16 menu structure, 1 monitor 1 (menu 1) – R&M Materials Handling HOIST MONITORS User Manual
Page 82
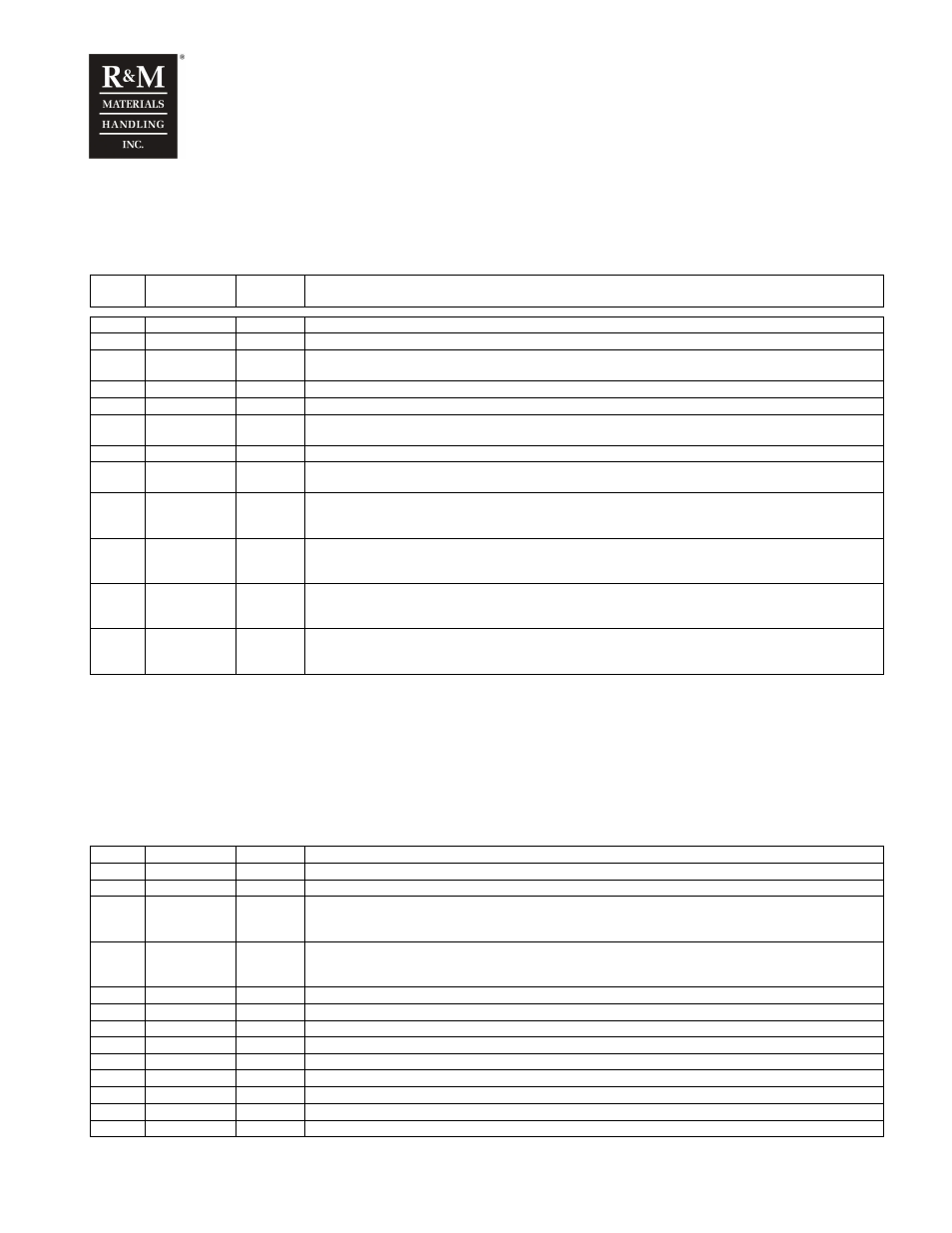
R&M Materials Handling, Inc.
4501 Gateway Boulevard
Springfield, Ohio 45502
P.: (937) 328-5100
FAX: (937) 325-5319
82/105
R&M Materials Handling, Inc. reserves the right to alter or amend the above information without notice.
16 Menu structure
16.1 Monitor 1 (Menu 1)
1
Monitor 1
Read only menu for condition monitoring values and measured values.
Accessible with the customer’s password.
Param. Name
Value
Description
1-1
Cond mon
Condition monitoring menu
1-1-1
SWP%
“n” %
Remaining Safe Working Period of the hoist in percentage, starting from 100%. When the SWP counter
descends to 0% (or even negative), a General Overhaul must be carried out.
1-1-2
Starts
“n”
Total number of starts of the hoist in either up or down direction. *1)
1-1-3
Run time
“n” h
Total running time of the hoist in hours. *2)
1-1-4
Cycles
“n”
Total number of hoisting cycles. *1). The number increases by one, when a load value increase more
than 20% of the rated load is lifted.
1-1-5
Mean load
“n.n” t
Average of the handled load during the recorded cycles.
1-1-6
Br SWP%
“n” %
Remaining Safe Working Period of the brake in percentage. The SWP for the brake is calculated
according to the number of Starts and E-stops.
1-1-7
MFI1 RT
“n” h
Total hours of running time, when MFI1 input is closed. Can be used to monitor the total running time of
another machinery (i.e. the trolley drive). Active only if parameter 4-1-1 is set to “ST/RT” and the MFI1
input is connected. *2)
1-1-8
MFI1 ST
“n”
Total amount of starts, when MFI1 input is closed. Can be used to monitor the total amount of starts of
another machinery (i.e. the trolley drive). Active only if parameter 4-1-1 is set to “ST/RT” and the MFI1
input is connected. *1)
1-1-9
MFI2 RT
“n” h
Total hours of running time, when MFI2 input is closed. Can be used to monitor the total running time of
another machinery (i.e. the bridge drive). Active only if parameter 4-2-1 is set to “ST/RT” and the MFI2
input is connected. *2)
1-1-10
MFI2 ST
“n”
Total amount of starts, when MFI2 input is closed. Can be used to monitor the total amount of starts of
another machinery (i.e. the bridge drive). Active only if parameter 4-2-1 is set to “ST/RT” and the MFI2
input is connected *1)
The values on the display are present with five digits.
*1) there is no unit name, all five digits are used to show the value.
The letter “k” appears when the value is greater than 99.999, indicating the full thousands.
The letter “M” appears when the value is greater than 1.000.000, indicating the full millions.
*2) a unit name is used (i.e. hours “h”), there are only four digits available to present the value.
The letter “k” appears when the value is greater than 9.999, indicating the full thousands.
The letter “M” appears when the value is greater than 1.000.000, indicating the full millions.
A dot will appear on the correct spot to indicate the decimals
Param. Name
Value
Description
1-2
Measure
Measurement menu
1-2-1
Act. Load
“n.n” t
The measured actual load value of the solo hoist connected to the unit.
1-2-2
Temp 1
“nnn” C
Temperature measured at thermistor input 1. Only functional when par. 4-4-1 is set to “”x”NTC” and a
NTC-type of thermistor is connected across terminals X2: 21-22. Otherwise the display shows “NA” (Not
Available)
1-2-3
Temp 2
“nnn” C
Temperature measured at thermistor input 2. Only functional when par. 4-5-1 is set to “”x”NTC” and a
NTC-type of thermistor is connected across terminals X2: 23-24. Otherwise the display shows “NA” (Not
Available)
1-2-4
Supply L1
“nnn” V
RMS line voltage of phase L1, measured at terminal X1: 19; VAC
1-2-5
Supply L2
“nnn” V
RMS line voltage of phase L2, measured at terminal X1: 17; VAC
1-2-6
Supply L3
“nnn” V
RMS line voltage of phase L3, measured at terminal X1: 15; VAC
1-2-7
Motor I1
“nn.n” A
RMS motor current of phase U. Only functional when par. 4-7-1 is set to “Motor”
1-2-8
Motor I2
“nn.n” A
RMS motor current of phase V. Only functional when par. 4-7-1 is set to “Motor”
1-2-9
Motor I3
“nn.n” A
RMS motor current of phase W. Only functional when par. 4-7-1 is set to “Motor”
1-2-10
Ain1 value
“n.nn” V
Measured voltage at analogue input AIN1. Voltage across terminals X2: 26-30; VDC
1-2-11
Ain2 value
“n.nn” V
Measured voltage at analogue input AIN2. Voltage across terminals X2: 27-30; VDC
1-2-12
Ain3 value
“n.nn” V
Measured voltage at analogue input AIN3. Note that there is no function behind AIN3. This input can be