Red Lion TSC User Manual
Page 61
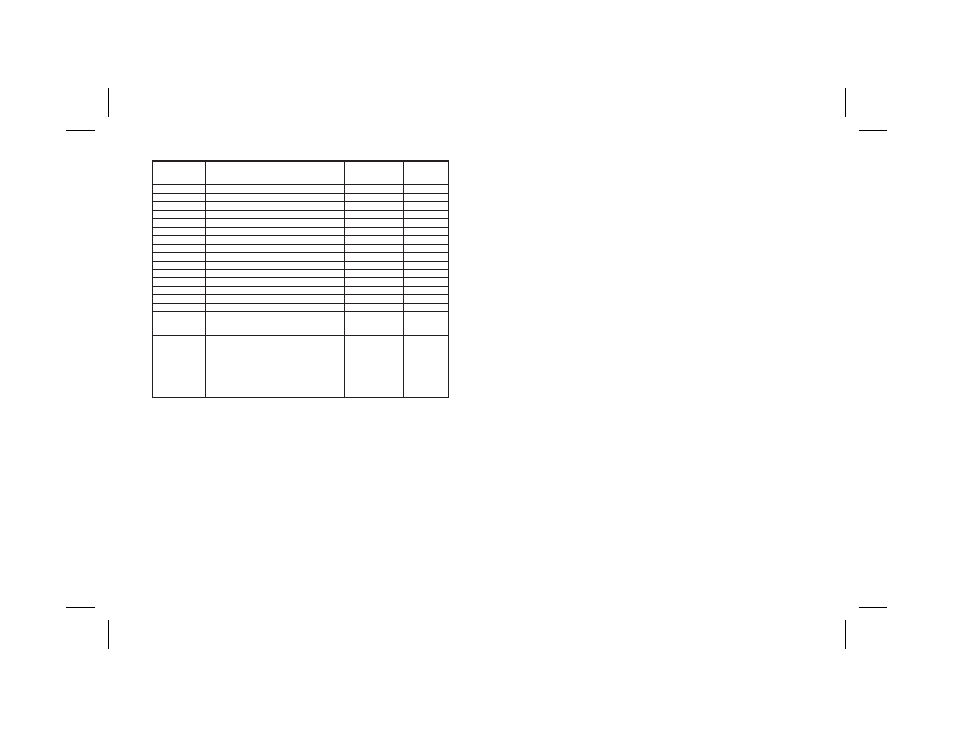
VALUE
IDENTIFIER
DESCRIPTION
SERIAL
MNEMONIC
UNITS
A
Temperature Display Value
TMP
F/C
B
Setpoint
SET
F/C
C
Output Power
PWR
%
D
Proportional Band
PBD
%
E
Integral Time
INT
S
F
Derivative Time
DER
S
G
Alarm 1
AL1
F/C
H
Alarm 2
AL2
F/C
I
Deviation
DEV
F/C
J
Output Power Offset
OFP
%
K
Setpoint Ramp Rate Q
RMP
R
L
Cooling Relative Gain
CRG
G
M
Cooling Deadband
CDB
F/C
O
Program Phase Time Remaining
TIM
M
Q
Program Phase Status
STS
--
S
Control Mode
1 - Automatic
2 - Manual (User)
--
--
U
1 = Start Profile 1 Operation
2 = Start Profile 2 Operation
3 = Start Profile 3 Operation
4 = Start Profile 4 Operation
5 = Stop Profile Operation
6 = Pause Profile Operation
7 = Continue Profile Operation
8 = Advance Profile to Next Phase
--
--
--
--
--
--
--
--
--
--
--
--
--
--
--
--
Note: The % output power can be changed only if the controller is in the
manual mode of operation.
Profile data cannot be configured via the serial interface. Only status
changes can be made to a running profile.
Q
The Auto Setpoint Ramp Rate is not associated with a profile. This
parameter is programmed in the Input Parameter Module (1-IN) (see
Setpoint Ramp Rate for details).
A command string is constructed by using a command, a value identifier,
and a data value if required. The Data value need not contain the decimal point
since it is fixed within the unit, when programmed at the front panel. The TSC
will accept the decimal point, however it does not interpret them in any way.
Leading zeros can be eliminated, but all trailing zeros must be present.
Example: If an alarm value of 750.0 is to be sent, the data value can be
transmitted as 750.0 or 7500. If a 750 is transmitted, the alarm value is
changed to 75.0 in the unit.
The address command allows a transmission string to be directed to a
specific unit on the serial communications line. When the unit address is zero,
transmission of the address command is not required. For applications that
require several units, it is recommended that each unit on the line be assigned a
specific address.
If they are assigned the same address, a Transmit Value Command, will cause
all the units to respond simultaneously, resulting in a communication collision.
The command string is constructed in a specific logical sequence. The TSC
does not accept command strings that do not follow this sequence. Only one
operation can be performed per command string.
Thefollowingprocedureshouldbeusedwhenconstructingacommandstring.
1. The first two to three characters of the command string must consist of the
Address Command (N) and the address number of the unit (0-99). If the unit
address is zero, the address command and number need NOT be sent.
2. The next character in the command string is the command that the unit is to
perform (P, R, T, C, or V).
3. A Value Identifier is next if it pertains to the command. The command P
(print) does not require a Value Identifier.
4. The numerical data will be next in the command string if the “Change
Value” or “Control Action” command is used.
5. All command strings must be terminated with an asterisk
Q
(2AH). This
character indicates to the unit that the command string is complete and
begins processing the command.
Below are typical examples of command strings.
Ex. 1 Change Proportional Band Value to 13.0% on the unit with an address
of 2.
Command String: N2VD130
Q
Ex. 2 Transmit the Temperature Value of the unit with an address of 3.
Command String: N3TA
Q
Ex. 3 Reset Alarm Output 1 of the unit with an address of 0.
Command String: RG
Q
Ex. 4 Start profile 1 of the unit with an address of 13.
Command String: Nl3CU1
Q
If illegal commands or characters are sent to the TSC, the string must be
re-transmitted.
-59-