Super Systems 9205 Series User Manual
Page 90
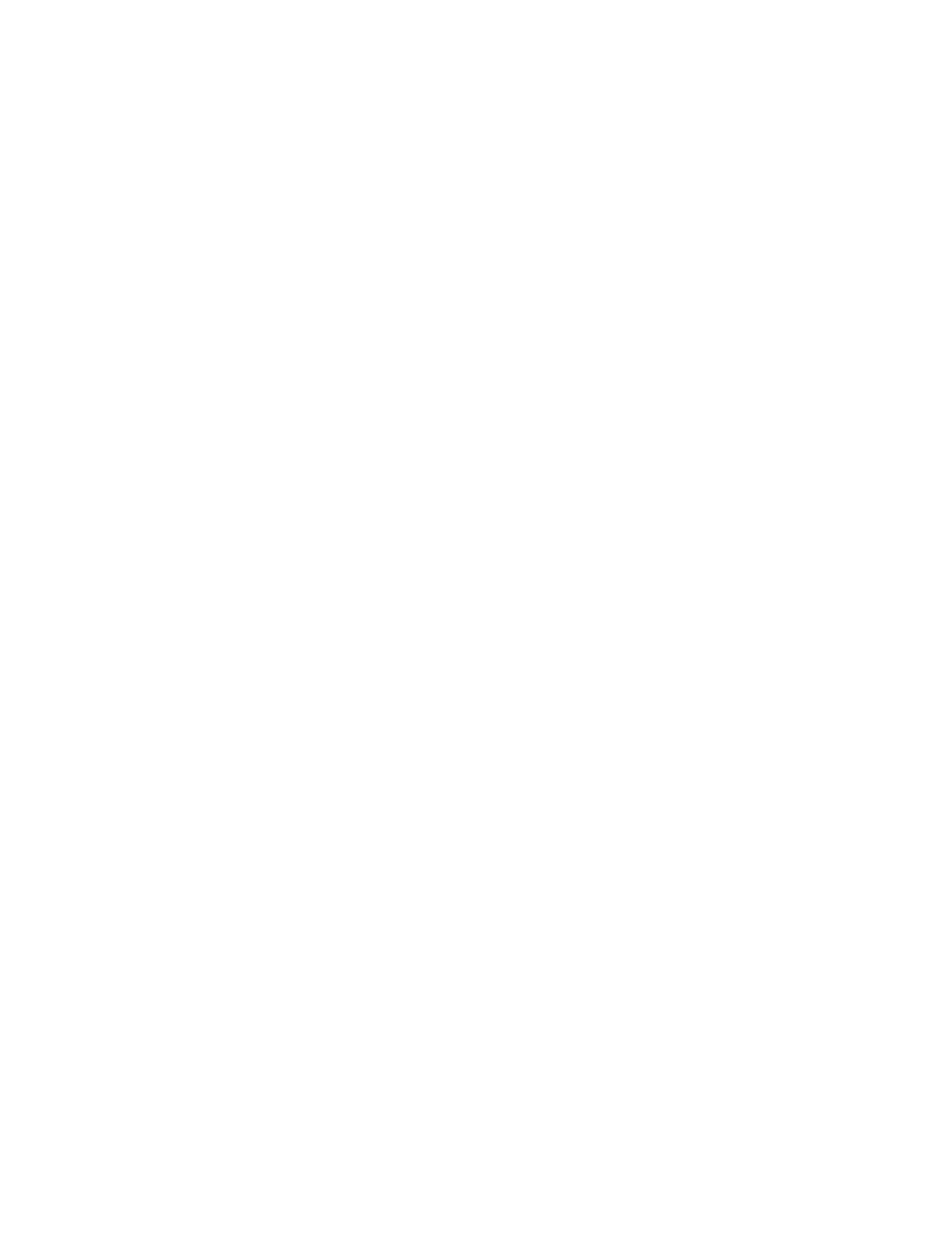
Series 9205 Operations Manual Rev A
89
Then the value for the Negative Output Accumulator after five seconds will be (20.0 + 20.0 + 21.0 + 21.0 +
22.0) or 104.
To reset the Negative Output Accumulator, simply click Edit while the Negative Output Accumulator is
highlighted and confirm the reset. This will cause the Negative Output Accumulator to be reset to zero and
start accumulating values again from that point.
Overshoot Control Logic (No/Yes)
Overshoot control logic is activated when a large setpoint change occurs. If the logic is active and a large
setpoint occurs, it sets a working setpoint at an appropriate distance from the desired setpoint to prevent
the PV from overshooting the desired final setpoint. When the PV reaches or crosses this working setpoint,
then the logic exponentially ramps the working setpoint to the desired final setpoint.
Ramp Detect Logic (No/Yes)
The Ramp Detect logic works in conjunction with the instrument recipe programmer. If the control loop is
the temperature loop for the recipe programmer, and the OPCODE is a ramp, then the control loop does
some special checks. If the Overshoot Control Logic is active, then the final setpoint of the ramp is used to
determine the working setpoint band. However, the ramp setpoint is used until the band is reached. Also,
once the band is reached, if the ramp is faster than the overshoot logic exponential ramp, then the program
is temporarily put on hold as needed to sync the two ramps.
Ramp Level 1 Control (No/Yes) and Ramp Level 2 Control (No/Yes)
Ramp Level 1 and 2 Control are only active if the Ramp Detect logic is active.
Ramp Level 1 Control provides mild overshoot protection during a recipe ramp.
Ramp Level 2 Control is only active if the Ramp Level 1 control is active.
Ramp Level 2 Control provides enhanced overshoot protection during a recipe ramp.
Output rate change limit, %/sec
This option causes the 9205 controller to limit the rate at which the output changes in the furnace. For
example, if the output rate change limit is 5% per second, the controller will increase the output at a rate
no greater than 5% each second until the output reaches the level needed to reach setpoint. This limit can
be useful in cases where (for example) a heating element should not (for operational and safety reasons)
heat up to a high output immediately. If the output needs to reach 100% to achieve setpoint, the Output Rate
Change Limit will apply the output incrementally, rather than allowing the output to climb to 100% as soon
as the heat is turned on.
PID Switch Variable
This is the parameter that triggers the PID switch. The options are Process variable and Setpoint. Note that
PID Auto Switch must be set to Yes in order to use PID Switching.