9 bore milling (cycle 208), Cycle run, Please note while programming – HEIDENHAIN TNC 320 (34055x-06) Cycle programming User Manual
Page 79: Bore milling (cycle 208)
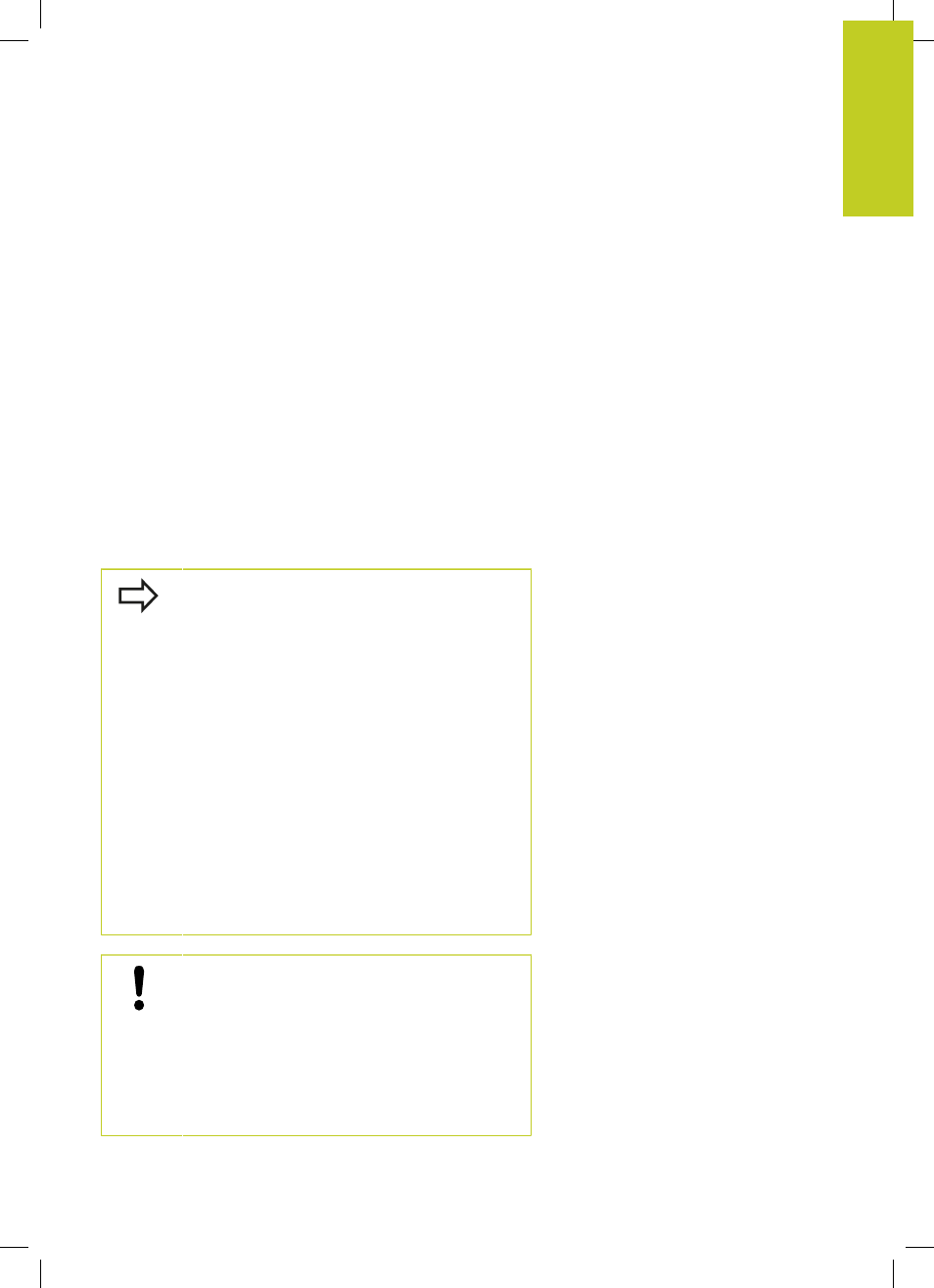
BORE MILLING (Cycle 208)
3.9
3
TNC 320 | User's Manual Cycle Programming | 5/2013
79
3.9
BORE MILLING (Cycle 208)
Cycle run
1 The TNC positions the tool in the tool axis at rapid traverse
FMAX to the programmed set-up clearance above the workpiece
surface and then moves the tool to the bore hole circumference
on a rounded arc (if enough space is available).
2 The tool mills in a helix from the current position to the first
plunging depth at the programmed feed rate
F.
3 When the drilling depth is reached, the TNC once again
traverses a full circle to remove the material remaining after the
initial plunge.
4 The TNC then positions the tool at the center of the hole again.
5 Finally the TNC returns to the setup clearance at
FMAX. If
programmed, the tool moves to the 2nd set-up clearance at
FMAX.
Please note while programming:
Program a positioning block for the starting point
(hole center) in the working plane with radius
compensation
R0.
The algebraic sign for the cycle parameter DEPTH
determines the working direction. If you program
DEPTH=0, the cycle will not be executed.
If you have entered the bore hole diameter to be
the same as the tool diameter, the TNC will bore
directly to the entered depth without any helical
interpolation.
An active mirror function
does not
influence the type
of milling defined in the cycle.
Note that if the infeed distance is too large, the tool
or the workpiece may be damaged.
To prevent the infeeds from being too large, enter
the maximum plunge angle of the tool in the
ANGLE
column of the tool table. The TNC then automatically
calculates the max. infeed permitted and changes
your entered value accordingly.
Danger of collision!
Use the machine parameter displayDepthErr to
define whether, if a positive depth is entered, the
TNC should output an error message (on) or not (off).
Keep in mind that the TNC reverses the calculation
for pre-positioning when a
positive depth is
entered
. This means that the tool moves at rapid
traverse in the tool axis to set-up clearance
below
the workpiece surface!