R&M Materials Handling HOIST MONITORS User Manual
Page 38
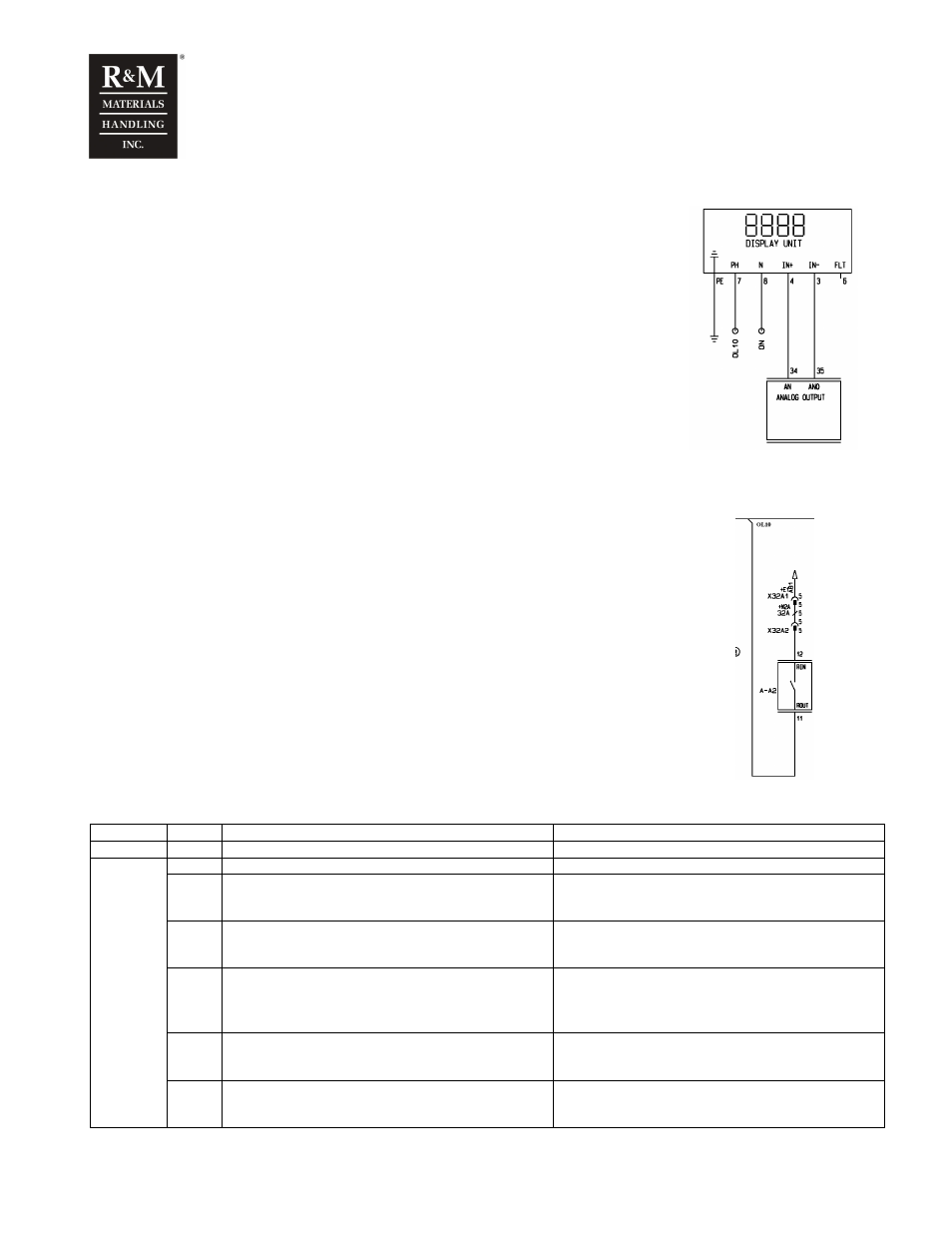
R&M Materials Handling, Inc.
4501 Gateway Boulevard
Springfield, Ohio 45502
P.: (937) 328-5100
FAX: (937) 325-5319
38/105
R&M Materials Handling, Inc. reserves the right to alter or amend the above information without notice.
7.5.2 Analogue output connections
The load display (or other device) is connected to the analogue output
terminals AN and ANO (terminals 33 and 34). The connected device must
have an input resistance of at least 1kΩ in order to prevent the analogue
output being overloaded.
The analogue output has a filtering delay of 1000ms before SW
2.100. In the SW 2.100 and the later SW the filtering delay is 200ms
to enable faster update of load information.
Consult on the specifications of the connected device for the minimum and
maximum required voltage range (difference between zero load voltage
and rated load voltage), and upper and lower limits.
7.6 Free relay output
The hoist-monitoring unit has one free relay output, connected between
terminals 11 and 12, which can be programmed to operate under the
following conditions:
Overload
Load limit
OK/Warning/Fault
Ready/Fault
Motor over temperature
Connected to the relay output can be any signalling device (optical or
acoustic) or an additional control circuit to react on any of the above
situations.
Note that only one of the options can be chosen at a time.
Relay’s switch’s technical data: 230VAC; 3A
Free relay output parameters
Parameter
Value
Description
Note
4-3 ROUT
Relay output parameters
Accessible with password 4: 8124
NU
Not used
Relay output does not operate
OL
Overload
Contact closed when overload is detected.
Operates simultaneously with the overload protection
Bridge overload activates also the overload function in the
relay output from software 2.100.
LoadX
Load limit
Contact closed when the load exceeds the limit “X”, where
the limit is determined by parameter 4-3-3
Operates only according to the measured load of the solo
hoist connected to the unit
OK
Fault- and warming –state supervision
Contact closed in normal operation
Contact blinks when the units shifts to “warning state”
Contact open when the unit shifts to “fault state”
Operates simultaneously with the red LED on the unit
Ready
Fault supervision
Contact closed in normal operation
Contact open when the unit shifts to “fault state”
Operates simultaneously with the red LED on the unit
4-3-1
Rout oper.
TempX
Motor overtemperature
Contact closed when the motor temperature exceeds the
limit “X”, where the limit is determined by parameter 4-3-5
Can only be selected when the motor is equipped with
NTC-type of temperature sensors (see parameter 4-5-1)