3 correcting for position deviation, 4 operation check after replacing the motor – IAI America SSPDACR User Manual
Page 97
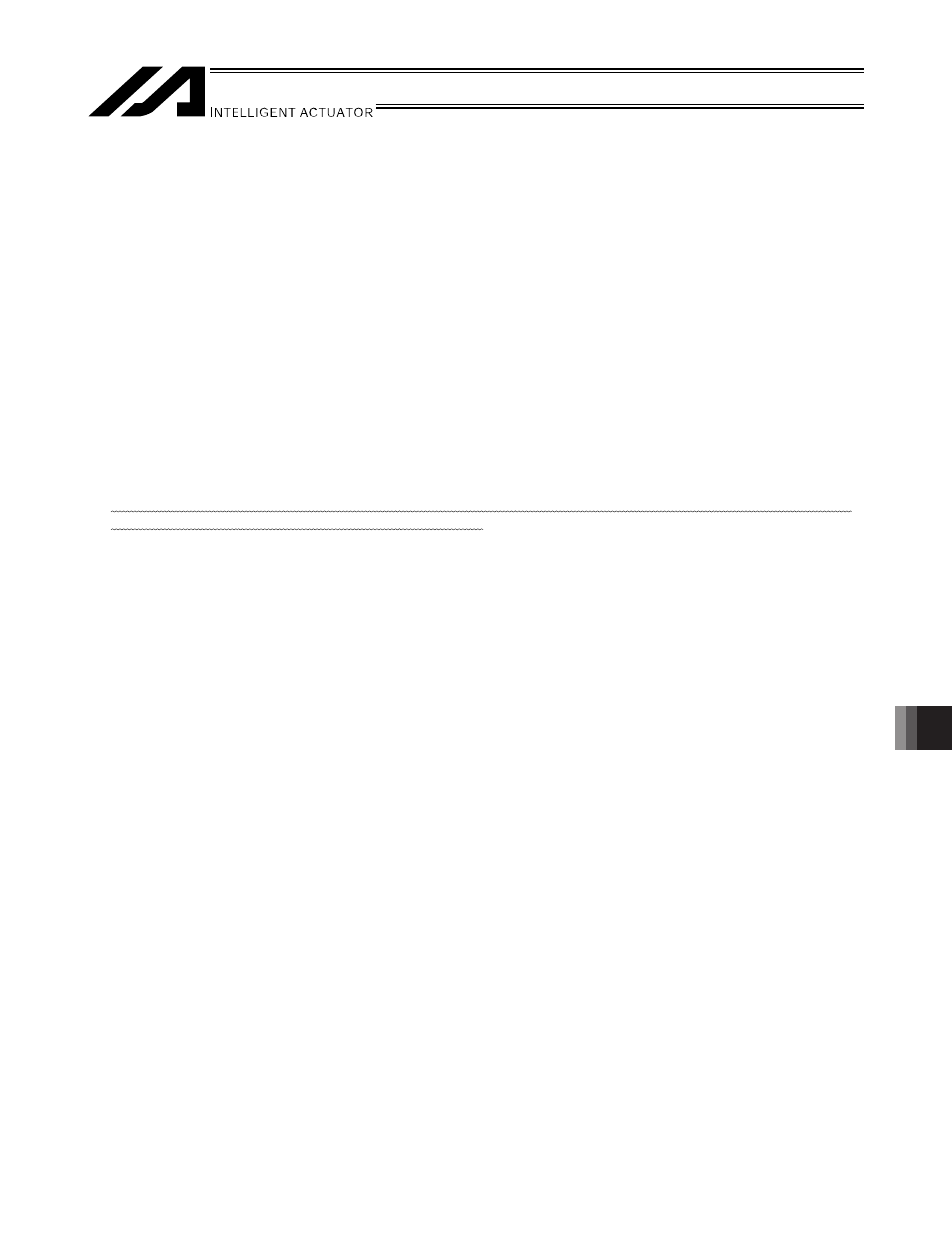
14. Motor Replacement Procedures
89
14.3 Correcting for Position Deviation
(1) Connect the motor cable and encoder cable and turn on the controller power.
(2) Use the PC software or teaching pendant to perform homing and check the home position. Repeat homing
several times to confirm that the actuator returns to the same position.
(If the actuator is of absolute specification, perform an absolute reset.)
(3) Check the amount of position deviation.
The position may have changed slightly from where it was before the motor was replaced.
Accordingly, select a desired position number that allows you to check the amount of deviation before and
after the replacement, and then perform positioning to that position and measure the amount of deviation.
(4) Reflect the deviation in the home preset parameter in the case of an X-SEL/SSEL controller, or in the home
return offset parameter in the case of an SCON controller. [For the setting method, refer to 9.5, “Fine-tuning
the Home Position.”]
* If the two positions differ significantly (one ball screw revolution or more = lead or more) or if the actuator does
not return to the same position when homing is repeated, install the motor unit again by following the
procedure described in this manual.
When the motor unit was installed, a wrong spacer size may have been used or the slider may have moved
instead of remaining stationary at the mechanical end.
14.4 Operation Check after Replacing the Motor
After replacing the motor, perform continuous operation to confirm absence of vibration or abnormal noise.