HP 30 HP30 User Manual
Page 115
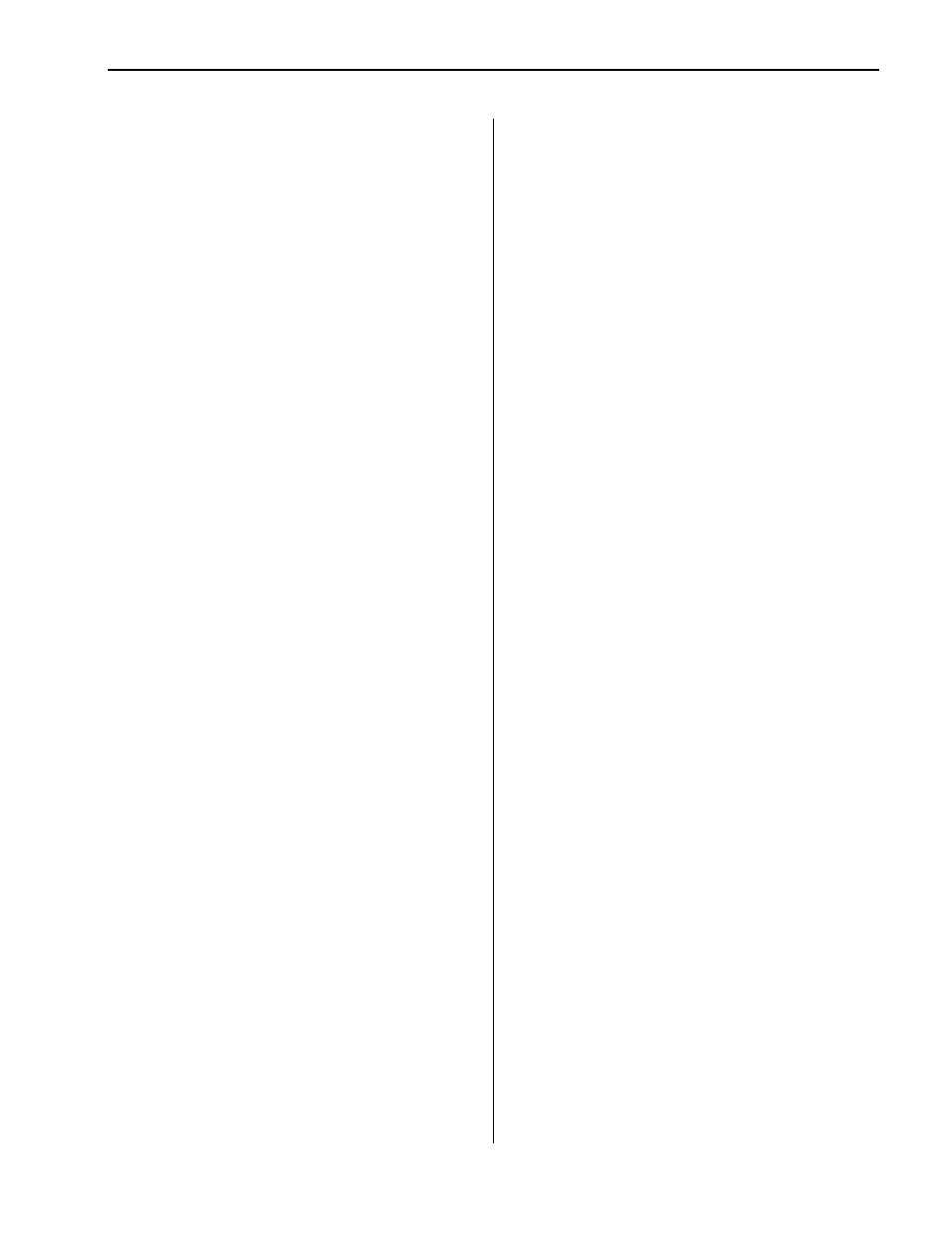
Chapter 6 - Parameter Description [FU2]
6-23
Conditions for Sensorless Vector Control
Conditions for sensorless control are as follows. If one of
the following conditions is not satisfied, the inverter may
malfunction with insufficient torque, irregular rotation, or
excessive motor noise. It is recommended to use V/F
control.
Use a motor capacity that is equal to or one
horsepower level lower than the inverter capacity.
Two different motor parameters can be set for one
inverter, but use only one motor parameter for
sensorless control.
If the motor in use is not
CMC 220V/440V Class motor
or
using 220V/380V dual use motor, utilize the auto
tuning feature in FU2-40 [Auto tuning] before starting.
Set appropriate values for the electronic thermal
function, the overload limit function and the stall
prevention. The set values should not exceed 150%
of the rated motor current.
When
DRV–04
[Frequency Mode] is set to “V1”, “I”, or
“V1+I”, eliminate any potential noise influence with
the frequency reference.
Pole number of the motor should be 2 pole, 4 pole, or
6 pole.
The distance between the inverter and the motor
should not exceed 100m (328 ft).
Precautions When Using Sensorless Control
Forced-cooling should be used for the motor when
the average operating speed is under 20Hz and more
than 100% load is used constantly.
The motor may rotate 0.5% faster than the maximum
speed if the motor temperature does not reach
normal operating temperature.
The performance can be improved during
regeneration for systems with frequent acceleration
and deceleration operations by installing the DB
(Dynamic Brake) braking unit option.
Utilize the auto-tuning feature when the motor
reaches normal temperature (average temperature
where the motor normally operates).
Output torque may be reduced when an output filter
option is used between the inverter and the motor.
Speed change is more frequent than the V/F control.
If the speed changes excessively when the FU2–38
[Carrier Frequency Selection] is set to a value more
than 10kHz, change the setting to 5~10kHz.
Over current fault can occur if the FU2-41 [Stator
Resistance (Rs)] is set to a value more than twice the
auto tuned value
Max setting range is
300 Hz.
Detail Tuning Method for Sensorless Vector Control
Adjust the
FU2–34 [No Load Motor Current (RMS)]
value
larger or smaller by 5% units if the current is larger or
smaller than that of V/F control with small load.
Adjust the
FU2–32
[
Rated Motor Slip
] value larger or
smaller by 5% units if the speed is faster or slower
than that of V/F control with small load.
Sensorless_T(Sensorless Vector Torque) Operation:
Vector_TRQ(Vector control torque) Operation:
All settings are the same as Vector_SPD except
using torque reference for torque control.