R&M Materials Handling HOIST MONITORS User Manual
Page 19
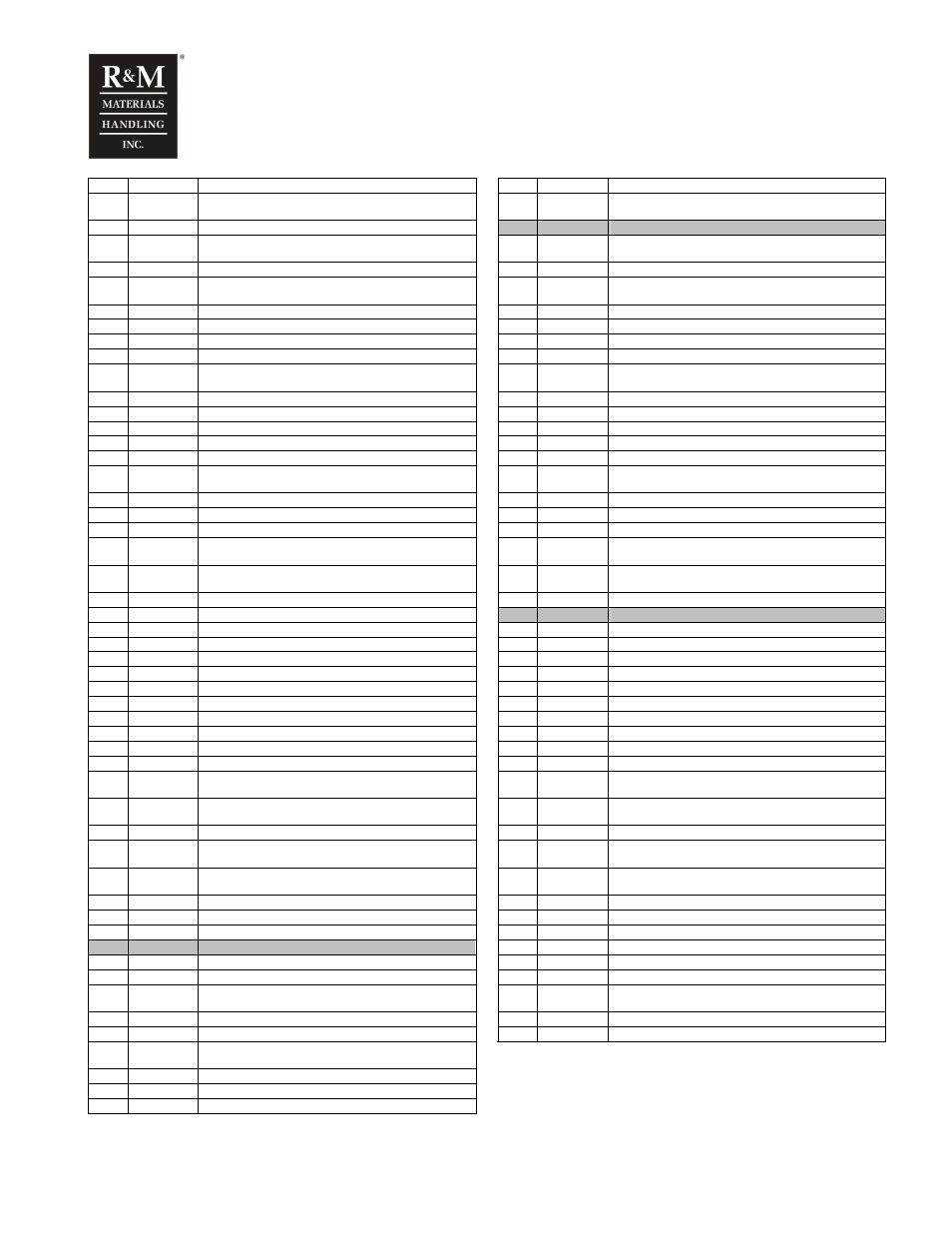
R&M Materials Handling, Inc.
4501 Gateway Boulevard
Springfield, Ohio 45502
P.: (937) 328-5100
FAX: (937) 325-5319
19/105
R&M Materials Handling, Inc. reserves the right to alter or amend the above information without notice.
4-3
ROUT
Relay output parameters
5-3
Reset log
Resets the fault log by pushing the ENT button..
4-3-1
ROUT oper. Selects the function of the relay output
5-3
Reset log ?
The reset action must be confirmed by pushing the ENT
button once more
4-3-2
ROUT logic
The operation logic of the relay:
6
Design
Design values menu. Accessible password level 6
4-3-3
ROUT LoadX The load limit to switch the relay is entered here
6-1
Hoist name
Identifying letter of the hoist-monitoring unit, A, B, C, D
or E.
4-3-4
TempX meas The temperature measurement operation
6-2
Unit No
The serial number of the hoist.
4-3-5
TempX lim
The temperature limit
6-3
Class
Mechanical class for the hoist according to the FEM /
ISO duty classes.
4-4
T1
Temperature measurement channel 1 parameters
6-4
Nom. Load
Rated load of the single hoist connected to the unit
4-4-1
T1 operat.
Selects the function channel 1.
6-5
Nominal ED Rated ED value of the hoist
4-5
T2
Temperature measurement channel 2 parameters
6-6
Sp ratio
Speed ratio.
4-5-1
T2 operat.
Selects the function channel 1.
6-7
Max ST
Maximum allowed number of starts
4-6
AOUT
Analogue output parameters
6-8
Max E-stop
Maximum allowed number of interrupted hoists
(emergency stops)
4-6-1
AOUT oper. Selects the function of the analogue output
6-9
Max RT
Maximum allowed run-time in hours
4-6-2
Zero load
Sets the voltage level with zero-load. Range 0…10V
6-10
D SRT3
Designed running hours, power three.
4-6-3
Nom. Load
Sets the voltage level with rated load. Range 0…10V
6-11
D SRT8
Designed running hours, power eight.
4-7
Load param Load calculation parameters
6-12
D SL3
Design constraint for hoisting cycles, power three
4-7-1
Load meas.
Selects the load calculation method:
6-13
D SL8
Design constraint for hoisting cycles, power eight
4-7-2
Load rate%
Load increase rate for controlling the hoisting in two step
control.
6-14
MaxST MFI1 Max number of MFI1 starts.
4-7-3
R0_F
Resistance of fast speed windings at temperature T0
6-15
MaxRT MFI1 Max running time for MFI1.
4-7-4
R0_S
Resistance of slow speed windings at temperature T0
6-16
MaxST MFI2 Max number of MFI2 starts.
4-7-5
T0
Resistance measuring temperature T0
6-17
MaxRT MFI2 Max running time for MFI2.
4-7-6
Temp_slow
Temperature measurement channel for the motor slow
speed windings.
6-18
Max Br
Max number of braking actions.
4-7-7
Temp_fast
Temperature measurement channel for the motor fast
speed windings.
6-19
Max Control Max number of Control (starts)
4-7-8
C2F
Coefficient 2 for fast speed
6-20
Password
Set password level 1 (4digits).
4-7-9
C2S
Coefficient 2 for slow speed
7
GO-setup
GO-settings menu. Accessible password level 7
4-7-10 C1F
Coefficient 1 for fast speed
7-1
Cycles
Number of hoisting cycles
4-7-11 C1S
Coefficient 1 for slow speed
7-2
MFI1 RT
MFI1 running time
4-7-12 ki
Reduction factor for current transformer [A/V]
7-3
MFI1 ST
MFI1 starts
4-7-13 Acc-t slow
Acceleration time from stop to slow speed.
7-4
MFI2 RT
MFI2 running time
4-7-14 Acc-t fast
Acceleration time from slow speed to fast speed.
7-5
MFI2 ST
MFI2 starts
4-8
Hoist ctrl
The selection for the hoist control method
7-6
RT slow
Run-time in slow speed
4-9
Slack rope
Slack rope function parameters
7-7
RT fast
Run-time in fast speed
4-9-1
SR select
Selects the slack rope function
7-8
No. OT
Number of hoist motor overtemperature incidents.
4-9-2
Load limit
The slack rope limit
7-9
No. OL
Number of hoist overload incidents
4-10
Single sup
7-10
E-stops
Number of emergency stops
4-10-1 OT run ?
Selects the action when the motor temperature exceeds
the limit or when “Fault, Br wear” occurs
7-11
ST up
Number of starts in up direction
4-10-2 OT limit
When NTC type sensor is applied the limit value for the
hoist motor overtemperature
7-12
ST down
Number of starts in down direction
4-10-3 Supply sup
Selects the supply voltage supervision.
7-13
ST fast
Number of starts to fast speed (two step control only)
4-11
Comm hoist The settings for common hoisting (multi-hoist
applications)
7-14
Max ED
Maximum ED value
4-11-1 Hoist cnt
The number of units connected with CAN bus. Range:
1…5
7-15
Over ED
Number of cases where ED value has exceeded the
rated ED value
4-11-2 Run sup.
Common hoisting supervision
7-16
SRT3
Load sum with hoist running time, third power
4-11-3 B OL
Bridge overload protection
7-17
SRT8
Load sum with hoist running time, eight power
4-11-4 B nom load
Rated load of the bridge
7-18
SL1
Load sum with hoist cycles, the first power (mean load)
5
Service
Start- menu. Accessible password level 5
7-19
SL3
Load sum with hoist cycles, the third power
5-1
S limits
The limit values to indicate the need for service.
7-20
SL8
Load sum with hoist cycles, the eight power
5-1-1
S Run time
Run time service limit
7-21
Power on
The total power on time for hoist control unit
5-1-2
S starts
Service limit for the number of starts
7-22
Temp Index
The power on time weighted with the hoist control unit
temperature
5-1-3
S SWP%
Service limit for SWP%
7-23
Max load
The maximum value of the measured load
5-1-4
S Br SWP% Service limit for the hoist brake service life
7-24
Br Count
The brake wear counter.
5-2
Fault log
The logger for the latest fault situations, the number
“n” indicates the number of faults in the logger
5-2-1
F_”XXX”
The latest fault.
5-2-2
F_”XXX”
The second latest fault.
5-2-“n” F_”XXX”
The “n” latest fault (highest number is 30).