Sensorless vector – Rockwell Automation 20B PowerFlex 70, PowerFlex 700 Reference Manual User Manual
Page 202
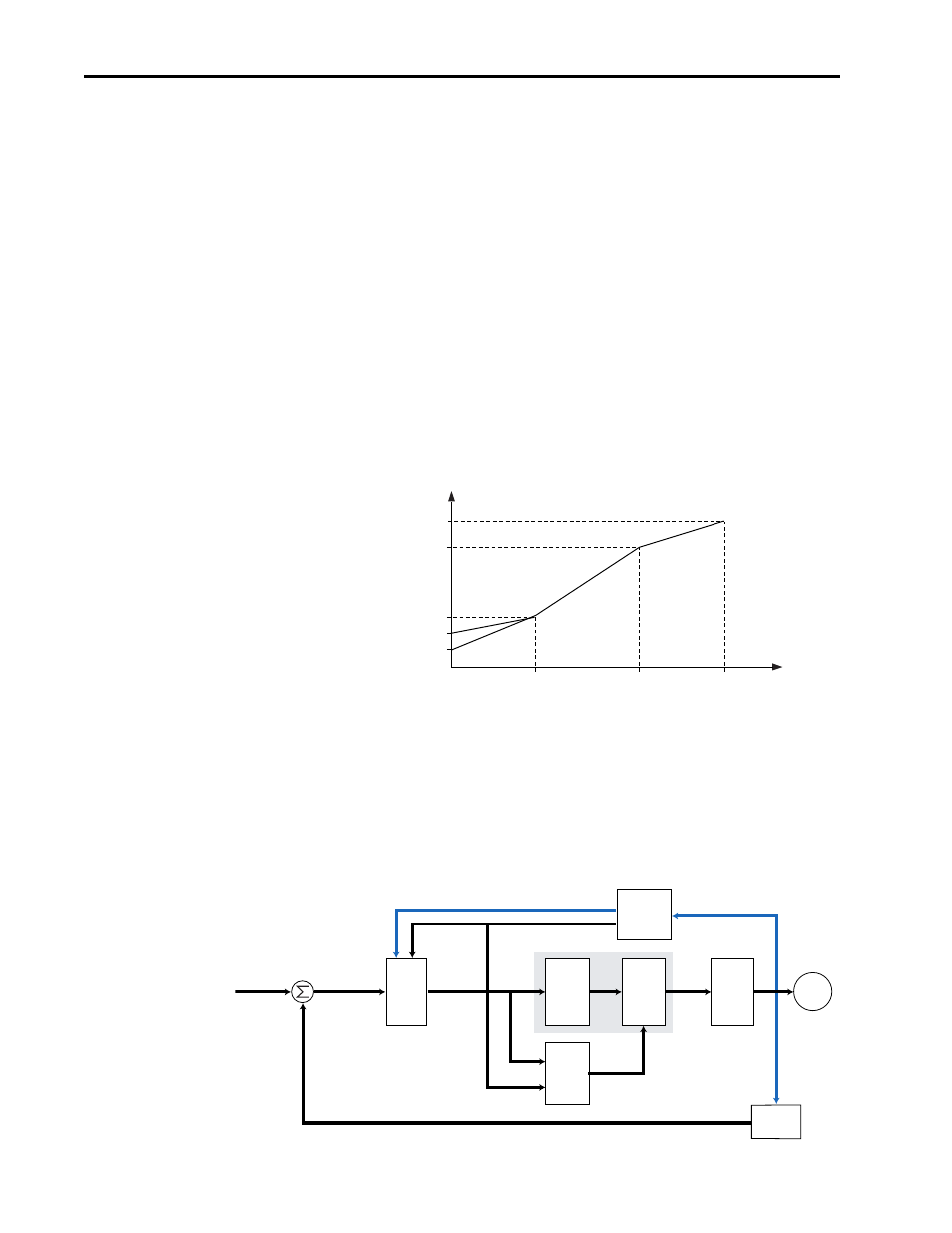
Torque Performance Modes
202
Rockwell Automation Publication PFLEX-RM001H-EN-P - June 2013
were started across the line. As seen in the diagram below, the volts/hertz ratio
can be changed to provide increased torque performance when required. The
shaping takes place by programming 5 distinct points on the curve:
– Start Boost - Used to create additional torque for breakaway from zero
speed and acceleration of heavy loads at lower speeds
– Run Boost - Used to create additional running torque at low speeds. The
value is typically less than the required acceleration torque. The drive will
lower the boost voltage to this level when running at low speeds (not
accelerating). This reduces excess motor heating that could be caused if the
higher start / accel boost level were used.
– Break Voltage/Frequency - Used to increase the slope of the lower
portion of the Volts / hertz curve, providing additional torque.
– Motor Nameplate Voltage/Frequency - sets the upper portion of the
curve to match the motor design. Marks the beginning of the constant
horsepower region
– Maximum Voltage/Frequency - Slopes that portion of the curve used
above base speed.
Sensorless Vector
Sensorless Vector technology consists of a basic V/Hz core surrounded by
excellent current resolution (the ability to differentiate flux producing current
from torque producing current), a slip estimator, a high performance current
limiter (or regulator) and the vector algorithms.
Maximum Voltage
Maximum
Frequency
Base Voltage
(Nameplate) Voltage
Base Frequency
(Nameplate)
Break
Frequency
Run Boost
Start/Accel Boost
Break Voltage
Flux
Vector
Control
Slip
Estimator
V/Hz Control
CURRENT FEEDBACK - TOTAL
CURRENT FEEDBACK
TORQUE I EST.
T
ORQ
UE I EST
.
TORQUE I EST.
V VECTOR
SPEED REF.
FREQUENCY REF.
SLIP FREQUENCY
ELEC. FREQ.
V REF.
GATE
SIGNALS
Current
Resolver
+
+
Current
Limit
V/Hz
Voltage
Control
Inverter
Motor