Pulsafeeder Pulsar DLC User Manual
Page 90
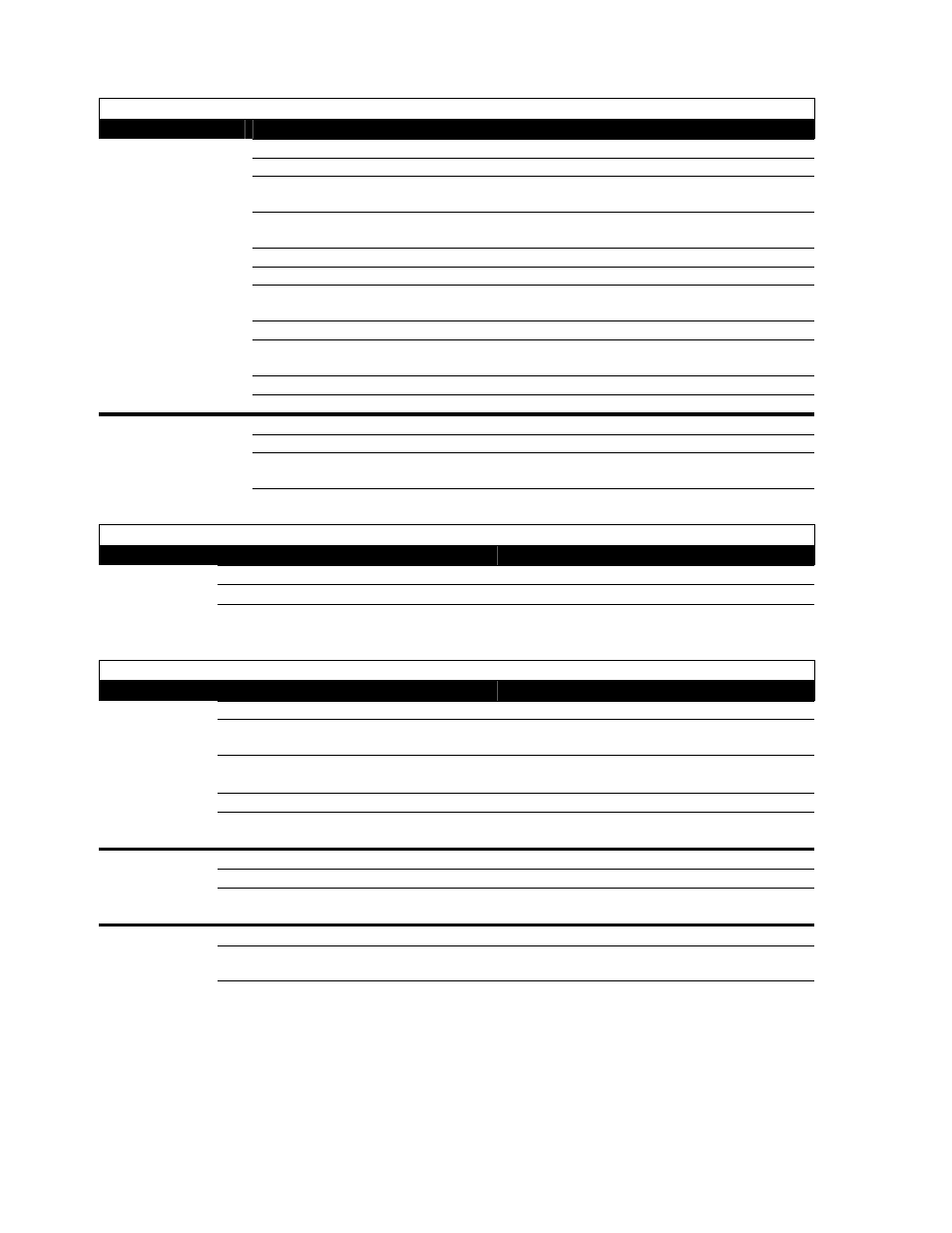
85
PULSAR MOTOR (1-Phase)
Symptom
Probable Cause
Possible Solution
Motor will not start.
No power supplied.
Check power source to DLC.
.
Motor wired incorrectly.
Check wiring.
Supply power outside of
specification.
Check voltage/frequency against name plate.
Motor key not pressed. Keypad
problem.
Press [MOTOR}to start motor. Refer to the
Keypad trouble shooting section.
Remote Motor Switch is off
Turn switch on.
Software did not initiate properly.
Cycle power.
Alarm or Level input set with option
MOTOR OFF? set to YES.
Correct Alarm or Level condition. Set
MOTOR OFF? to NO.
PULSAR mechanicals locked.
Check PULSAR, reference PULSAR IOM.
Motor Thermostat not connected or
programmed.
Connect or program the Motor Thermostat.
Solid-state relay failed.
Contact Technical Services.
MODBUS in control.
Check MODBUS control application
Motor will not stop.
Motor wired incorrectly.
Check wiring.
Software did not initiate properly.
Cycle power.
Motor key not pressed. Keypad
problem.
Press [MOTOR] to stop motor. Refer to the
Keypad trouble shooting section.
Solid-state relay failed.
Contact Technical Services.
ALARM RELAY
Symptom
Probable Cause
Possible Solution
Alarm Relay
Relay wired incorrectly.
Check wiring.
will not
Relay fuse blown.
Replace with
1A@250VAC
fuse.
Activate
Software not configured properly.
Refer to Section 7 – General Operation:
Menu.
ANALOG INPUT
Symptom
Probable Cause
Possible Solution
Input wired incorrectly.
Check wiring.
Input not wired to correct channel.
Refer to Section 5 – Installation: Analog
Input for wiring instructions.
Input fuse(s) blown.
Replace F4 & F5 w/
50mA@250VAC
for
channel #1 and F6 & F7 for Channel #2.
Not in Analog Operation Mode.
Press [MODE] or configure Active.
Not
Responding to
Analog (mA)
Input
Input not calibrated properly.
Review Section 7-General Operation:
Calibration.
Break in wiring.
Check wiring.
Input outside of specification.
Boost/Condition Signal.
Signal Failure
Message
Displayed with
no signal loss
Process fluctuates too rapidly: < 0.3mA
and changing by more than 8.8mA/s
Condition Signal. Change Failure Mode. Re-
calibrate.
Miss-Calibrated.
Re-Calibrate.
0% calibration value mis-interpreted.
The "0% = 4.0mA" calibration screen refers to
0% flow. Not 0% stroke.
Lo Analog
Input point
(e.g., 4.0mA)
does not equate
to 0% unit
reading
Jitters or slow response.
Change Averaging Parameters.