3 alarms, causes and actions – IAI America PCON-PO User Manual
Page 89
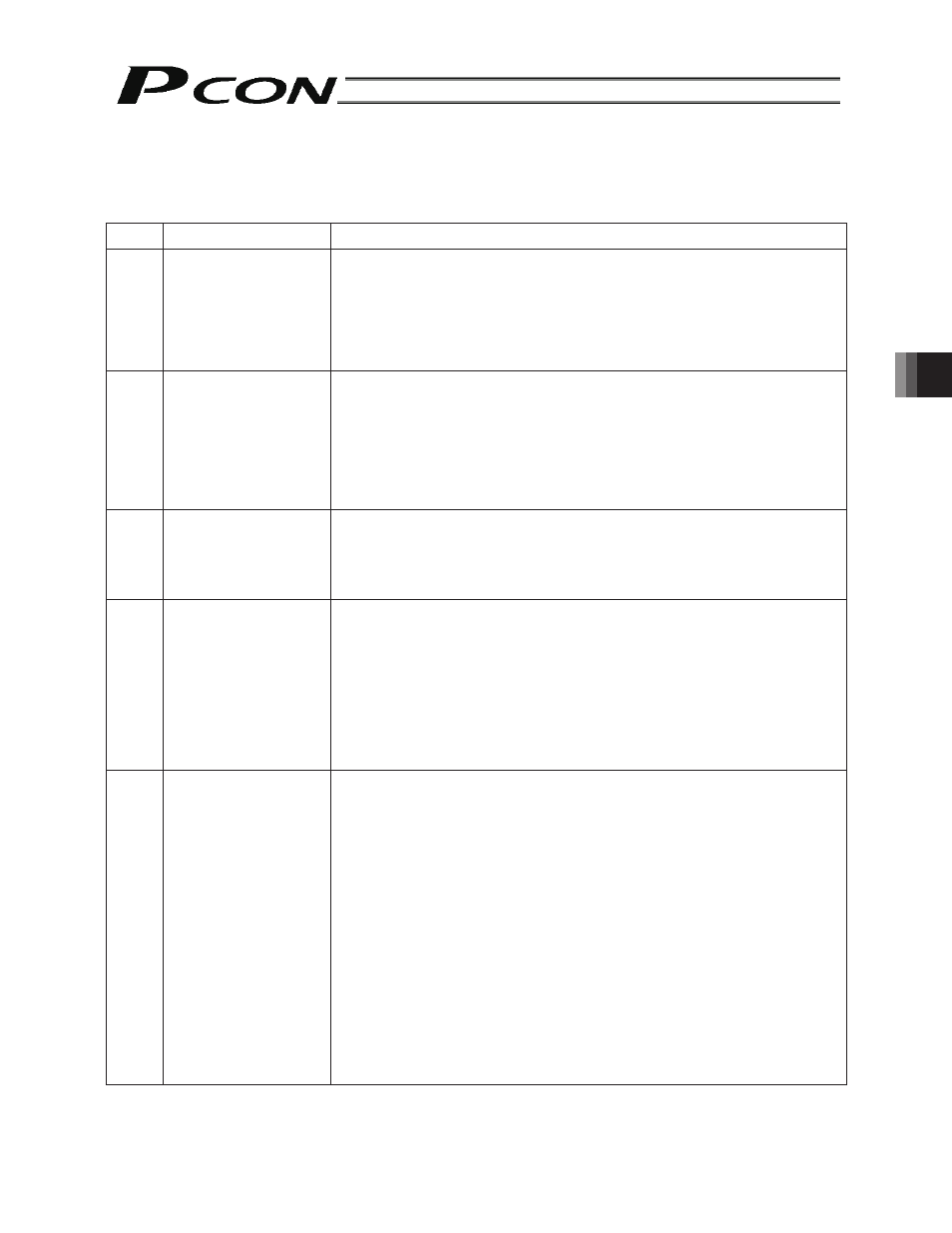
77
6. T
roubleshooting
6.3
Alarms, Causes and Actions
(1) Operation Cancellation Alarms
Code
n
o
i
t
c
a
/
e
s
u
a
C
r
o
r
r
E
0A1
Parameter data error
Cause:
The parameter data does not meet the specified input range.
(Example)
This alarm generates when a pair of values clearly has an
inappropriate magnitude relationship, such as when the soft
limit + setting is 200.3 mm, while the soft limit – setting is
300 mm.
Action:
Change the settings to appropriate values.
0BA
Home sensor not yet
detected
This alarm indicates that the actuator equipped with a home check sensor did not
complete homing successfully.
Cause:
[1] The work contacted peripheral equipment during the homing.
[2] The slide resistance of the actuator is large in some areas.
[3] The home check sensor is not installed properly, or the sensor is
faulty or its circuit is open.
Action:
If the work is not contacting any peripheral equipment, [2] and [3] are
suspected. Contact IAI.
0BE
Homing timeout
Cause:
After the start of homing, homing does not complete after elapse of the
time set by the manufacturer’ s parameter. (This alarm does not
generate during normal operation.)
Action:
As one possible cause, the controller and actuator combination may be
incorrect. Contact IAI.
0C0
Excessive actual speed
Cause:
The motor speed exceeds the maximum speed set by the
manufacturer’ s parameter.
This alarm does not generate during normal operation, but it may occur
if the load decreased before a servo error was detected and the motor
speed has increased as a result. This condition occurs due to the
following reasons:
[1] The slide resistance of the actuator is large in some areas.
[2] The load increased due to momentary application of external force.
Action:
Check the assembly condition of mechanical parts for any abnormality.
If the actuator itself is suspected as the cause, contact IAI.
0C1
Servo error
This alarm indicates that after the acceptance of the move command, the motor
could not operate for 2 seconds or more before the actuator reached the target
position.
Cause:
[1] The connector of the motor relay cable is loose or its circuit is open.
[2] If the actuator is equipped with a brake, the brake cannot be
released.
[3] The load increased due to application of external force.
he actuator itself is high.
Action:
[1] Check the wiring condition of the motor relay cable.
[2] Check the wiring condition of the brake cable, and also turn on/off
the brake release switch to check if “click” sound is heard.
[3] Check the assembly condition of mechanical parts for any
abnormality.
[4] If the load is normal, cut off the power and move the actuator by
hand to check the slide resistance.
ted as the cause, contact IAI.
[4] The sliding resistance of t
[5] The positioning band setting is smaller than the encoder resolution.
[5] Set the positioning band value greater than that of the encoder
If the actuator itself is suspec
resolution.