Appendix fidfl - manual tuning 80, Appendix “d” - manual tuning – Red Lion TSC User Manual
Page 82
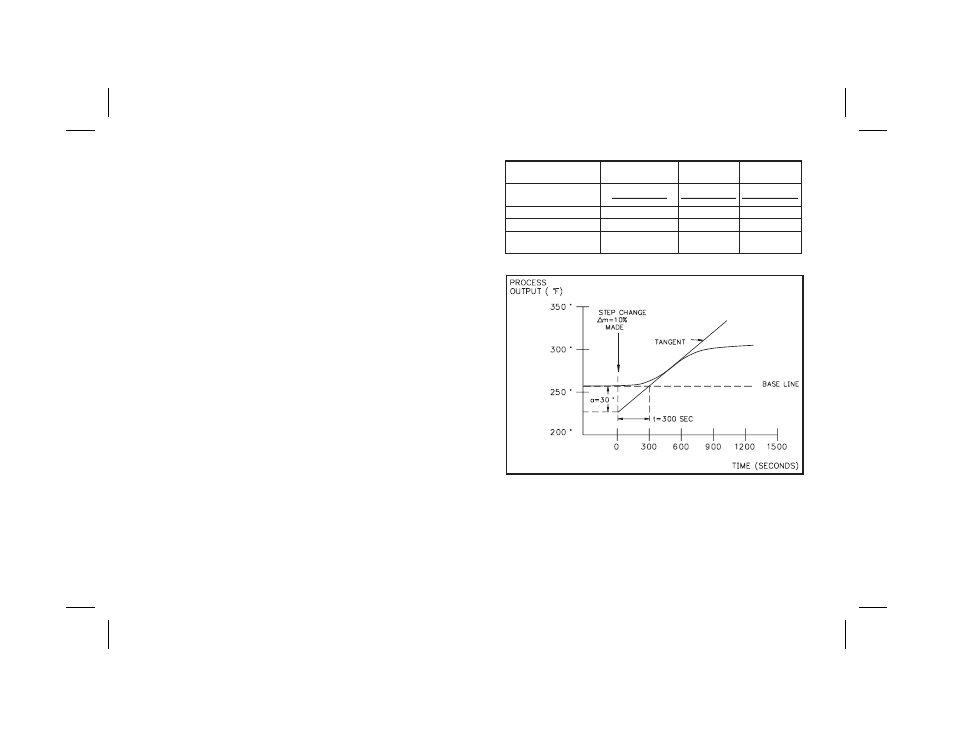
APPENDIX “D” - MANUAL TUNING
OPEN LOOP STEP RESPONSE METHOD
The Open Loop Step Response Method is a tuning procedure that does not
induce process oscillations. This method involves making a step change to the
process and observing the process reaction. A strip paper recorder or other
high resolution data logging equipment is required for this procedure. This
procedure requires that all disturbances to the process are minimized because
the data is influenced by these disturbances.
1) Connect a chart recorder to log temperature and set the paper speed
appropriate for the process.
2) Set the controller to manual (user) control mode.
3) Allow the process to stabilize (line out).
4) Make a step change of 10% or more in the controller output. It may be
necessary to increase the size of the step to yield a sufficient process
reaction curve.
5) Record the response of the process. Use the information from the table to
calculate the controller tuning values. The PID tuning parameters are
determined graphically from the Process Reaction Curve Figure. Draw a
vertical line at the moment the step change was made. Draw a line (labeled
tangent) through the process reaction curve at its maximum upward slope.
Extend this line to intersect the vertical line.
Example: From the Process reaction Curve
a = 30°, t = 300 sec, step = 10%, thermocouple range = 1700°F.
For fast response:
Prop
=
35.3%
Intt
=
900 sec
dert
=
120 sec
OPdP
=
15
Parameter
Fast Response
Damped
Response
Slow
Response
Proportional Band (%)
20000a
Range
Step%
´
40000a
Range
Step%
´
60000a
Range
Step%
´
Integral Time (Sec)
3t
4t
5t
Derivative Time (Sec)
0.4t
0.4t
0.4t
Output Power
Dampening (Sec)
t/20
t/15
t/10
-80-
Process Reaction Curve