A2.2.2 safety accuracy, A2.2.3 diagnostic response time, A2.2.4 setup – Yokogawa RotaMASS 3-Series User Manual
Page 250: A2.2.5 proof testing
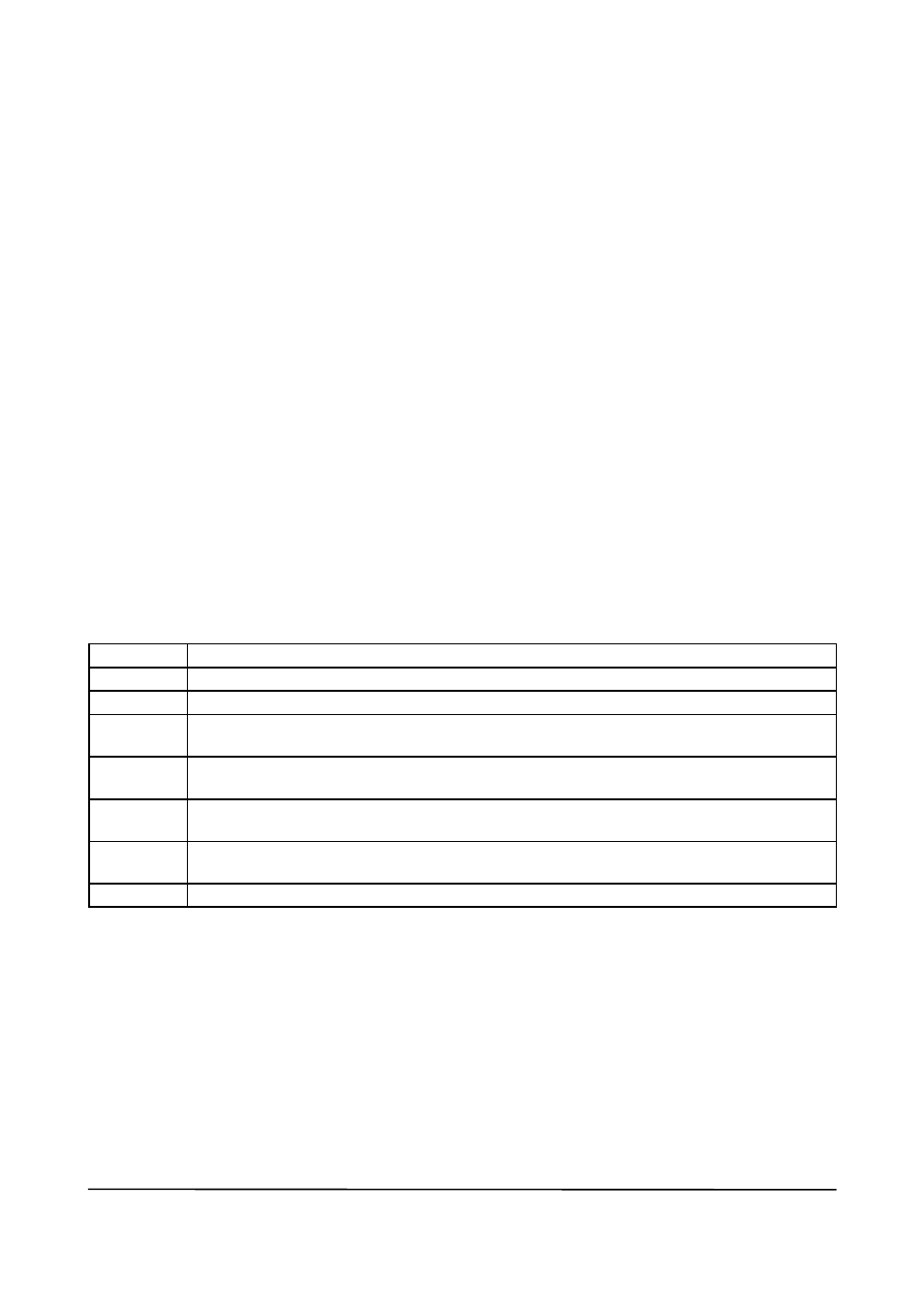
A2 SAFETY INSTrUMENTEd SYSTEMS INSTAllATION
A2-2
IM 01R04B04-00E-E 8th edition March 01, 2011 -00
All Rights Reserved. Copyright © 2003, Rota Yokogawa
A2.2.2 Safety Accuracy
The flowmeter has a specified safety accuracy of 2%. This means that internal component
failures are listed in the device failure rate if they will cause an error of 2% or greater.
A2.2.3 diagnostic response Time
The flowmeter will report an internal failure within 3 minutes of fault occurrence for amplitude errors and
within 1 second of fault occurrence for all other errors (e. g. frequency error, signal fault).
A2.2.4 Setup
During installation the flowmeter must be setup with engineering unit parameters. This is typically done
with a handheld device. These parameters must be verified during the installation to insure that the correct
parameters are in the flowmeter. Engineering range parameters can be verified by reading these parameters
from the optional local display or by checking actual calibration of the flowmeter.
Calibration of the flowmeter must be done after parameters are set.
A2.2.5 proof Testing
The objective of proof testing is to detect failures within the flowmeter that are not detected by the
diagnostics of the flowmeter. Of main concern are undetected failures that prevent the safety instrumented
function from performing its intended function. The frequency of the proof tests (or the proof test interval) is
to be determined in the reliability calculations for the safety instrumented functions for which the flowmeter
is applied. The actual proof tests must be performed more frequently or as frequently as specified in the
calculation in order to maintain required safety integrity of the safety instrumented function. The following
tests need to be specifically executed when a proof test is performed. The results of the proof test need to be
documented and this documentation should be part of a plant safety management system. Failures that are
detected should be reported to Yokogawa.
Step
Action
1.
Bypass the safety function and take appropriate action to avoid a false trip
2.
Verify current output with flow tube filled and zero flow rate within stated accuracy
3.
Verify reasonability of current output with flow tube filled at two different flow rates able
to be independently estimated to approximately 10% accuracy
4.
Use display or digital communications to retrieve process temperature measurement
and verify against independent measurement
5.
Use display or digital communications to retrieve any diagnostics and take appropriate
action.
6.
Use display or digital communications to send the flowmeter to the high and low alarm
level output state current and verify that the analog current reaches these values
1
.
7.
Remove the bypass and otherwise restore normal operation
1
This tests low loop voltage and high loop impedance related failures.
When all the tests listed above are executed a proof test coverage of 71.8% can be claimed.
This proof test in combination with automatic diagnostics will detect 94% of possible DU failures.
The following tools need to be available to perform proof testing.
- Flowmeter display or alternatively for digital communication: HART Handheld, PRM or FieldMate
- Measurement instrument to verify output current
- Reference temperature measurement as close as possible to the meter under test.
The person(s) performing the proof test of the Yokogawa ROTAMASS 3 Series Coriolis Mass Flow and
Density Meter should be trained in SIS operations including bypass procedures, flowmeter maintenance and
company management of change procedures.