Toshiba – Toshiba Adjustable Speed Drive H3 User Manual
Page 106
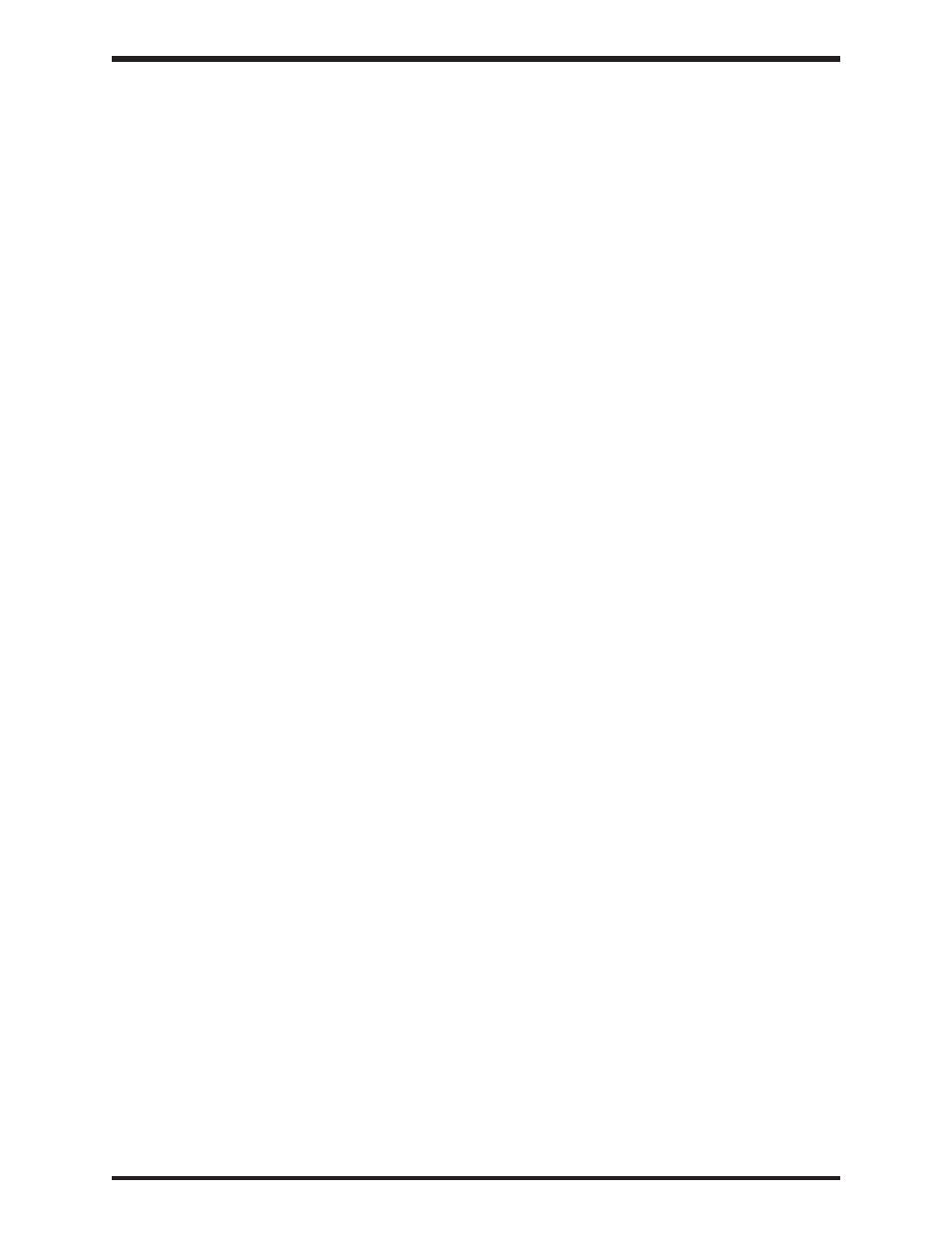
TOSHIBA
10 - 6
Drive Fault Displays and Explanations (cont'd)
OPTION PCB ERROR
Comments:
If drive is energized with an option board installed and is later energized without the
board installed, this fault will appear. Check connectors between control board and option board.
Check settings of Item 80,
FREQUENCY PRIORITY SELECTION #1
, Item 81,
FREQUENCY
PRIORITY SELECTION #2
, and Item 264,
COMMUNICATION SELECTION
. Use stand-offs to
secure board.
LOW CURRENT TRIP
Cause:
The drive's output current went below the current value entered in Item 167,
LOW
CURRENT DETECT LEVEL
for at least the amount of time entered in Item 168,
LOW
CURRENT DETECTION TIME
.
UNDERVOLTAGE TRIP
Cause:
The drive's DC bus voltage went below 217 VDC (230 V G3), 413 VDC (460 V G3), or
594 VDC (600 V G3) for at least the time entered in Item 165,
UNDERVOLTAGE DETECT TIME
.
Comments: Item 164,
UNDERVOLTAGE TRIP SELECTION
turns the ability to undervoltage trip
on/off. On G3 models 2080-2110 and 4080-4270, turning on Item 155,
REGENERATION POWER
RIDE-THROUGH
and adjusting Item 156,
REGENERATION RIDE-THROUGH TIME
may keep bus
up during brown out if there is sufficient regen energy from the load.
OVERTORQUE TRIP
Cause:
The drive's torque current went above the current value programmed in Item 171,
OVERTORQUE TRIP LEVEL
. The G3 can be programmed to torque current limit; contact your
Toshiba distributor and request the torque limit application guideline.
EARTH FAULT (SOFT) or EARTH FAULT (HARD)
Cause:
Drive detected some current to ground. Depending on rating, drive senses ground fault via
ZCT (hard fault) or HCT (soft fault).
Comments: With leads disconnected from drive, meg motor and leads. Look for any moisture that
may provide current path to ground. Make sure that control wiring is separated from power wiring.
Adding noise supressors on coils of starters on same line as drive may snub noise picked up by
ZCT. RF/EMI filter may help remove noise generated by SCR rectifiers in the vicinity. Make sure
drive chassis and motor are grounded.
AUTO-TUNING ERROR
Cause:
Motor's physical characteristics are not within the window of allowable values for modeling.
Comments: Try a different inertia setting in Item 323,
LOAD MOMENT OF INERTIA
. Motor must
be at rest to perform auto-tuning. Motor must be one HP size within the drive's HP size.
Auto-tuning is best done with motor at full-load temperature (if temperature is very cold, auto-tune
error may appear).
GATE ARRAY FAULT
Comments: Replace control board.
CURRENT DETECT ERROR
Comments:
Occurs when drive is stopped but CPU detects current flowing. This fault could be
caused by plugging in RS232 cable with drive powered (resulting in damage to control board).
Adding a RF/EMI filter may remove noise spikes from nearby SCR rectifiers. If the control board
is damaged, the drive must be serviced.
INV TYPEFORM ERROR
Cause:
Control board is not configured to drive's rating.
Comments: Enter "7" into Item 280,
STANDARD SETTING MODE SELECTION
.