Task 8 establish the shunt calibration reference – MTS Series 793 User Manual
Page 182
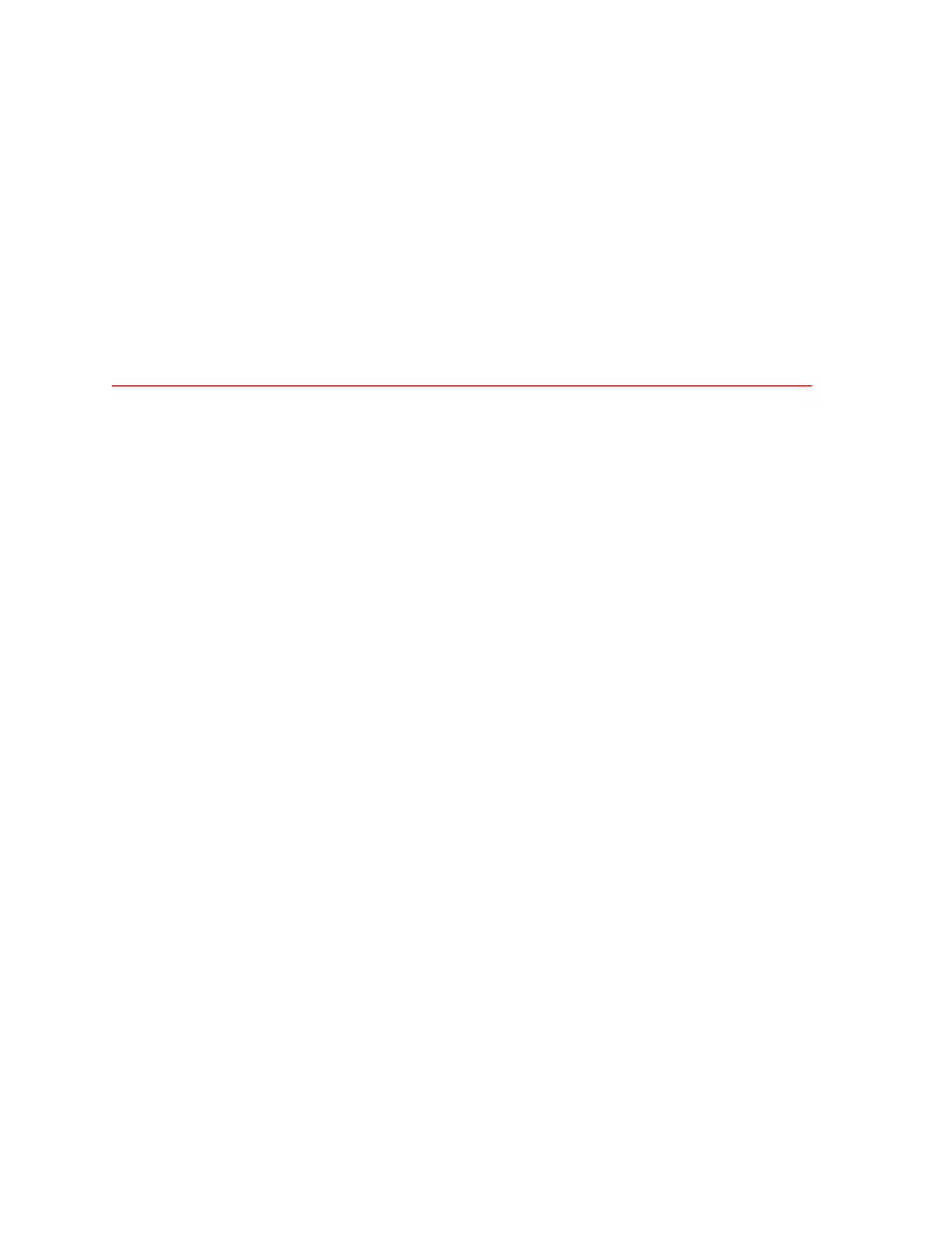
MTS Series 793 Tuning and Calibration
Force Sensor Calibration
Calibration Procedures
182
A. Enter the full scale force values in the Fullscale Min/Max entry boxes.
B. Adjust Neg Tension for the required tension sensitivity value (+mV/
V).
C. Adjust Pos Compression for the required compression sensitivity
value (-mV/V).
D. Adjust Excitation for the required calibration excitation value (DC).
Task 8
Establish the shunt calibration reference
Each resistive bridge type transducer (DC sensor) uses a shunt resistor to check
the calibration accuracy of the sensor/conditioner combination. Each DC
conditioner supports a shunt resistor.
1. Turn off hydraulic power.
2. Remove the load standard.
3. Turn on hydraulic power.
4. Zero the force sensor output.
Standalone FlexTest SE Controllers:
Adjust the Setpoint for a 0 kN output. The sensor output must be 0.000 kN
for a proper shunt calibration. If not, return to
“Set the zero and offset”
on
page 163.
Automated Controllers:
Adjust the Manual Cmd slider on the Manual Command window for a 0
kN output. The sensor output must be 0.000 kN for a proper shunt
calibration. If not, return to
“Set the zero and offset”
on page 163.
5. Change the control mode to displacement.
Standalone FlexTest SE Controllers: Select Status > Control Mode >
Disp.
Automated Controllers: On the Manual Command window, change
Control Mode to Displacement.
Shunt calibration cannot be performed on a sensor when it is in control of
the servo loop.