Fairbanks FB2550 SERIES User Manual
Page 119
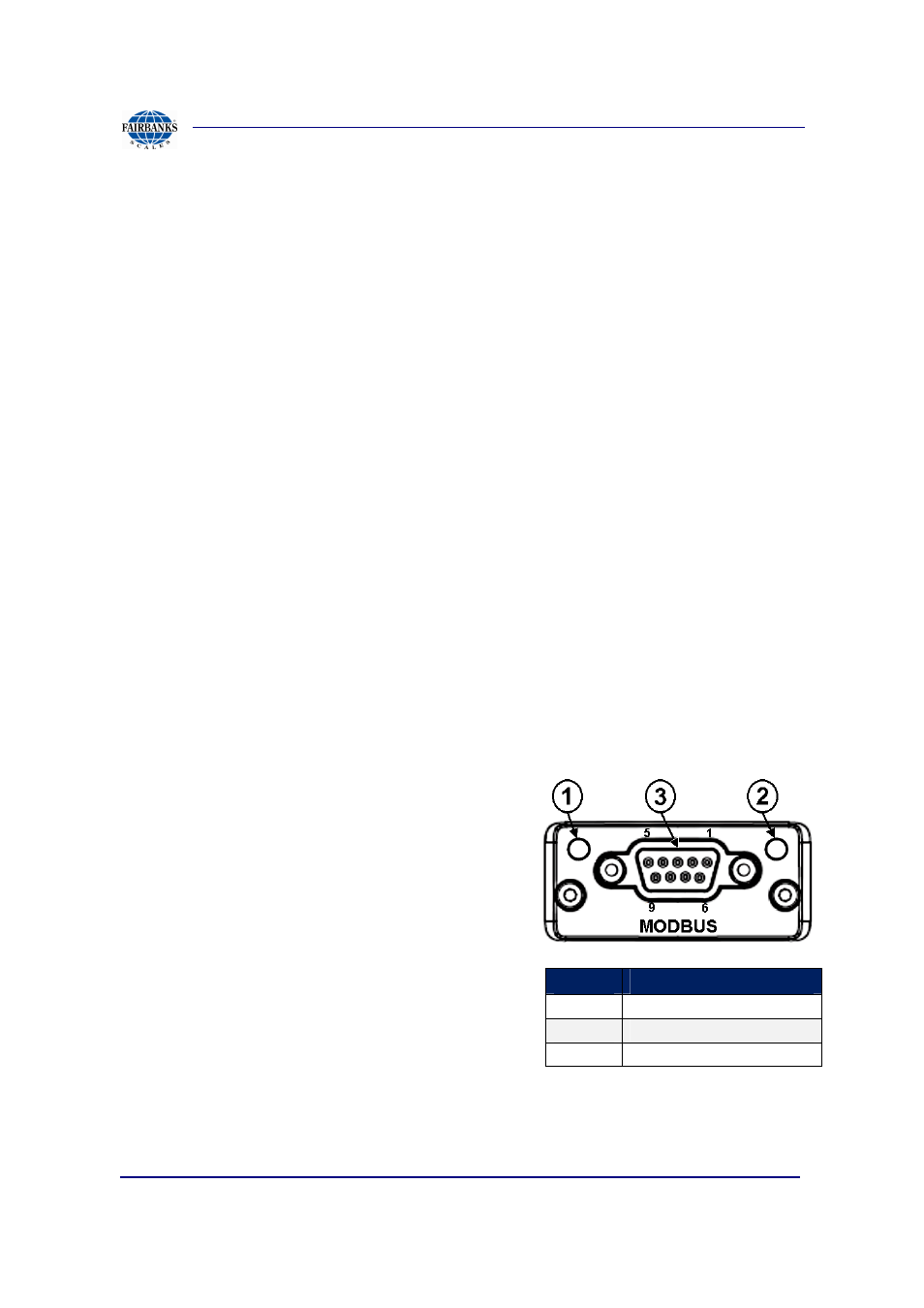
Section 5: Input/ Output
07/2012
119
51254 Rev. 3
5.15.4. MODBUS (
30925
)
MODBUS PROTOCOL
was originally developed in 1978 to exchange
information between devices on the factory floor.
It developed into the standard for exchanging data and communication
MODULE
STATUS
– information between PLC systems.
– Modbus devices communicate over a Serial Network in a master/slave
(request/response) type relationship.
– Uses either the ASCII (American Standard Code for Information Interchange)
mode or the RTU (Remote Terminal Unit) mode.
In the
ASCII MODE
, two eight-bit bytes of data are sent as two ASCII characters.
– The primary advantage of ASCII mode is the flexibility of the timing sequence.
– Up to a one second interval can occur between character transmissions
without causing communication errors.
In the
RTU MODE
, data is sent as two four-bit, hexadecimal characters, providing
for higher throughput than in ASCII mode for the same baud rate.
– Modbus Plus communicates using a single twisted pair of wires in one
shielded cable (#18AWG).
– Modbus Plus does NOT provide power on the network.
Maximum of up to 32 Nodes, and up to 64 with a Repeater.
No.
DESCRIPTION
1
Communication LED
2
Device Status LED
3
Modbus Interface