Toshiba – Toshiba Adjustable Speed Drive H3 User Manual
Page 104
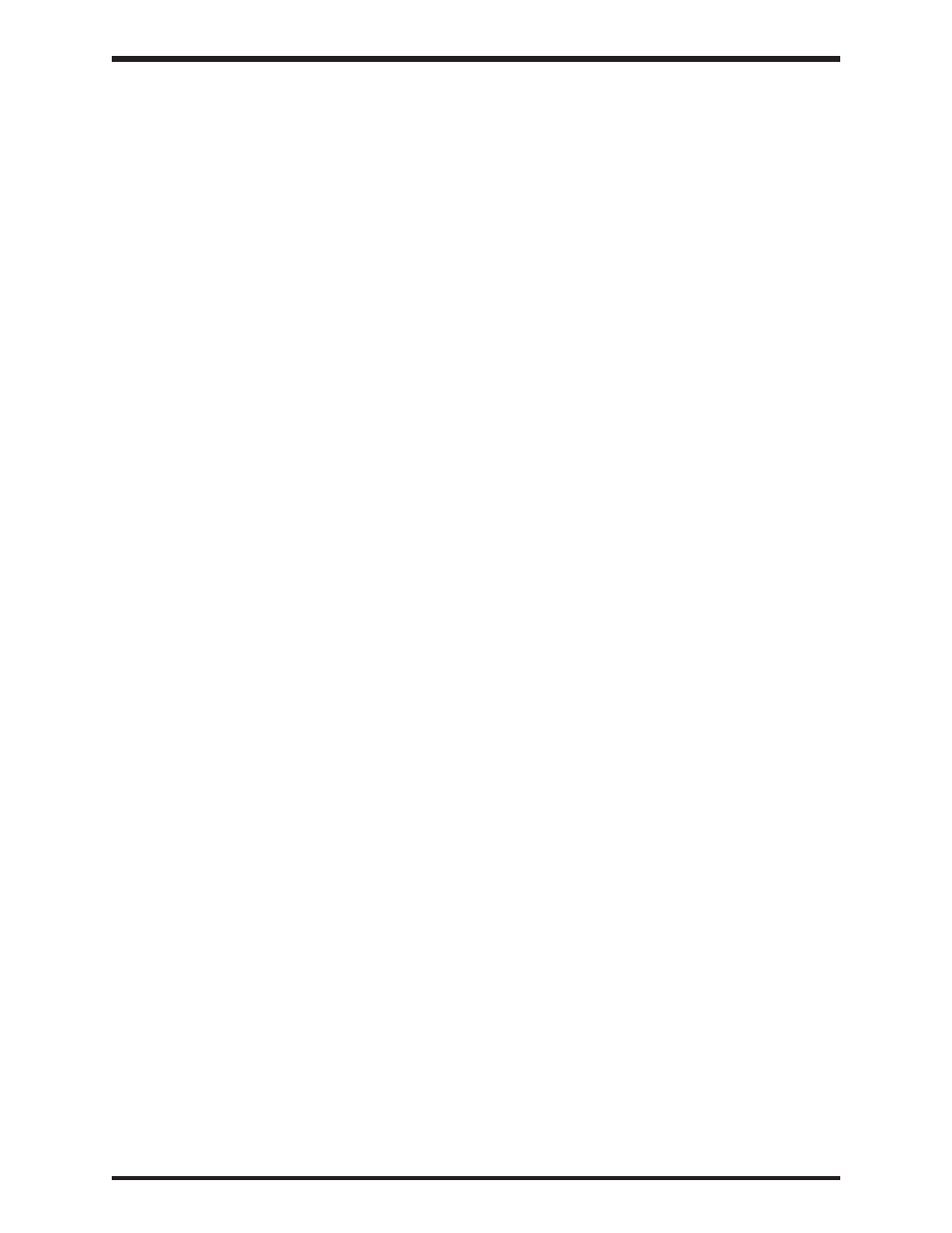
TOSHIBA
10 - 4
Drive Fault Displays and Explanations (cont'd)
U-PHASE SHORT-CIRCUIT
or
V PHASE SHORT-CIRCUIT
or
W PHASE SHORT-CIRCUIT
Cause: Drive detected short-circuit in transistor.
Comments:
Replace transistor. Contact your Toshiba distributor for authorized repair.
LOAD-END OVERCURRENT
Cause: Drive detected short-circuit on output.
Comments:
Check for phase-phase short.
Meg motor/leads with leads disconnected from
drive. Remove any power factor correction caps on motor. See Item 169,
OUTPUT SHORT-
CIRCUIT DETECTION SELECT
.
OVERVOLTAGE (ACCEL)
or
OVERVOLTAGE (RUN)
Cause: Bus exceeded 393 VDC (230 volt drive),or 787 VDC (460 volt drive).
Comments:
Incoming AC may have gone high or spiked (verify with Item 289,290, 291, or 292
set to "16"); a line reactor or a lower tap on transformer may help. Motor may be mechanically
forced to run faster than drive is commanding; install appropriate dynamic braking resistor (see
page 9-16). On eccentric cyclic loads like presses or pump jacks, contact your Toshiba distributor
for special programming instructions that may make a DBR unnecessary.
OVERVOLTAGE (DEC)
Cause: Bus exceeded 393 VDC (230 volt drive),or 787 VDC (460 volt drive).
Comments:
Incoming AC may have gone high or spiked (verify with Item 289 set to "16"); a line
reactor or a lower tap on transformer may help. Item 11,
DECELERATION TIME #1
may be too
short. Drive will automatically change decel time with Item 12,
ACC/DEC PATTERN ADJUST
LOW
set to "1". Make sure Item 145,
OVERVOLTAGE STALL PROTECTION
is set to "0". Motor
may be mechanically forced to run faster than drive is commanding (due to large load inertias
mechanical couplings); install appropriate dynamic braking resistor (see page 9-16). On eccentric
cyclic loads like presses or pump jacks, contact your Toshiba distributor for special programming
instructions that may make a DBR unnecessary.
INVERTER OVERLOAD
Cause: Drive exceeded 110% of its rated current for too long of a time.
Comments:
This trip indicates that the drive output exceeded its rated current for specific
amounts of time. For example, 100 HP and smaller drives can output 150% of their rated current
for 120 seconds, 130% for 240 seconds, 170% for 3.5 seconds, and 185% for 0.5 seconds.
If using DC Injection, Item 147,
DC INJECTION CURRENT MAGNITUDE
or Item 148
DC
INJECTION TIME
they may be too large. If Item 42,
PWM CARRIER FREQUENCY
is greater than
8 KHz, try carrier frequencies less than 8 KHz. Programming Item 161,
OVERLOAD SELECTION
to "1" or "3" (soft stall on) makes the drive reduce output frequency/voltage to shed load (works
best on variable torque applications).
Motor or load bearings may have seized. Enabling True
Torque Control (see page 9-31) may reduce drive's current output and solve the problem. Make
sure that drive is seeing voltage on all three of its input phases. Drive may be undersized.
MOTOR OVERLOAD
Cause:
Motor is in danger of overheating because it drew too much current for too long of a time,
as determined by the drive.
Comments:
See page 9-17. Check Items 158, 159, 160, and 161. If trip occurred at a low
frequency, the setting of Item 159,
OVERLOAD REDUCTION START FREQUENCY
is probably
critical. Motor overload protection can be turned off by placing a "2" or "3" in Item 161. Check
value in Item 160,
MOTOR 150% OVERLOAD TIME LIMIT
.