2 tachometer troubleshooting – Pulsafeeder Pulsar DLC User Manual
Page 95
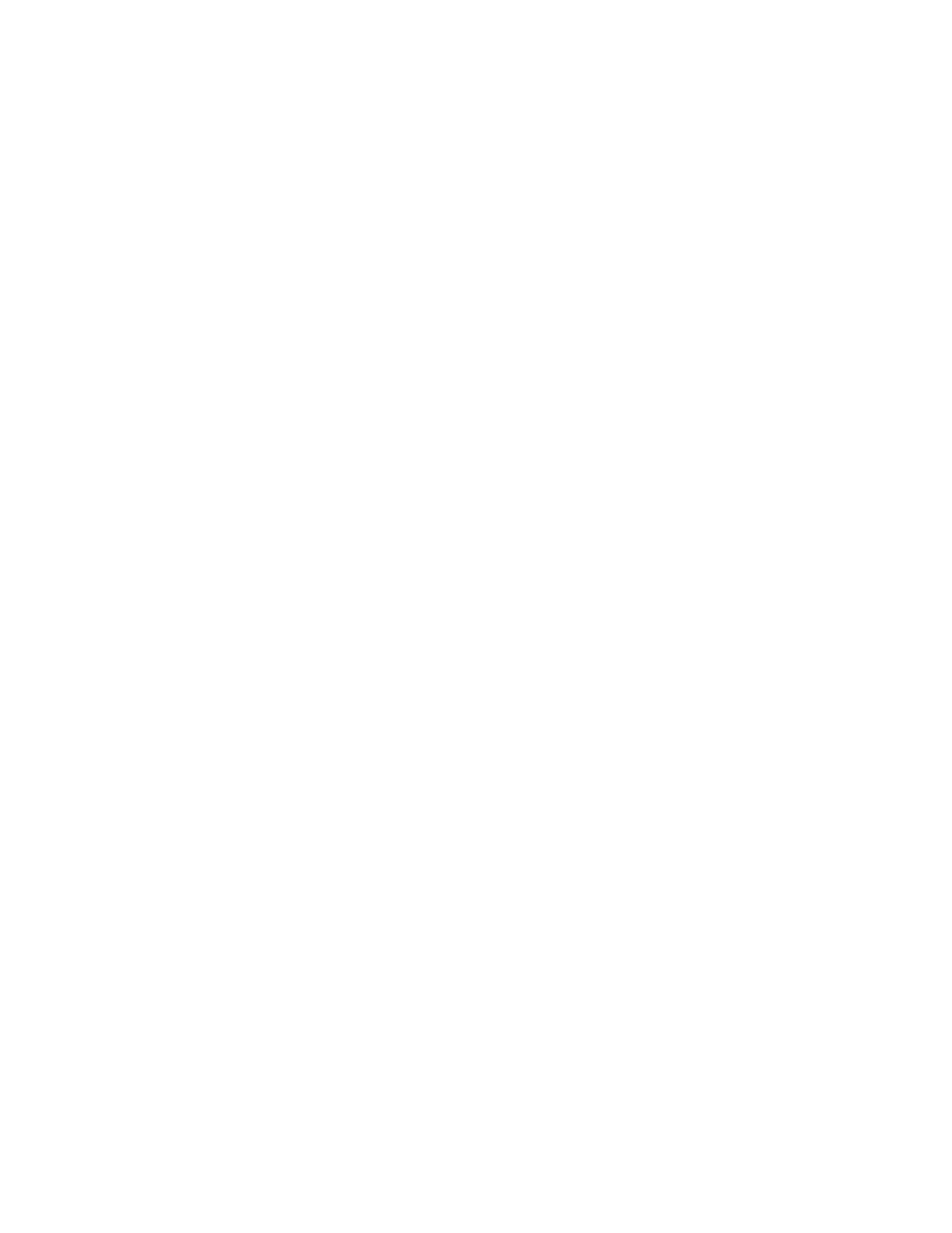
90
11.1.2 Tachometer Troubleshooting
The DLC may utilize a tachometer sensor installed in the gear box (optional). This sensor detects the
passage of 24 gear teeth per motor shaft revolution.
Required Tools:
−
Phillips head screw driver
−
Adjustable Wrench
−
Multi-meter
1. Turn off and lock out the power to the DLC at the main panel.
2. Remove the Wiring Access cover (refer to Figure 2: Accessing the Field Wiring Board).
3. Disconnect the motor power from J3 on the Field Wiring Board (refer to Figure 4 – High Voltage
Connections).
4. Assure that the pump will not discharge fluid and will not be subject to back pressure. Take all
necessary precautions.
5. To complete this procedure, you will have to manually rotate the PULSAR drive motor. If the motor
type is TEFC, you can push against the fan blades through the shroud to do this. If the motor type is
TENV, you must remove the protective cap from the end of the motor to access the motor shaft.
6. Turn on the power to the DLC at the main panel.
7. Check the supply voltage to the Tachometer. Set your multi-meter to read DC voltage in the range of
0-100 VDC. Connect the positive lead of the multi-meter to J10-1 (TACH[+]). Connect the negative
lead of the multi-meter to J5-8 (unlabeled, it is actually DC ground). You should read a value of
12.0VDC +/- 1.0VDC. If you do not read this value, stop your test and contact Technical Services.
8. Check the output from the Tachometer. Set your multi-meter to read DC voltage in the range of 0-10
VDC. Connect the positive lead of your multi-meter to J10-2 (TACH[-]) and the negative lead to J5-8
(unlabeled, it is actually DC ground). Slowly rotate the pump motor observing the high and low multi-
meter readings. When the Tachometer is working properly this output will be transition from a value of
approximately 1.0 VDC when a gear tooth is near the end of the sensor to a value above 5.0 VDC when
it is away from it. If these readings are obtained skip to step 17.
9. If these voltage readings are not obtained, adjust the sensor as follows.
10. Remove the conduit from the sensor housing by removing the ‘C’ clip and threading the plastic
coupling from the sensor. Note: the tachometer cord will prevent you from removing the conduit
completely. Refer to Figure 8: Tachometer and Pump Motor Thermostat Connections.
11. Remove the lock nut from the sensor housing and carefully rotate the sensor body clockwise until the
sensor bottoms against the gear, then rotate the sensor body counter clockwise 1/2 turn.
12. Slowly rotate the pump motor until the minimum multi-meter reading is obtained. If the meter does not
exhibit any voltage change either the sensor or the interface circuitry is defective.
13. Slowly rotate the sensor body counter-clockwise a few degrees at a time until the minimum multi-
meter reading is obtained. If this reading is above 1.5 volts either the sensor or the interface circuitry is
defective.
14. Slowly rotate the sensor body clockwise a few degrees at a time until the multi-meter reading rises
slightly (0.01 to 0.05 volts above the minimum obtained above).
15. Replace and tighten the lock nut, while maintaining the voltage reading above by holding the sensor
cable to prevent the sensor from rotating.
Slowly rotate the pump motor observing the high and low multi-meter readings. The output should now
transition from a value below 1.5 VDC when a gear tooth is near the end of the sensor to a value above
5.0 VDC when it is away from it. If the meter reads a low value above 1.5 VDC or a high value below
5.0 VDC either the sensor or the interface circuitry is defective. .
17. If you have already made adjustments to the Tachometer position at this point you may want to skip to
step 20 and test your adjustments.