11 overload protection – motor torque, 2 motor torque calculation parameters – R&M Materials Handling HOIST MONITORS User Manual
Page 55
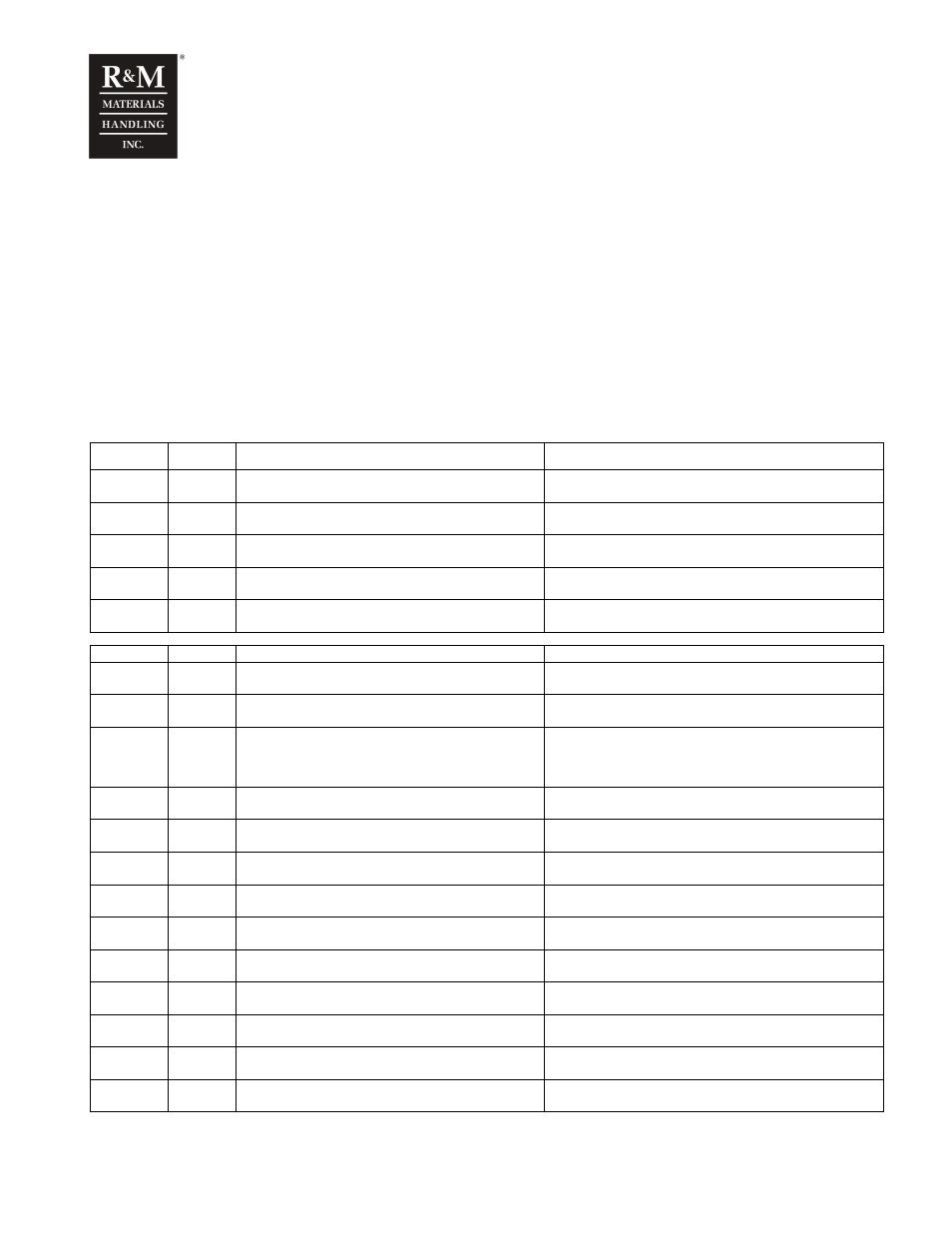
R&M Materials Handling, Inc.
4501 Gateway Boulevard
Springfield, Ohio 45502
P.: (937) 328-5100
FAX: (937) 325-5319
55/105
R&M Materials Handling, Inc. reserves the right to alter or amend the above information without notice.
11 Overload protection – Motor torque
11.1 Overload protection instructions
11.1.1 Motor torque calculation-system
The parameters as described in the table “Motor torque calculation parameters” must be checked and
if needed adjusted, before the calibration sequence is carried out. The unit used these values in order to
calculate the actual load. After the calibration has been done, it is recommended to write down the values
of the parameters of group “3-2 MC values” and “4-7 Load param”.
11.1.2 Motor torque calculation parameters
Parameter
Value
Description
Note
4
Start-up
Start-up menu
Accessible with password 4: 8124
4-4
T1
T1 parameters
4-4-1
T1 operat.
B NTC
Determines the type of thermistors in the low speed
windings, connected to the temperature 1 input
Type “B” is presently used as standard
4-5
T2
T2 parameters
Accessible with password 4: 8124
4-5-1
T2 operat.
B NTC
Determines the type of thermistors in the fast speed
windings, connected to the temperature 2 input
Type “B” is presently used as standard
Parameter
Value
Description
Note
4-7
Load param
Load calculation menu
Accessible with password 4: 8124
4-7-1
Load meas.
Motor
Selects the motor torque calculation method
4-7-2
Load rate%
10
Load increase rate for controlling the hoisting in two
step control, speed change to fast speed is allowed
when actual load change within 200ms < parameter 4-
7-2.
See also description in chapter “Sudden load increase
supervision” of this manual for further details
4-7-3
R0_F
0.00 –
1000
Resistance of the fast speed windings at temperature
T0
If accurate measurements can not be performed, one has to
rely on the information given in the motor data files.
4-7-4
R0_S
0.00 –
1000
Resistance of the slow speed windings at temperature
T0
If accurate measurements can not be performed, one has to
rely on the information given in the motor data files.
4-7-5
T0
“nn” C
Temperature T0 “nn” at the time when measurement is
carried out, in degrees Celsius
If accurate measurements can not be performed, one has to
rely on the information given in the motor data files.
4-7-6
Temp_slow
T1
Temperature measurement channel for the motor slow
speed windings
4-7-7
Temp fast
T2
Temperature measurement channel for the motor fast
speed windings
4-7-8
C2F
143
Coefficient 2 for fast speed
Additional motor losses in fast speed windings. Setting is
motor dependent
4-7-9
C2S
236
Coefficient 2 for slow speed
Additional motor losses in slow speed windings. Setting is
motor dependent
4-7-10
C1F
165
Coefficient 1 for fast speed
Iron losses in fast speed windings. Setting is motor
dependent
4-7-11
C1S
255
Coefficient 1 for slow speed
Iron losses in slow speed windings. Setting is motor
dependent
4-7-12
ki
0.0 - 300.0 Reduction factor for current transformer [A/V]
See appendix 3 “Current Transformer Table” of this
manual for the correct setting