Tool change, 2 t ool d a ta – HEIDENHAIN TNC 426 (280 476) User Manual
Page 135
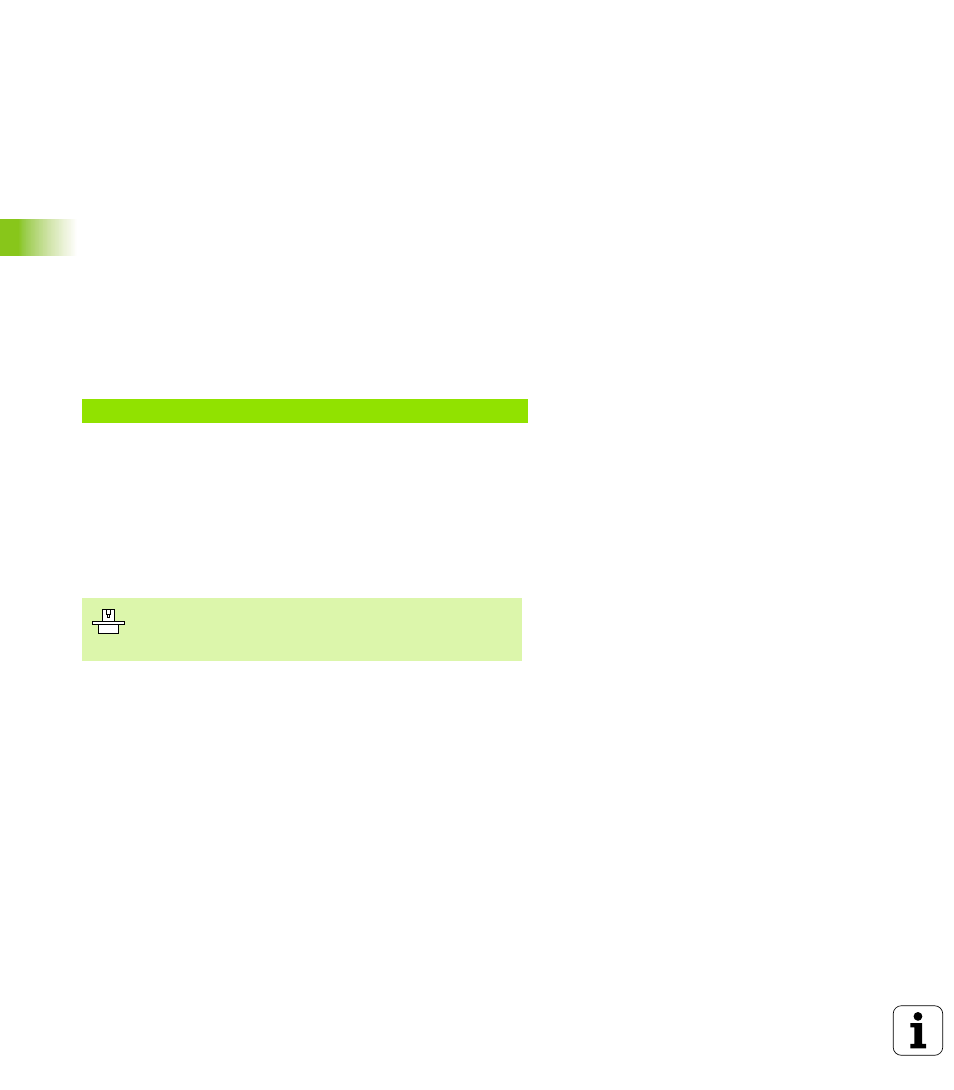
108
5 Programming: Tools
5.2 T
ool D
a
ta
7
7
7
7
Feed rate F:
Enter the feed rate directly or allow the
TNC to calculate the feed rate if you are working with
cutting data tables. Press the F CALCULATE
AUTOMAT. soft key. The TNC limits the feed rate to
the maximum feed rate of the longest axis (set in MP
1010). F is effective until you program a new feed rate
in a positioning block or a TOOL CALL block.
7
7
7
7
Tool length oversize DL:
Enter the delta value for
the tool length.
7
7
7
7
Tool radius oversize DR:
Enter the delta value for
the tool radius.
7
7
7
7
Tool radius oversize 2:
Enter the delta value for the
tool radius 2.
Example: Tool call
Call tool number 5 in the tool axis Z with a spindle speed 2500 rpm and
a feed rate of 350 mm/min. The tool length is to be programmed with
an oversize of 0.2 mm, the tool radius 2 with an oversize of 0.05 mm,
and the tool radius with an undersize of 1 mm.
The character D preceding L and R designates delta values.
Tool preselection with tool tables
If you are working with tool tables, use TOOL DEF to preselect the next
tool. Simply enter the tool number or a corresponding Q parameter, or
type the tool name in quotation marks.
Tool change
Tool change position
A tool change position must be approachable without collision. With
the miscellaneous functions M91 and M92, you can enter machine-
referenced (rather than workpiece-referenced) coordinates for the tool
change position. If TOOL CALL 0 is programmed before the first tool
call, the TNC moves the tool spindle in the tool axis to a position that
is independent of the tool length.
20 TOOL CALL 5.2 Z S2500 F350 DL+0.2 DR-1 DR2+0.05
The tool change function can vary depending on the
individual machine tool. The machine tool manual
provides further information.