5 run and fault supervision – R&M Materials Handling HOIST MONITORS User Manual
Page 27
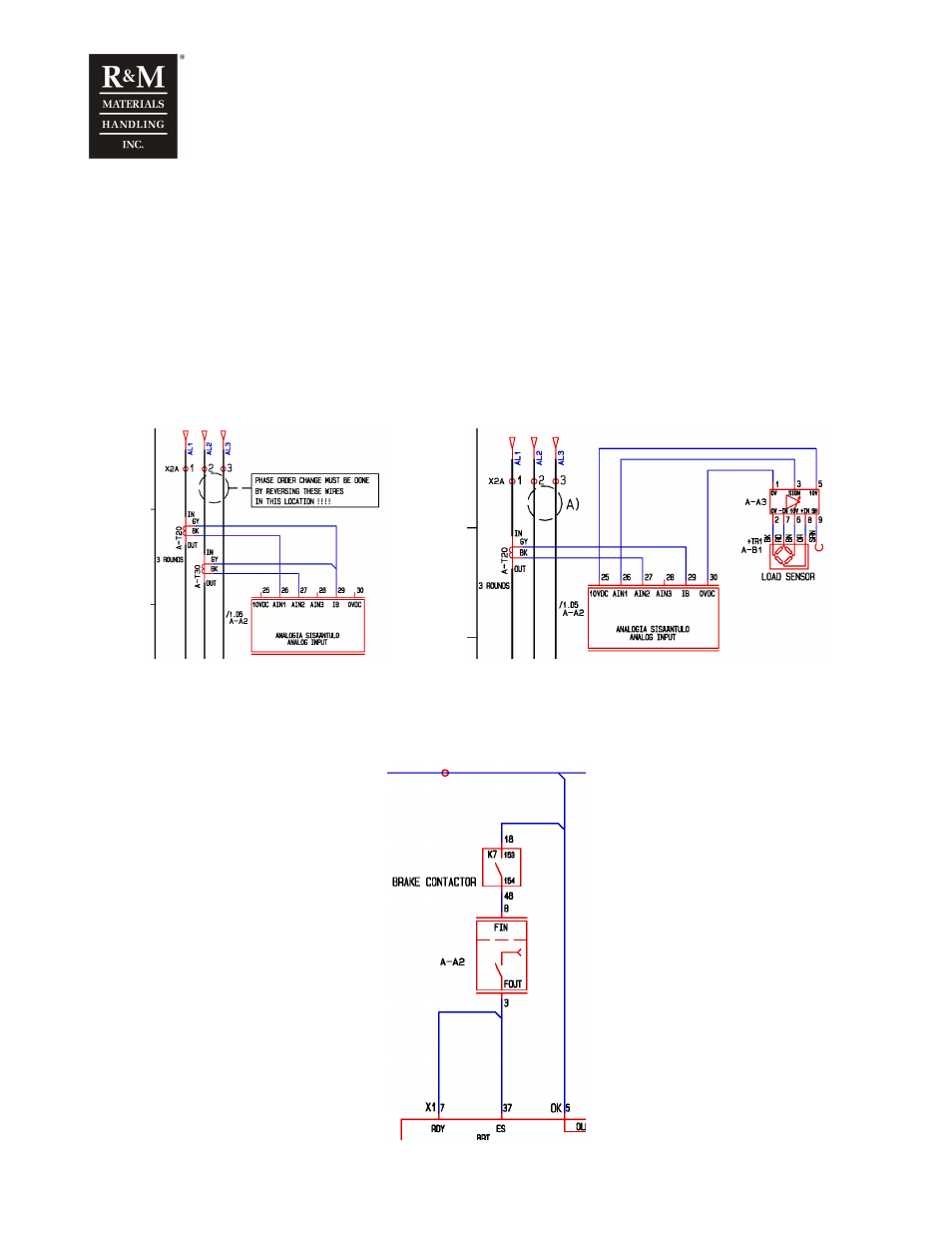
R&M Materials Handling, Inc.
4501 Gateway Boulevard
Springfield, Ohio 45502
P.: (937) 328-5100
FAX: (937) 325-5319
27/105
R&M Materials Handling, Inc. reserves the right to alter or amend the above information without notice.
5.5 RUN and fault supervision
The hoisting and lowering request from the control station will come as an input to the hoist-monitoring
unit. Before the hoist can start the requested motion, the hoist-monitoring unit checks if it is safe to
proceed. If no limitations are detected, the hoist-monitoring unit will activate the requested output and
movement will start. The unit monitors a feedback signal. When the feedback signal drops during
running, the motion will stop immediately. During the starting sequence, the feedback signal must be on
within 200ms in contactor control, and within 800ms in inverter control.
2 Speed Hoisting: Unit monitors a feedback signal from a current transformer to analog input 2. The
current transformer measures the input current to the motor in 2 speed hoisting. During the starting
sequence, the feedback signal must be on within 200ms in contactor control. When the feedback signal
drops during running, the motion will stop immediately.
2 Speed, load measurement by motor
2 Speed, load measurement by sensor
When the unit supervises a hoist inverter application a brake contact from AK7 is connected to the FIN
input, terminal 8, to be a brake open feedback signal. If the brake contactor does not energize during
start or de-energizes during hoisting (initiated by a fault or due to brake failure) the unit will disconnect
control voltage from the FOUT signal output, terminal 3, feeding the ES and RDY inputs of the inverter.
During the starting sequence, in inverter control, the feedback signal at FIN must be on within 800ms.