3 cont our appr oac h and depar tur e – HEIDENHAIN TNC 426 (280 476) User Manual
Page 163
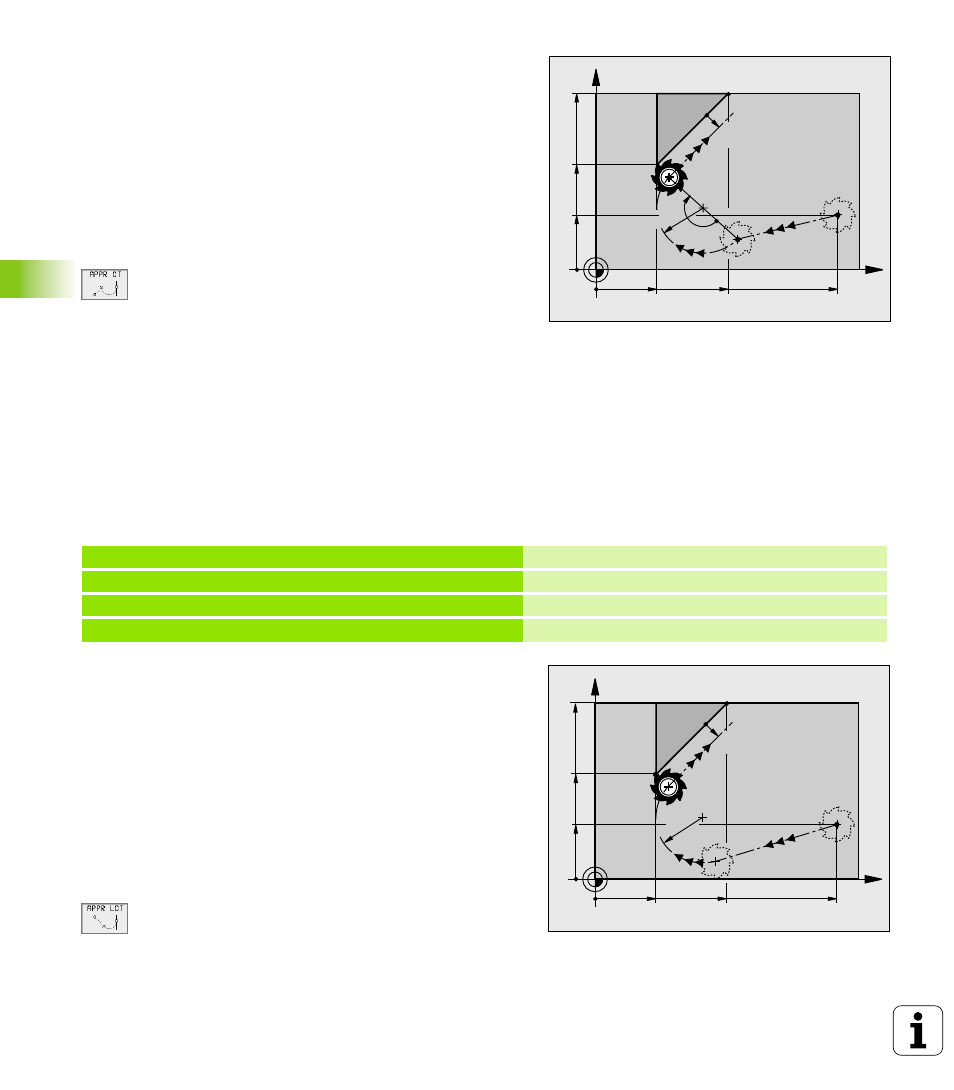
136
6 Programming: Programming Contours
6.3 Cont
our Appr
oac
h and Depar
tur
e
Approaching on a circular path with tangential
connection: APPR CT
The tool moves on a straight line from the starting point P
S
to an
auxiliary point P
H
. It then moves to the first contour point P
A
following
a circular arc that is tangential to the first contour element.
The arc from P
H
to P
A
is determined through the radius R and the
center angle CCA. The direction of rotation of the circular arc is
automatically derived from the tool path for the first contour element.
7
7
7
7
Use any path function to approach the starting point P
S
.
7
7
7
7
Initiate the dialog with the APPR/DEP key and APPR CT soft key:
7
7
7
7
Coordinates of the first contour point P
A
7
7
7
7
Radius R of the circular arc
n
If the tool should approach the workpiece in the
direction defined by the radius compensation: Enter
R as a positive value.
n
If the tool should approach the workpiece opposite
to the radius compensation:
Enter R as a negative value.
7
7
7
7
Center angle CCA of the arc
n
CCA can be entered only as a positive value.
n
Maximum input value 360°
7
7
7
7
Radius compensation RR/RL for machining
Example NC blocks
Approaching on a circular arc with tangential
connection from a straight line to the contour:
APPR LCT
The tool moves on a straight line from the starting point P
S
to an
auxiliary point P
H
. It then moves to the first contour point P
A
on a
circular arc.
The arc is connected tangentially both to the line P
S
– P
H
as well as to
the first contour element. Once these lines are known, the radius then
suffices to completely define the tool path.
7
7
7
7
Use any path function to approach the starting point P
S
.
7
7
7
7
Initiate the dialog with the APPR/DEP key and APPR LCT soft key:
7
7
7
7
Coordinates of the first contour point P
A
7
7
7
7
Radius R of the circular arc. Enter R as a positive value.
7
7
7
7
Radius compensation RR/RL for machining
X
Y
10
20
P
A
RR
P
S
R0
P
H
RR
RR
40
10
CCA=
180°
R10
35
20
7 L X+40 Y+10 RO FMAX M3
Approach P
S
without radius compensation
8 APPR CT X+10 Y+20 Z-10 CCA180 R+10 RR F100
P
A
with radius comp. RR, radius R=10
9 L X+20 Y+35
End point of the first contour element
10 L ...
Next contour element
X
Y
10
20
P
A
RR
P
S
R0
P
H
RR
RR
40
10
R10
35
20