Preparatory instructions, 12 preparatory instructions, Positioning and control functions – Parker Products COMPAX-M /-S (L) User Manual
Page 101: Posr speed
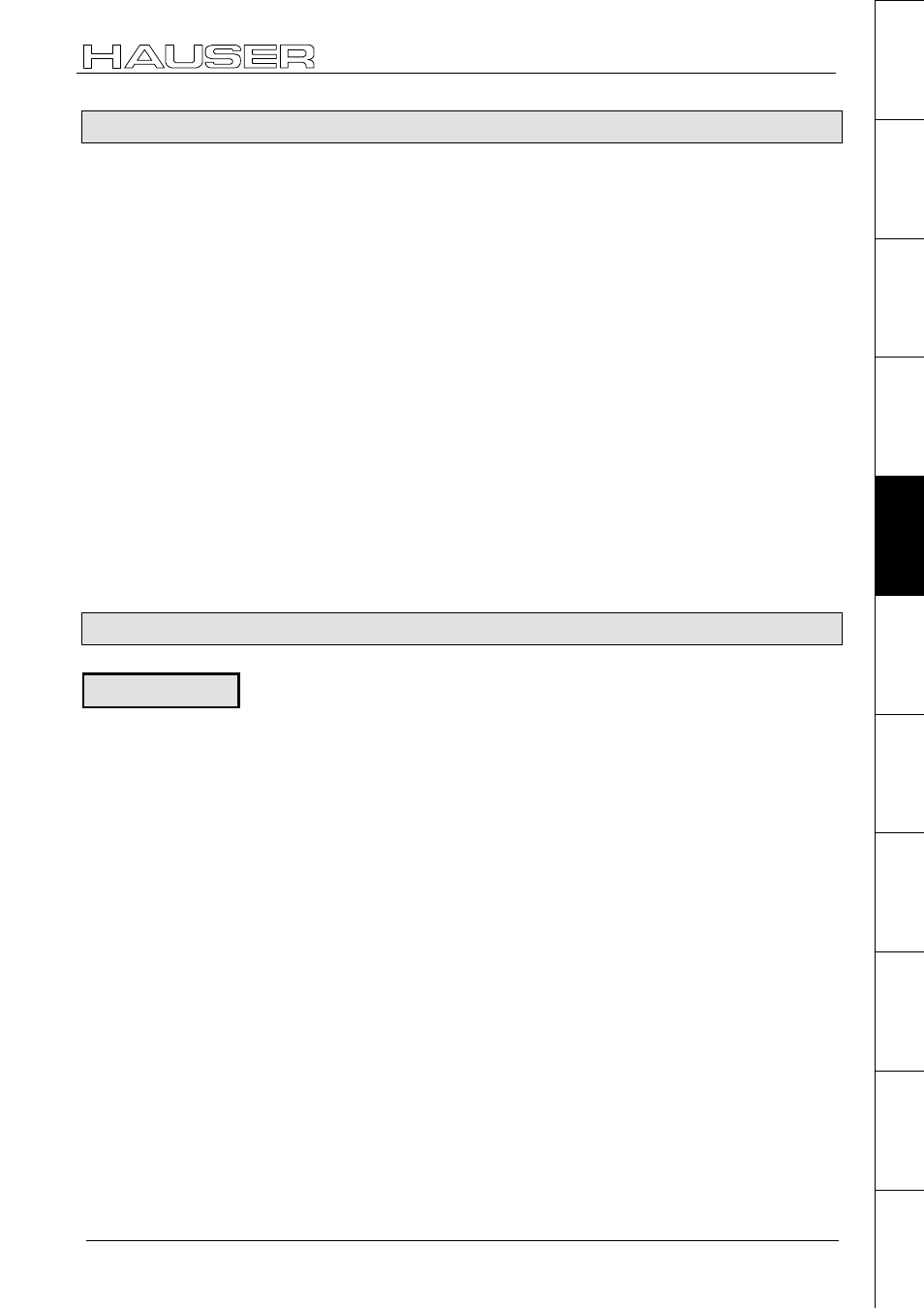
Positioning and control functions
Preparatory instructions
101
Unit
hardware
Connector
assignment / cable
Technical data
Configuration
Positioning and
control functions
Optimization
functions
Interfaces
Accessories /
options
Status
Parameter
Error list
8.4.12 Preparatory instructions
The following command combinations are preparatory instructions for creating
speed step profiles or setting comparator switch points . The prepared positioning
process is started using POSA or POSR. Note the following:
♦
Combined commands can be mixed (POSR SPEED, POSR OUTPUT).
♦
A total of 8 combined commands can be programmed per positioning process.
♦
The positioning values of the command combinations are always positive and
refer to the start point of the positioning process. They represent differences in
travel. The direction is specified by the next positioning command. This can be
relative (POSR) or absolute (POSA) . Meaning:
♦
The positioning values for speed steps, ramp times or comparators always apply
from the point at which positioning starts (for POSA and POSR)
♦
The positioning values for speed steps, ramp times or comparators are numerical
values:
♦
If the following positioning is positive, COMPAX calculates them as positive
values.
♦
If the following positioning is negative, COMPAX calculates them as negative
values.
♦
If a process cycle has been interrupted by "Stop", continue the cycle using
"Start".
♦
The preparatory instructions are canceled by the "Hand+/-", "Find machine zero"
and "Approach real zero" commands.
8.4.13 Changes in speed within a positioning process [POSR SPEED]
Each speed step profile can have a maximum of 8 speed steps. The comparator
value is specified as a relative dimension. It is referenced to the positioning start
point.
POSR value 1 SPEED value 2
Value 1: only positive values permitted (unit corresponds to P90); two digits after
the decimal point (three for inches), a control parameter (P40..P49) or a
variable V1 ... V39.
Value 2: no digits after the decimal point; numerical value, a control parameter
(P40..P49) or a variable V1 ... V39.
e.g.: POSR .P40 SPEED .P41
N001: ACCEL 250
Acceleration and braking time = 250 ms
N002: SPEED 20
Starting velocity = 20%
N003: POSR 150 SPEED 30
1st speed step when starting position
±
150, sets velocity to
30%.
N004: POSR 300 SPEED 50
2st speed step when starting position
±
300, sets velocity to
50%.
N005: POSR 500 SPEED 80
3st speed step when starting position
±
500, sets velocity to
80%.
N006: POSR 900 SPEED 60
4st speed step when starting position
±
900, sets velocity to
60%.
N007: POSA -1000
Positioning command to position -1000 (position -1000 is
approached with all of or one part of the speed step profile
depending on the start point).
N008: POSR 200 SPEED 50
Prepares a new speed step profile.
N009: ...
POSR SPEED
Syntax:
Example: