Flyingsaw, Appendix – Lenze EVS93xx FlyingSaw User Manual
Page 137
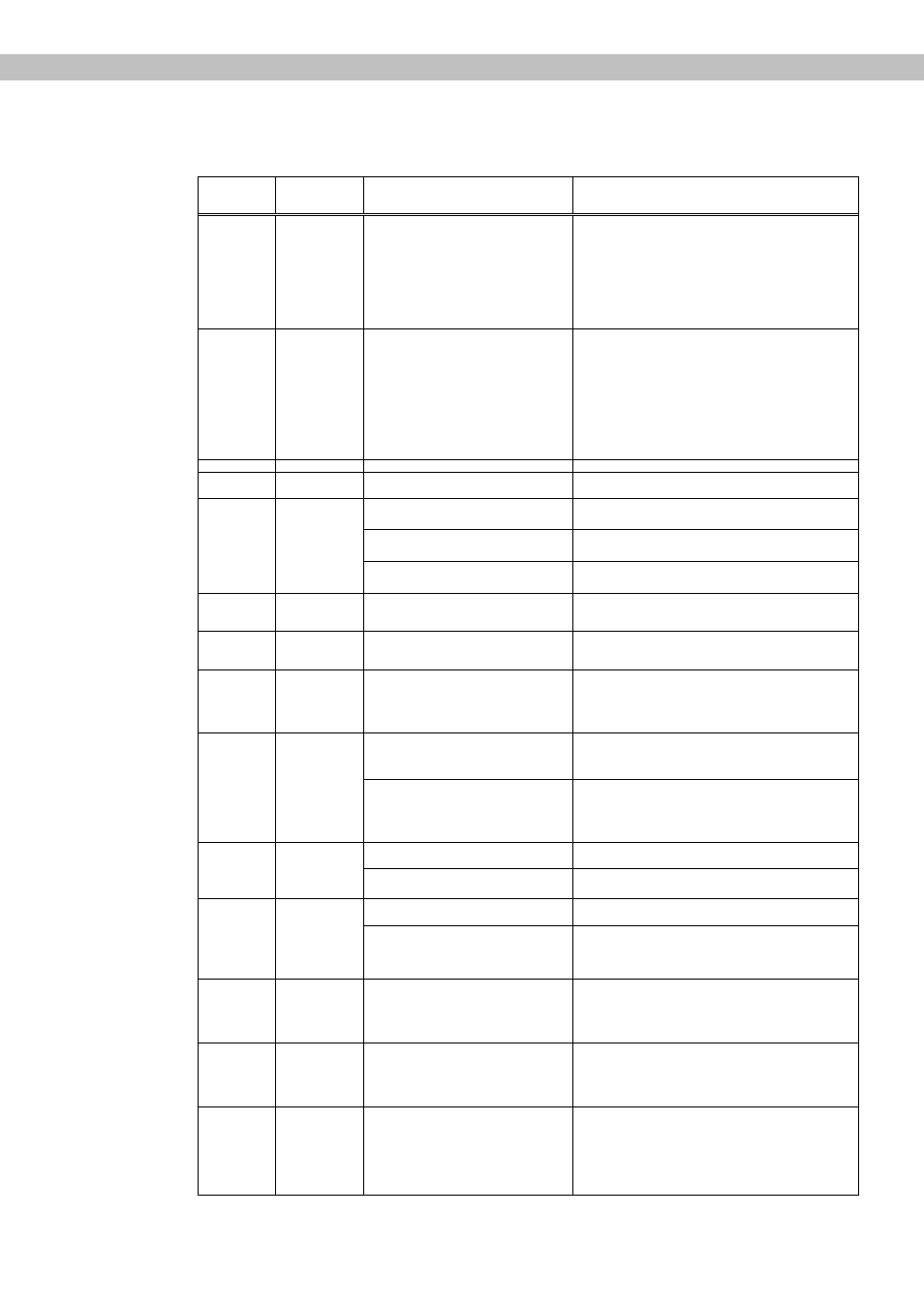
FlyingSaw
Appendix
Prepared Solution Servo PLC / ECSxA 1.1 EN
11-15
Error
number
Error code
Cause
Remedy
64
CE3
CAN-IN3 channel is not receiving any
data or is receiving erroneous data
Check CAN bus cable (connector X4)
Check CAN terminating resistor (on the first and last
CAN station)
Check configuration of the CAN node sending on CAN-
IN3
Check power supply to the CAN node sending on CAN-
IN3
Check monitoring time in code C0357/003 and increase
if necessary
65
CE4
Controller has received too many
erroneous messages over the CAN bus
and has disconnected itself from the bus
Check baud rate of all nodes
Check wiring:
-
Check bus terminating resistors
-
Check shield connection on the cables
- Check
PE
connection
-
Check bus load (e.g. using software tool
PCANView)
-
Reduce baud rate (CAUTION: pay attention to
CAN bus cable lengths)
66
CE5
CAN time-out (gateway function C0370)
Check settings in C0370.
70
U15
Undervoltage internal 15 V supply
voltage
Check servo axis voltage supply.
Processor is overloaded or program
execution problem
Reduce processor load: remove unnecessary function
blocks from the processing table (C0465/0xx)
Heavy interference on the control cables Lay control cables screened
71
CCr
Earth loop in the wiring
Wire as per EMC requirements (see System Manuals
"9300", p. 4-34)
72
Pr1
Error on transferring the parameter set
CAUTION: default setting is loaded
automatically!
Set the required parameters and save safe against
mains failure in the EPROM using code C0003/000
74
PEr
Error in the internal program execution
Read parameter set and send together with the source
project to Lenze for further analysis, consultation with
Lenze necessary (service hotline: (+49) 5154 82-1111)
75
Pr0
Invalid data in the EEPROM on loading
the parameters from the EEPROM to the
RAM
CAUTION: default setting is loaded
automatically!
Set the required parameters and save safe against
mains failure in the EPROM using code C0003/000, then
switch mains/shutdown the control voltage once
Error on transferring the parameters from
the EEPROM to the RAM
Read parameter set and send together with the source
project to Lenze for further analysis, consultation with
Lenze necessary (service hotline: (+49) 5154 82-1111)
79
PI
Use of a parameter set in the GDC
software that does not match the device
(9300EI/ET).
Use parameter set that matches the controller in the
GDC software, transfer this again to the controller and
save safe against mains failure in the controller using
C0003/000, then switch mains/shutdown the control
voltage once
Resolver cable partially or entirely open
circuit/disconnected
Check resolver cable for wire breakage
Check resolver
82
Sd2
Resolver not fitted/not connected
Disable monitoring via the code C0586/000 = 3, if a
resolver is not used
Encoder cable open circuit
Disconnect cable from X9 and check for wire breakage
83
Sd3
Pin 8 on input X9 open circuit
Apply +5V DC to pin 8 on input X9
OR:
Disable monitoring using code C0587/000 = 3
85
Sd5
Current master value on X6 (terminals 1
and 2) less than 2mA
Check cable for wire breakage
Check master current value encoder
Check setpoint configuration using C0034/000
OR:
Disable monitoring using code C0598/000 = 3
86
Sd6
Motor temperature sensor on X8 is
providing undefined values
Check cable on X8 for correct seating and wire breakage
Disconnect thermocouple (PTC/KTY) and measure
resistance (must not be
∞)
OR:
Disable monitoring using code C0594/000 = 3
87
Sd7
Absolute value encoder with RS485
interface is not sending any data
Check cable on X8 for correct seating and wire breakage
Check absolute value encoder for correct function
Set supply voltage to 8.0V using C0421/000
Encoder with HIPERFACE interface not connected
CAUTION: after rectifying the cause of the error, fully
isolate the servo controller