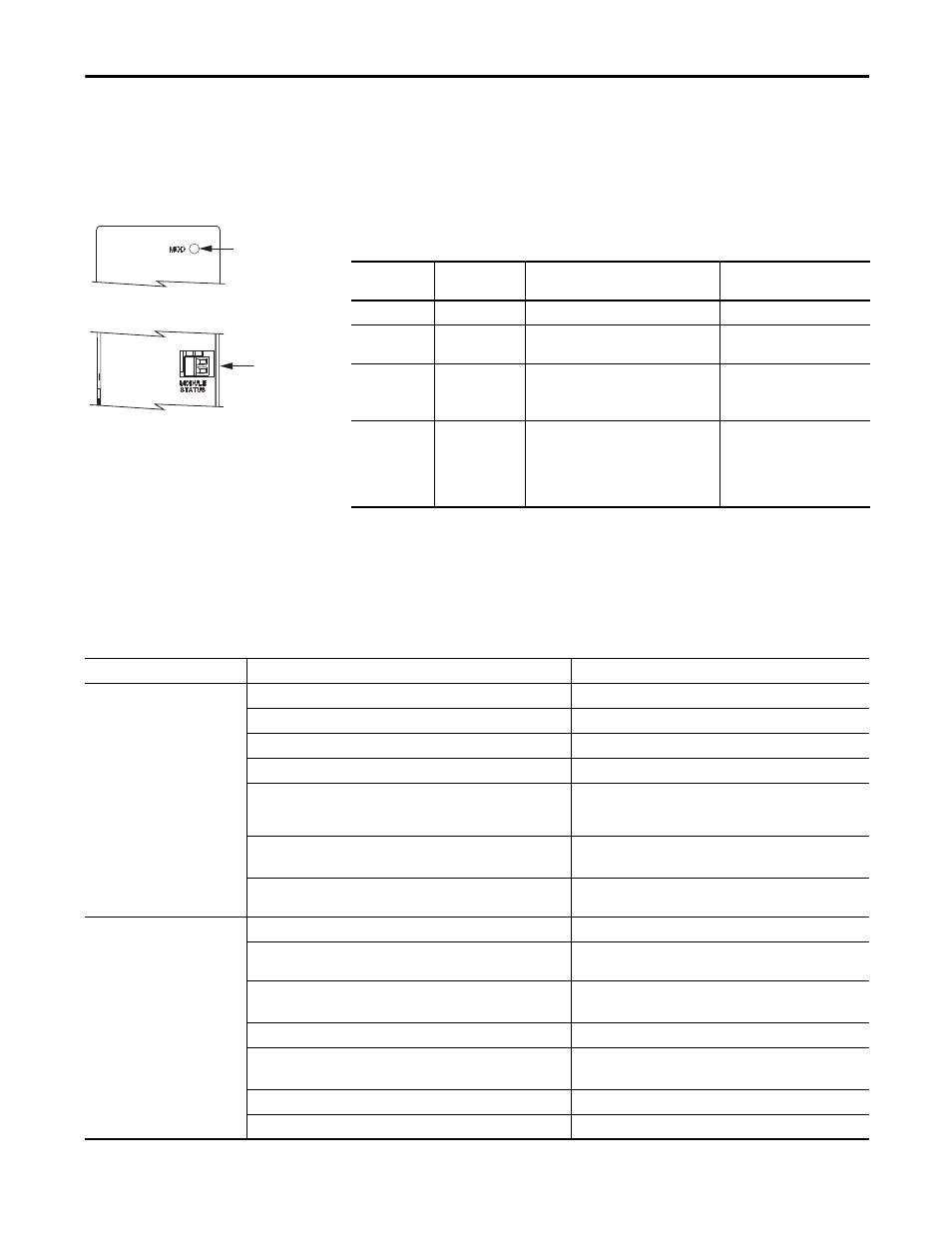
Rockwell Automation Publication 2198-UM001D-EN-P - May 2014
147
Troubleshooting the Kinetix 5500 Drive System
Chapter 7
Kinetix 5500 Capacitor Module Status Indicators
The capacitor module status indicator and module status (MS) connector are on
the front of the module. The module status connector is a relay output suitable
for wiring to the Logix5000 controller.
Table 66 - Module Status Indicator and Relay Output
General Troubleshooting
These conditions do not always result in a fault code, but can require
troubleshooting to improve performance.
Module Status
Indicator
Relay Output
(1)
(1) Wiring the module status relay output to the Logix5000 controller is optional.
Status
Resolution
Steady Green
Closed
Bus is fully charged and no faults exist.
N/A
Flashing Green
Open
Control power is present and bus is waiting
to charge up.
N/A
Flashing Red
Open
Recoverable fault
(precharge or overvoltage fault).
• Cycle control and bus power
• Verify that AC input meets
specificatons
Steady Red
Open
Internal, non-recoverable fault condition
inside the module.
• Cycle control and bus power
• Verify that AC input meets
specificatons
• Replace the module if fault
persists
Module Status
Indicator
Kinetix 5500 Capacitor Module
Module Status
(MS) Connector
Table 67 - General Troubleshooting
Condition
Potential Cause
Possible Resolution
Axis or system is unstable.
The position feedback device is incorrect or open.
Check wiring.
Unintentionally in Torque mode.
Check to see what primary operation mode was programmed.
Motor tuning limits are set too high.
Run Tune in the Logix Designer application.
Position loop gain or position controller accel/decel rate is improperly set.
Run Tune in the Logix Designer application.
Improper grounding or shielding techniques are causing noise to be
transmitted into the position feedback or velocity command lines,
causing erratic axis movement.
Check wiring and ground.
Motor Select limit is incorrectly set (servo motor is not matched to axis
module).
• Check setups.
• Run Tune in the Logix Designer application.
Mechanical resonance.
Notch filter or output filter can be required (refer to Axis Properties
dialog box, Output tab in the Logix Designer application).
You cannot obtain the motor
acceleration/deceleration that you
want.
Torque Limit limits are set too low.
Verify that torque limits are set properly.
Incorrect motor selected in configuration.
Select the correct motor and run Tune in the Logix Designer
application again.
The system inertia is excessive.
• Check motor size versus application need.
• Review servo system sizing.
The system friction torque is excessive.
Check motor size versus application need.
Available current is insufficient to supply the correct accel/decel rate.
• Check motor size versus application need.
• Review servo system sizing.
Acceleration limit is incorrect.
Verify limit settings and correct them, as necessary.
Velocity Limit limits are incorrect.
Verify limit settings and correct them, as necessary.