Auto probe, Trigger method, Auto stop option – Dukane DPC II Plus 9001:2000 User Manual
Page 82: Parameter ( t, And the duration of the burst signal ( t, Untimed auto probe, Timed auto probe, Hold time, Afterburst, Ii plus and ez welder system – user’s manual
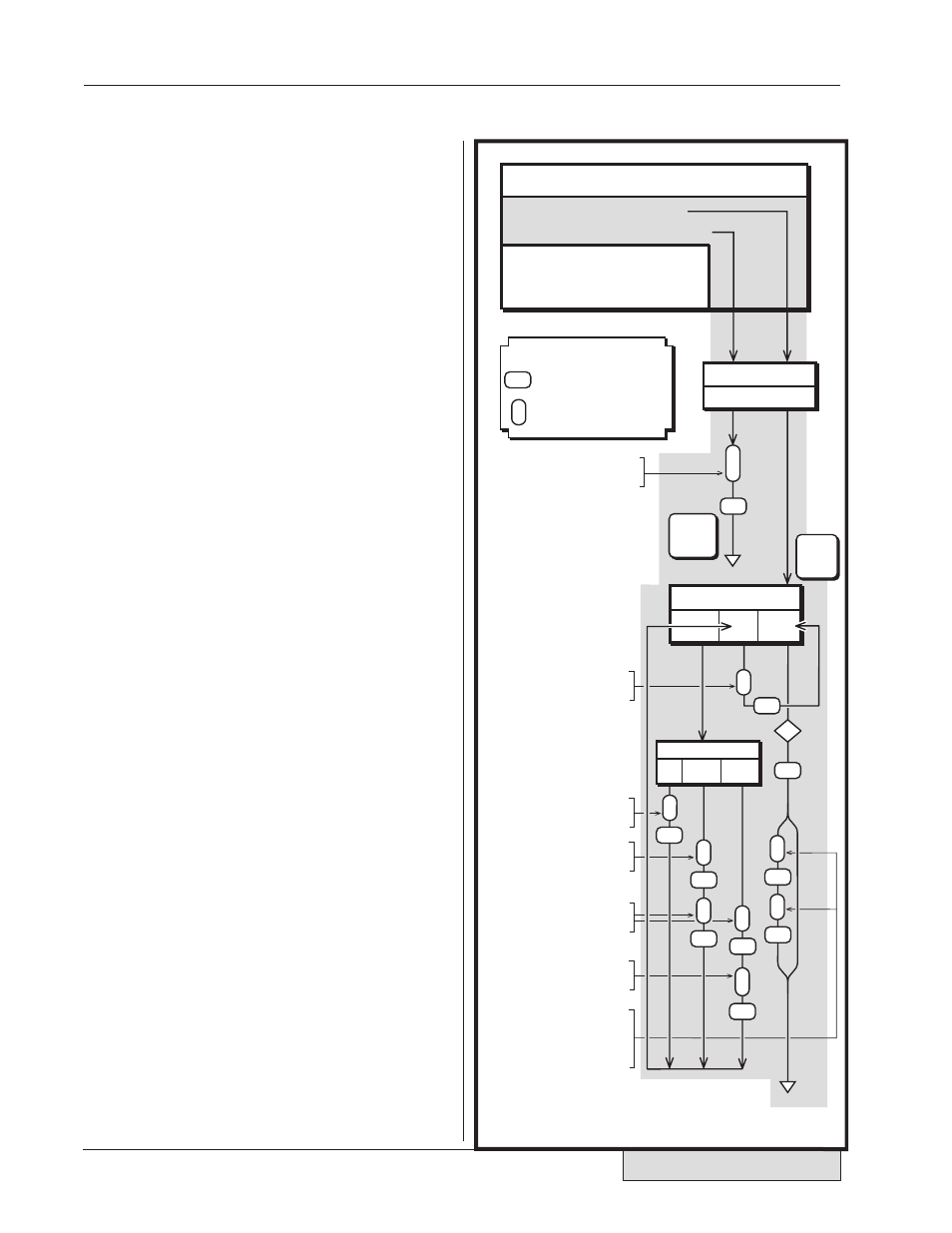
72
Dukane Manual Part No. 403–566–01
DPC
™
II Plus and EZ Welder System – User’s Manual
AUTO Probe
The cable connection diagram for connecting an
automated probe or an automated thruster is shown
in Section 3 in Figures 3–5 and 3–7. The flow chart
for the Process Control menu using Auto Probe is
shown in Figure 7–21. If you do not have a Power
Output module installed, the Energy Weld Method
menu will not be displayed.
The Auto Probe Setup logic adds a Process Con-
trol menu before the Weld Method decision menu.
Compare the flowchart in Figure 7–21 to the pre-
vious MPC flowchart in Figure 7–12. The Pro-
cess Control menu offers two additional settings
to control the welding process. After the normal
Weld Method is programmed, Hold time and
Afterburst settings are available.
1. The
HOLD TIME
parameter (T
hold
) determines
the length of time the probe is held in contact
with the parts after the welding cycle has
stopped. Holding permits the material to so-
lidify under pressure before the head retracts.
2. In some applications, the material being
welded can stick to the horn as it retracts. A
short burst of ultrasonic energy called
AFTERBURST
prevents this. This operation is
defined by two values. The delay after the start
of the upstroke before the burst starts (T
delay
)
and the duration of the burst signal (T
burst
).
The maximum value of both of these param-
eters is 0.999 second.
AUTO STOP Option
The Auto Stop option is shown in Figure 7–13. It is
designed for use with automation equipment and is
available in both the Timed and Untimed Auto Probe
Trigger Method. To use this option, move the SH704
jumper block to JU715 (see Figure 5–12). If Auto
Stop is enabled, then a stop signal on pin 9 of the
HD–15 SYSTEM IN connector will be recognized.
This permits external automation equipment to stop
the welding cycle. If Auto Stop is set to disable,
then a signal on pin 9 will be ignored.
T
we
ld
RTW = Ready To Weld
LEGEND
= Front Panel ENTER Key
(Section 4.3 – Menu Keys)
ENTER
= Parameter Value Entry
T = Time
E = Energy
WELD
METHOD
HOLD
TIME
PROCESS CONTROL
AFTER–
BURST
RTW
RTW
TIMED
AUTO
PROBE
UNTIMED
AUTO
PROBE
Step 1
Step 2
Step 3
WELD METHOD
TIME ENERGY
GND.
DETECT
UNTIMED AUTO PROBE
TRIGGER METHOD
TIMED AUTO PROBE
ENABLE or DISABLE
AUTO STOP
ENTER
ENTER
ENTER
ENTER
ENTER
ENTER
ENTER
ENTER
ENTER
T
dela
y
T
hold
T
dela
y
T
bu
rs
t
T
we
ld
E
we
ld
T
max
T
max
T
scrub
E/D
ENTER
Enable/
Disable
Maximum
E
weld
Minimum
E
weld
= 12,000 Joules
= 1 Joule*
Maximum
T
max
Minimum
T
max
= 30.000 Seconds
= 0.001 Second*
Maximum
T
weld
Minimum
T
weld
= 30.000 Seconds
= 0.001 Second*
Maximum
T
hold
Minimum
T
hold
= 30.000 Seconds
= 0.001 Second*
Maximum
T
delay
Minimum
T
delay
= 30.000 Seconds
= 0.000 Second
Maximum
T
delay
Minimum
T
delay
= 0.999 Second
= 0.000 Second
Maximum
T
burst
Minimum
T
burst
= 0.999 Second
= 0.001 Second*
Maximum
T
scrub
Minimum
T
scrub
= 0.150 Seconds
= 0.001 Second*
* These values can be set to zero, but will not produce any
output. The values listed represent the resolution and are
the smallest values that will produce any output signal.
Figure 7–21
Auto Probe Setup Flow Chart