Rockwell Automation 2198-Hxxx Kinetix 5500 Servo Drives User Manual User Manual
Page 143
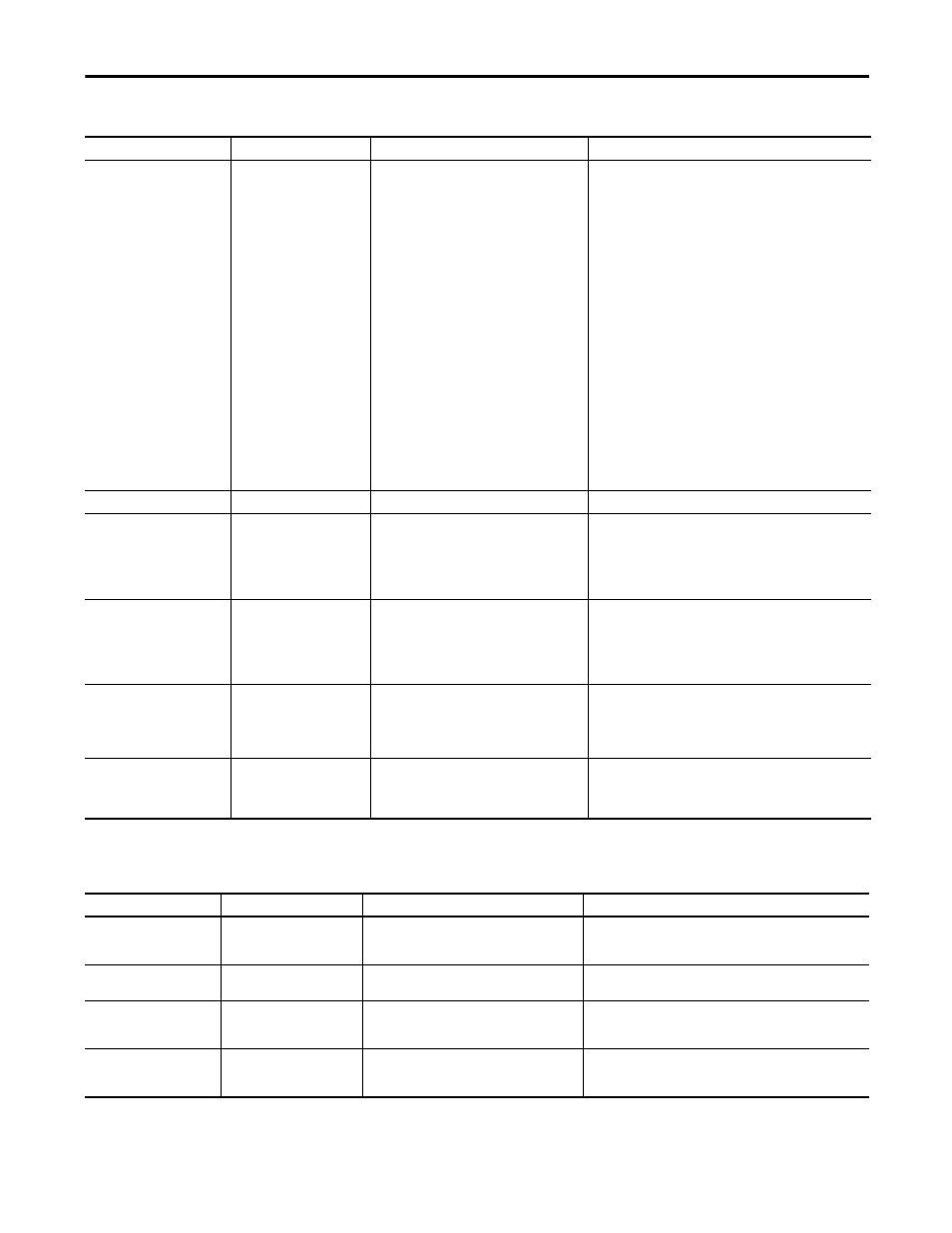
Rockwell Automation Publication 2198-UM001D-EN-P - May 2014
143
Troubleshooting the Kinetix 5500 Drive System
Chapter 7
FLT S47 – FDBK DEVICE FAILURE nn
Feedback Device Failure
The feedback device has detected an internal error.
The nn sub-code is defined as follows:
1:
ACCELERATION OVERFLOW
4:
TRACKING FILTER ERROR
5:
VECTOR LENGTH ERROR
6:
COUNTER ERROR
7:
SYNCHRONIZATION ERROR
16: SINGLE TURN ERROR
17: MULTI TURN AMPLITUDE ERROR
18: MULTI TURN SYNC ERROR
19: MULTI TURN VECTOR LENGTH ERROR
35: STANDARD PARAMETER ERROR
36: INTERNAL COMMUNICATION ERROR1
37: INTERNAL COMMUNICATION ERROR2
38: INTERNAL SYSTEM ERROR
48: CRITICAL TEMPERATURE
49 : CRITICAL LED CURRENT
50: CRITICAL SUPPLY VOLTAGE
51: CRITICAL SPEED
52: CRITICAL ACCELERATION
53: COUNTER OVERFLOW
54: INTERNAL MONITORING ERROR
66: INTERNAL RESOURCE ACCESS ERROR
• Check motor feedback cable and connector
• Cycle control power
• Replace motor if fault continues
• Check feedback shield connection
• Reduce shock and vibration to motor
FLT S49 – BRAKE SLIP FLT
Brake Slip Exception
Motor slip has exceeded brake slip tolerance.
Check motor brake.
FLT S54 – POSN ERROR
Excessive Position Error Fault
The position error of the position control loop has
exceeded the value given by Position Error Tolerance
for a time period given by Position Error Tolerance
Time.
• Check position loop tuning
• Increase the feedforward gain
• Verify sizing of the drive and motor
• Check motor power wiring
• Increase Position Error Tolerance and/or Position Error Tolerance
Time attribute values
FLT S55 – VEL ERROR
Excessive Velocity Error Fault
The velocity error of the velocity control loop has
exceeded the value given by Velocity Error Tolerance
for a time period given by Velocity Error Tolerance
Time.
• Check velocity loop tuning
• Reduce acceleration
• Verify sizing of the drive and motor
• Check motor power wiring
• Increase Velocity Error Tolerance and/or Velocity Error Tolerance
Time attribute values
FLT S56 – OVERTORQUE LIMIT
Overtorque Limit Fault
Motor torque has risen above user defined maximum
torque level given by Overtorque Limit for a time
period given by Overtorque Limit Time.
• Verify Torque Trim value
• Verify motion profile
• Verify sizing of the drive and motor
• Increase Overtorque Limit and/or Overtorque Limit Time attribute
values
FLT S57 – UNDERTORQUE LIMIT
Undertorque Limit Fault
Motor torque has dropped below user defined
minimum torque level given by Undertorque Limit for
a time period given by Undertorque Limit Time.
• Verify motion profile
• Verify sizing of the drive and motor
• Decrease Undertorque Limit and/or Undertorque Limit Time
attribute values
Table 56 - FLT Sxx Fault Codes (continued)
Exception Code on Display
Exception Text
Problem
Possible Solutions
Table 57 - FLT Mxx Fault Codes
Exception Code on Display
Exception Text
Problem
Possible Solutions
FLT M02 – MOTOR VOLTAGE
Motor Voltage Mismatch Fault
The configured voltage of the drive is greater than the
motor rated voltage. For example, a 400V-class drive
with a 200V-class motor.
Set the drive voltage to a lower value or replace motor with voltage
rating that matches the drive.
FLT M25 – COMMON BUS
DC Common Bus Fault
AC power was detected by the drive while configured
for shared DC operation.
• Check the drive power configuration from controller
• Check wiring
FLT M26 – RUNTIME ERROR
Runtime Error
The drive firmware encountered an unrecoverable
runtime error.
• Cycle control power
• Reset the drive
• Return drive for repair if fault continues
FLT M28 – SAFETY COMM
(2198-Hxxx-ERS2 drives only)
Safety Module Communication
Error
Communication with the safety hardware within the
drive has failed.
• Cycle control power
• Reset the drive
• Return drive for repair if fault continues