HEIDENHAIN TNC 426 (280 476) User Manual
Page 6
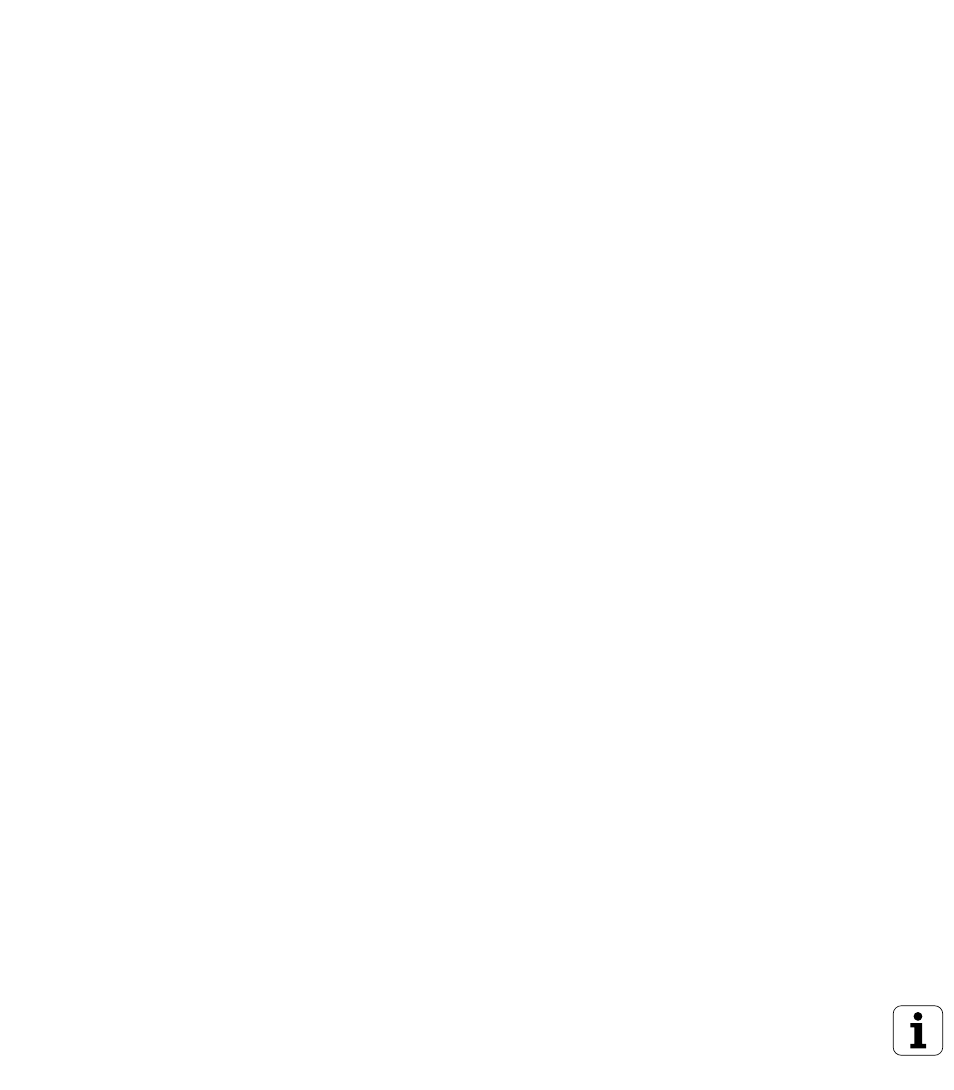
II
New features of the NC software 280 476-xx
n
Thread milling cycles 262 to 267 (see “Fundamentals of thread
milling” on page 235)
n
Tapping Cycle 209 with chip breaking (see “TAPPING WITH CHIP
BREAKING (Cycle 209)” on page 233)
n
Cycle 247(see “DATUM SETTING (Cycle 247)” on page 324)
n
Cycle run by means of point tables (see “Point Tables” on page 206)
n
Entering two miscellaneous functions M (see “Entering
Miscellaneous Functions M and STOP” on page 176)
n
Program stop with M01 (see “Optional Program Run Interruption”
on page 416)
n
Starting NC programs automatically (see “Automatic Program Start”
on page 414)
n
Selecting datum tables in the NC program (see “Selecting a datum
table in the part program” on page 322)
n
Editing the active datum table in the program run mode of operation
(see “Edit a pocket table in a Program Run operating mode.” on
page 323)
n
Selecting the screen layout for pallet tables (see “Screen layout for
executing pallet tables” on page 83)
n
New columns in the tool table for managing TS calibration data (see
“Entering tool data in tables” on page 101)
n
Management of unlimited calibration data with the TS triggering
touch probes (see User’s Manual for Touch Probe Cycles)
n
Cycles for automatic tool measurement with the TT tool touch probe
in ISO (see User's Manual for Touch Probe Cycles)
n
New Cycle 440 for measuring the axial displacement of a machine
with the TT tool touch probe (see User's Manual for Touch Probe
Cycles)
n
Support of Teleservice functions (see “Teleservice” on page 444)
n
Setting the display mode for blocks with more than one line, e.g. for
cycle definitions (see “MP7281.0 Programming and Editing
operating mode” on page 457)
n
New SYSREAD function 501 for reading REF values from datum
tables (see “FN18: SYS-DATUM READ Read system data” on page
373)
n
M140 (see “Retraction from the contour in the tool-axis direction:
M140” on page 188)
n
M141 (see “Suppressing touch probe monitoring: M141” on page
189)
n
M142 (see “Delete modal program information: M142” on page
190)
n
M143 (see “Delete basic rotation: M143” on page 190)
n