R&M Materials Handling HOIST MONITORS User Manual
Page 32
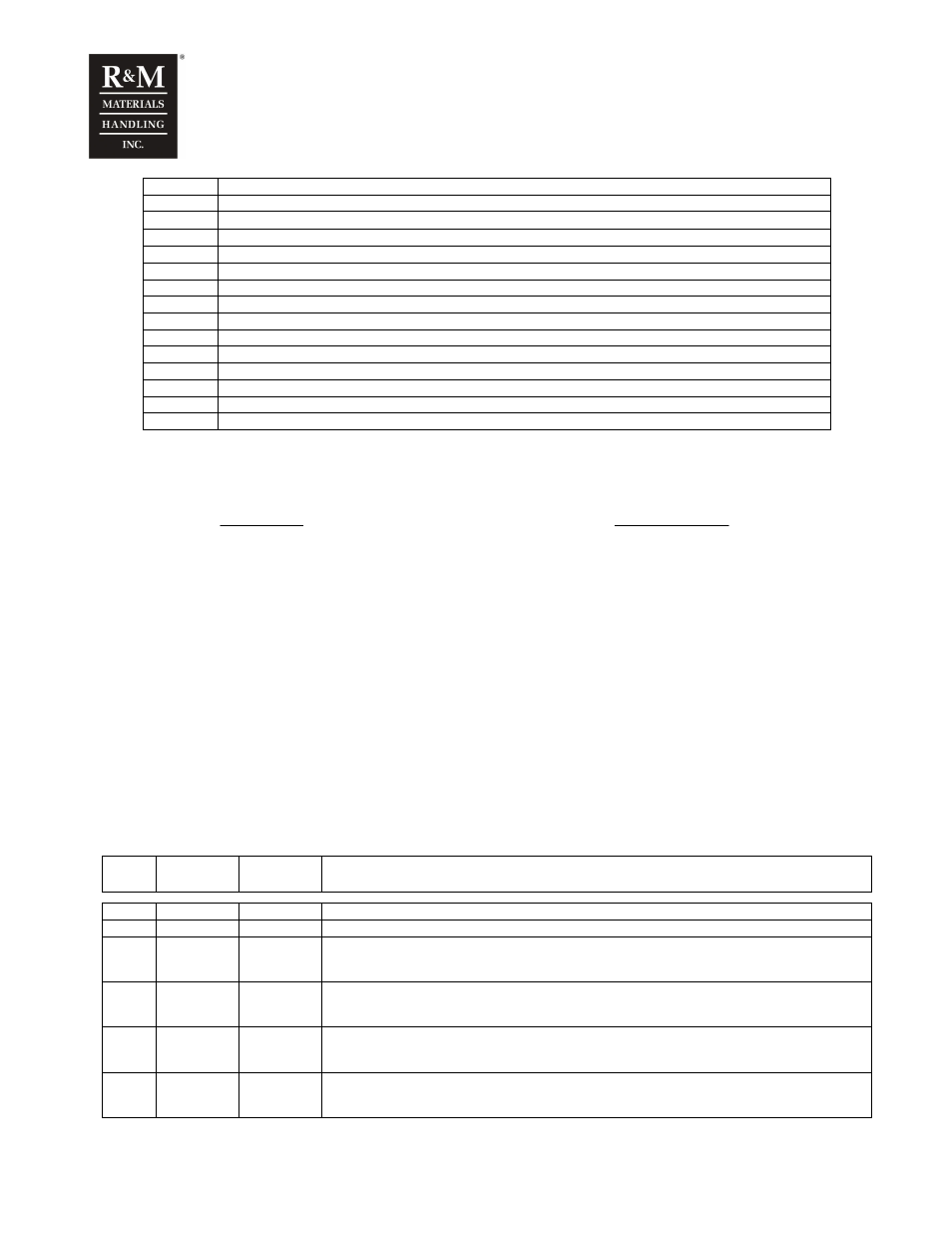
R&M Materials Handling, Inc.
4501 Gateway Boulevard
Springfield, Ohio 45502
P.: (937) 328-5100
FAX: (937) 325-5319
32/105
R&M Materials Handling, Inc. reserves the right to alter or amend the above information without notice.
SRT3
Load sum with hoist running time, third power. The parameter 2-13
I
Time period number (Time period is 0,1s)
∆
∆
∆
∆
tf
i
Run time in fast speed with load
i
∆
∆
∆
∆
ts
i
Run time in slow speed with load
i
SR
Speed ratio. Two-speed systems: slow-fast (i.e. 6); Inverter drives: always 1
load
i
Actual load in period i.
nom.load
Hoist’s nominal load. The parameter 6-4
SL3
Load sum with hoist cycles, the third power. The parameter 2-17.
load
k
The load difference between maximum load and initial load within the hoist cycles k
k
Hoist cycles number
SWPRT%
SWP% value calculated with hoist running time. The parameter 2-12
D_SRT3
Designed running hours, power three. The parameter 6-10
SWPHC%
SWP% value calculated with hoist cycles. The parameter 2-15.
D_SL3
Designed constraint for hoisting cycles, power three. The parameter 6-12
SWP%
Remaining Safe Working Period of the hoist in percentage, starting from 100%. The parameter 1-1-1.
SWP% is calculated when the parameter 2-13 SRT3 and the parameter 2-17 SL3 are known.
Example. The parameters 2-13 SRT3 is 163h; the parameter 2-17 SL3 is 3780 and hoist duty class is M4
(
)
%
6
,
79
%
100
800
163
800
%
=
⋅
−
=
SWPRT
(
)
%
25
,
84
%
100
24000
3780
24000
%
=
⋅
−
=
SWPHC
SWP% = min {SWPRT%, SWPHC%}= 79,6%
When SWP% is known the parameter 2-13 SRT3 and the parameter 2-17 SL3 can be calculated.
See section “Replacement instructions” of this manual.
6.2.4 Hoist cycles counter
Total number of hoisting cycles. The number increases by one, when the hoist is started to down
direction if a load difference was bigger than 20% of the rated load between a maximum load and a initial
load within the last hoisting motion.
6.2.5 Run time and start counter for trolley and bridge
In addition to the hoist run-time and starts counter, the hoist-monitoring unit can be programmed to count
the total run-time and starts of either the trolley and/or bridge travel motion. When this option is activated,
a complete overview of the usage of the crane is recorded.
1
Monitor 1
Read only menu for condition monitoring values and measured values.
Accessible with the customer’s password.
Param. Name
Value
Description
1-1
Cond mon
Condition monitoring menu
1-1-7
MFI1 RT
“n” h
Total hours of running time, when MFI1 input is closed. Can be used to monitor the total running
time of another machinery (i.e. the trolley drive). Active only if parameter 4-1-1 is set to “ST/RT”
and the MFI1 input is connected.
1-1-8
MFI1 ST
“n”
Total amount of starts, when MFI1 input is closed. Can be used to monitor the total amount of
starts of another machinery (i.e. the trolley drive). Active only if parameter 4-1-1 is set to “ST/RT”
and the MFI1 input is connected.
1-1-9
MFI2 RT
“n” h
Total hours of running time, when MFI2 input is closed. Can be used to monitor the total running
time of another machinery (i.e. the bridge drive). Active only if parameter 4-2-1 is set to “ST/RT”
and the MFI2 input is connected.
1-1-10
MFI2 ST
“n”
Total amount of starts, when MFI2 input is closed. Can be used to monitor the total amount of
starts of another machinery (i.e. the bridge drive). Active only if parameter 4-2-1 is set to “ST/RT”
and the MFI2 input is connected