Delta p stabilization, Delta p stabilization 31 – MTS Series 793 User Manual
Page 31
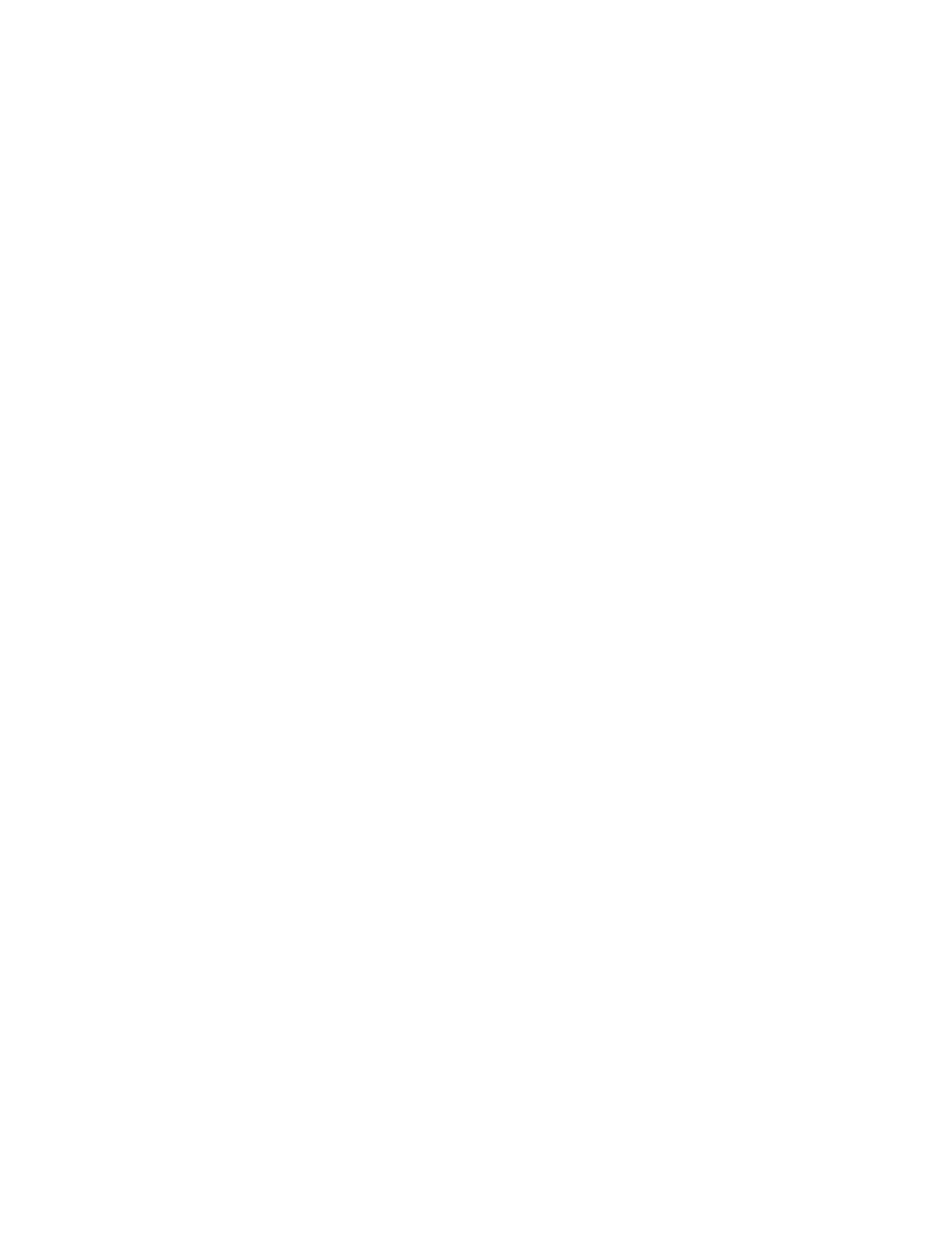
About Tuning
MTS Series 793 Tuning and Calibration
Introduction
31
Delta P Stabilization
Delta P makes use of a differential pressure sensor that measures the difference in
pressure at each end of the actuator. It compensates for hydraulic compliance
(compressed hydraulic fluid acts like a spring). Delta P improves displacement
control of heavy mass loaded systems.
Delta P is typically used on systems with large hydraulic fluid flow rates. This
adjustment is usually needed when the natural frequency of the actuator is less
than the 90º phase lag frequency of the servovalve. The servovalve 90º phase lag
frequency can be found in the servovalve product literature.
The natural frequency can be approximated with the following formula:
•
If the system response deteriorates when adding delta P, then change the
polarity of the signal. If changing polarity does not improve system
response, try adjusting the stabilization filter.
•
Check all amplitudes for overshoot. Do not allow more than 10% overshoot
(preferably none) at any amplitude of a square wave response.
•
Delta P will not compensate for additional compliance from swivels,
linkages, test tables, and so forth. In this case, a mass accelerometer signal
from an accelerometer may be used in place of a delta P signal for
stabilization.
Actuator Frequency
CA
WV
---------
=
C = constant for English (2500) or metric units (1060)
A = actuator piston area expressed as in
2
(cm
2
)
W = any directly coupled mass including the actuator piston mass
expressed in lbs (kg)
V = hydraulic fluid volume contained inside the actuator and
manifold expressed as in
3
(cm
3
)
Where: