Setting machine parameters, Fundamentals 18.1 – HEIDENHAIN TNC 320 (34055x-06) Cycle programming User Manual
Page 385
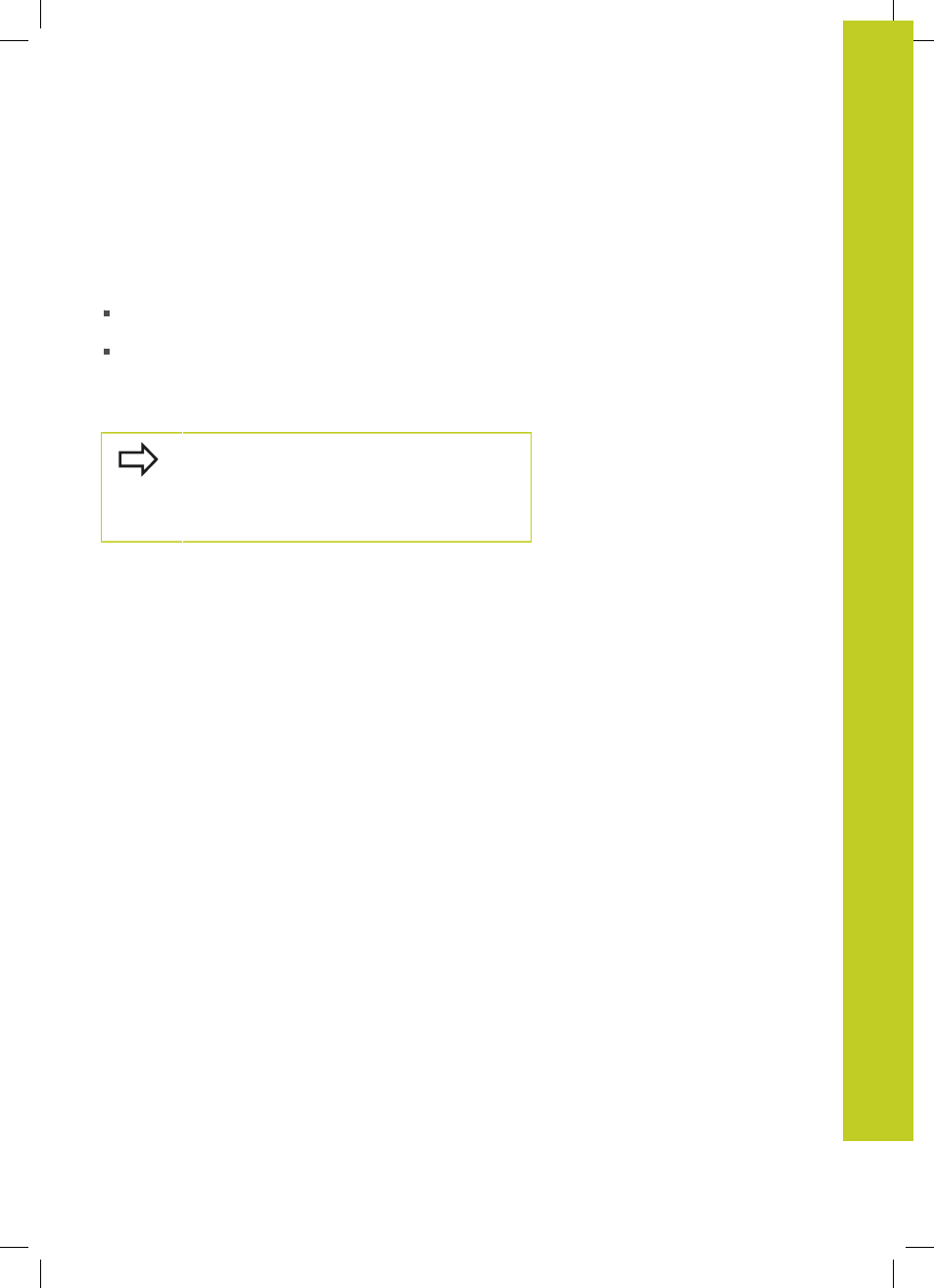
Fundamentals 18.1
18
TNC 320 | User's Manual Cycle Programming | 5/2013
385
Differences between Cycles 31 to 33 and Cycles 481 to
483
The features and the operating sequences are absolutely identical.
There are only two differences between Cycles 31 to 33 and Cycles
481 to 483:
Cycles 481 to 483 are also available in controls for ISO
programming under G481 to G483.
Instead of a selectable parameter for the status of the
measurement, the new cycles use the fixed parameter
Q199.
Setting machine parameters
Before you start work with the TT cycles, inspect
all machine parameters defined in
ProbeSettings >
CfgToolMeasurement and CfgTTRoundStylus.
The TNC uses the feed rate for probing defined in
probingFeed when measuring a tool at standstill.
When measuring a rotating tool, the TNC automatically calculates
the spindle speed and feed rate for probing.
The spindle speed is calculated as follows:
n =
maxPeriphSpeedMeas / ( r • 0.0063) where
n:
Spindle speed [rpm]
maxPeriphSpeedMeas:
Maximum permissible cutting speed in
m/min
r:
Active tool radius in mm
The feed rate for probing is calculated from:
v = measuring tolerance • n with
v:
Feed rate for probing in mm/min
Measuring tolerance
Measuring tolerance [mm], depending
on
maxPeriphSpeedMeas
n:
Shaft speed [rpm]