Remote i/o checklist, Redundancy module checklist, Remote i/o checklist redundancy module checklist – Rockwell Automation 1756-RMxx ControlLogix Enhanced Redundancy System User Manual User Manual
Page 278
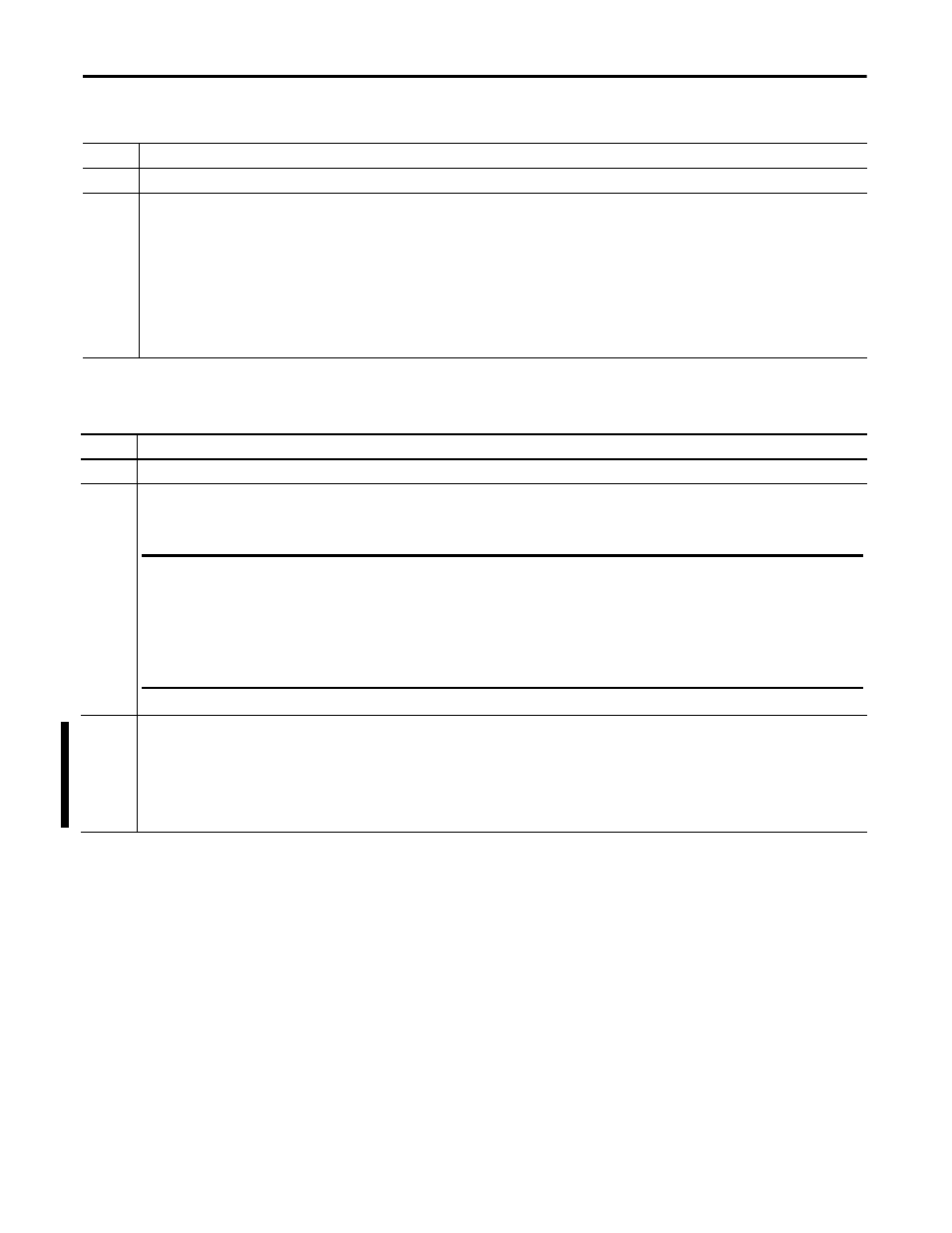
278
Rockwell Automation Publication 1756-UM535D-EN-P - November 2012
Appendix F
Enhanced Redundancy System Checklists
Remote I/O Checklist
Redundancy Module Checklist
Requirement
I/O is not placed in redundant chassis.
I/O is connected to the redundant chassis by using one of these networking options:
• ControlNet connections to the same ControlNet network as the redundant controller chassis, without bridging.
• EtherNet/IP connections to the same EtherNet/IP network as the redundant controller chassis, without bridging. If in the I/O tree of the redundancy controller, all I/O
and consumed tag connections must be multicast connections. The I/O tree of the redundancy controller may contain produced unicast tags consumed by remote
users.
• A DeviceNet network connected through a 1756-DNB DeviceNet communication module in a remote, that is, nonredundant, chassis.
• A universal remote I/O or Data Highway Plus network connected through the use of a 1756-DHRIO module in a remote (nonredundant) chassis.
Requirement
One redundancy module is placed in the same slot of each redundant chassis.
Series A and B redundancy modules are fully compatible. Therefore, you can use any combination of them in a partnered set, for example, a 1756-RM/A module in the
primary chassis and a 1756-RM/B module in the secondary chassis. However, the best scan performance occurs when two Series B redundancy modules are used with
1756-L7x controllers.
A fiber-optic cable connects the redundancy modules in the redundant chassis pair. These are catalog numbers of fiber-optic cable you can order from Rockwell
Automation:
• 1756-RMC1 (1 m, 3.28 ft)
• 1756-RMC3 (3 m, 9.84 ft)
• 1756-RMC10 (10 m, 32.81 ft)
If necessary, you can make your own fiber-optic cable that is up to 4 km (13,123.36 ft) for the 1756-RM/B module or 10 km (32,808.40 ft) for the 1756-RM2 module.
IMPORTANT
The scan time is slightly extended when you downgrade a Series B redundancy module to a Series A module in conjunction with a 1756-L7x
controller in the redundant chassis pair. In this case, raise the task watchdog limits by a factor of ~2x before downgrading. Thereafter, you can re-
tune the limits based on the updated scan time numbers.
If your application uses 1756-L6x controllers in the redundant chassis pair, using a combination of Series A and Series B redundancy modules
results in the same performance as if you use only a Series A redundancy module in the redundancy chassis pair, regardless of the primary or
secondary redundancy state.