8 measuring material speed, Measuring material speed -31, Flyingsaw – Lenze EVS93xx FlyingSaw User Manual
Page 44: Example 1, Example
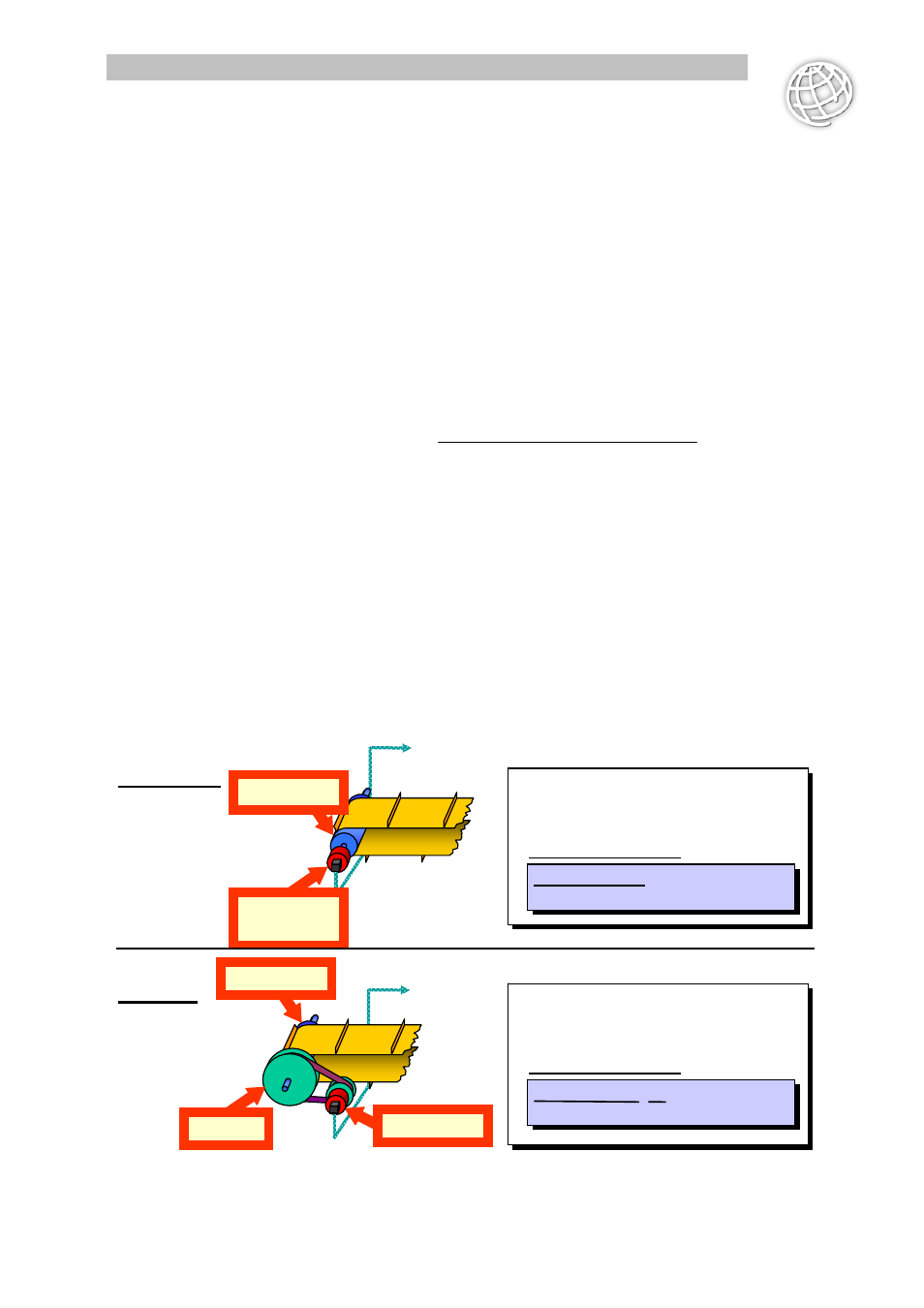
FlyingSaw
Functions
Prepared Solution Servo PLC / ECSxA 1.1 EN
page 3-31
3.8
Measuring material speed
To be able to set the cutting length for the sawing process, the material speed must be known.
The material speed can be measured in the following manner:
An encoder is fitted as close as possible to the "flying saw" without any slip. This encoder is
connected as an external encoder to the master frequency input X9 on the saw carriage drive.
The velocity and the material position are determined using the incremental position information
from the external encoder. At least 10 increments should be available each time accuracy is
required to determine the material speed sufficiently accurately.
π
*
]
[
]
/
[
]
/
[
mm
el
measurewhe
diameter
umdr
inc
pulse
encoder
mm
inc
resolution
master
−
−
=
−
On the use of the master frequency input (connector X9) as the master value, the incoming
pulses from the incremental encoder connected are counted. The speed of the master axis is
then determined with the aid of the number of encoder increments and the master frequency
constant (code C0425/000).
Example master value resolution
Example 1:
Number of encoder increments:
2048
[inc./rev.]
d = 150mm
2048
inc./rev
To the drive controller
(Connector X9)
Roller
Master value resolution:
2048 [inc./rev.]
π
.
150[mm]
= 4.346[inc./mm]
Encoder mounting:
direct
mounting
Example
Number of encoder increments:
Roller diameter: 150 [mm]
Master value resolution:
4096 inc./rev.
π
.
150[mm]
= 21.730 inc./mm
Encoder mounting:
ratio 5
d = 150mm
4096
i = 5 : 2
5
2
.
To the drive controller
(Connector X9)